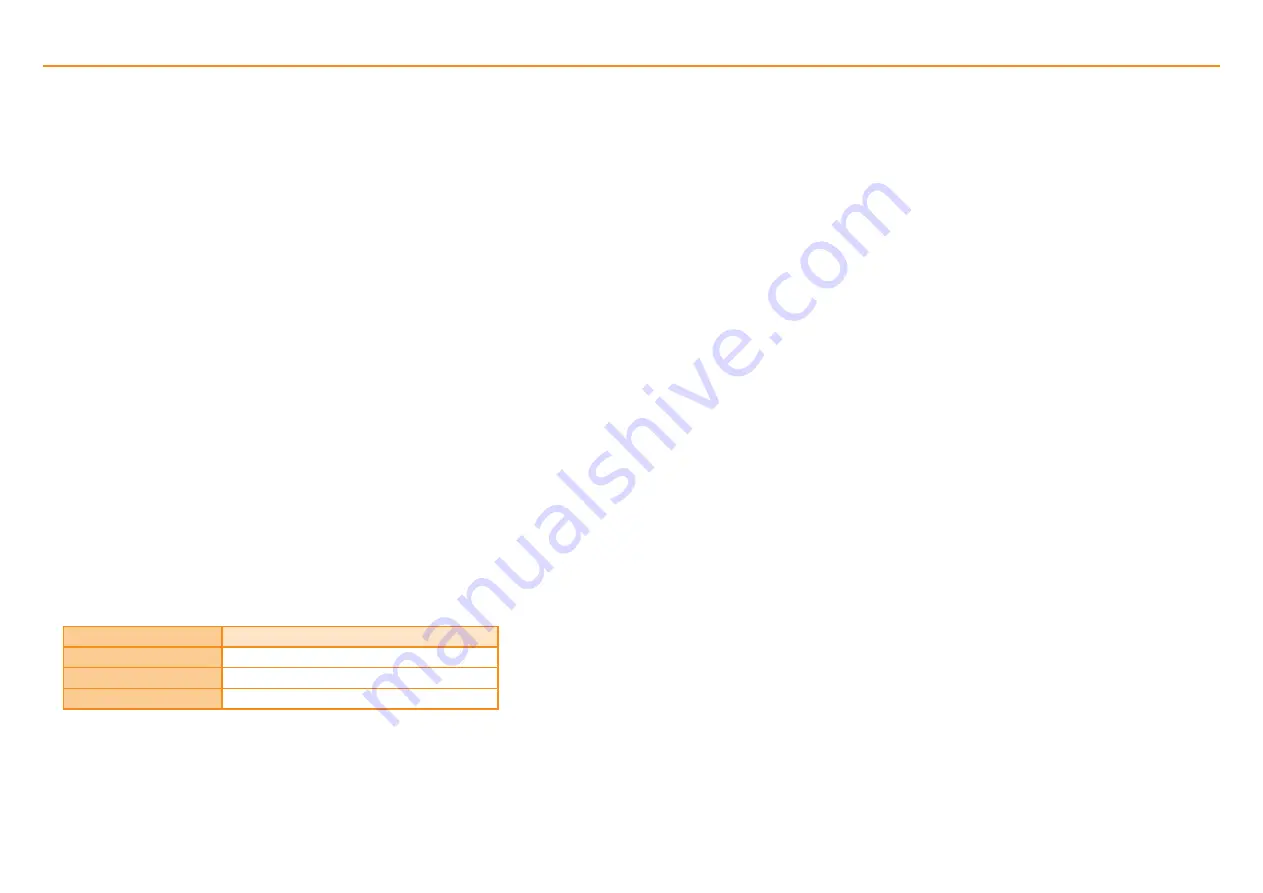
13
QUANTiC RTLC40 /
FASTRACK
installation guide
System calibration
NOTE:
The functions described below can also be carried out using the optional ADTi-100 and ADT View software. See
for more information.
Before system calibration:
u
Clean the scale and readhead optical window.
u
If reinstalling, restore factory defaults
(‘Restoring factory defaults’, page 14)
u
Maximise the signal strength along full length of travel (readhead set-up LED is flashing Green).
NOTE:
Maximum calibration speed 100 mm/s or less than the readhead maximum, whichever is slowest.
Step 1 – Incremental signal calibration
u
Cycle the power to the readhead or connect the ‘Remote CAL’ output pin to 0 V for < 3 seconds. The readhead will then single flash Blue to indicate it is in calibration mode as detailed in
‘Readhead mounting and alignment’, page 12
The readhead will only enter calibration mode if the LED is flashing Green.
u
Move the readhead at slow speed along the axis ensuring it does not pass a reference mark, until the LED starts double-flashing indicating the incremental signals are now calibrated and the new settings are stored in
the readhead memory.
u
The system is now ready for reference mark phasing. For systems without a reference mark, cycle the power to the readhead or connect the ‘Remote CAL’ output pin to 0 V for < 3 seconds to exit calibration mode.
u
If the system does not automatically enter the reference mark phasing stage (LED continues single flashing) the calibration of the incremental signals has failed. After ensuring failure is not due to overspeed (> 100 mm/s,
or
exceeding the readhead maximum speed), exit the calibration routine, restore factory defaults as detailed below, and check the readhead installation and system cleanliness before repeating the calibration routine.
NOTE:
For analogue variants of QUANTiC ensure correct termination of output signals
(‘Recommended signal termination’, page 19)
.
Step 2 – Reference mark phasing
u
Move the readhead back and forth over the selected reference mark until the LED stops flashing and remains solid Blue. The reference mark is now phased.
NOTE:
Only the chosen reference mark that has been used in the calibration routine is guaranteed to remain phased.
u
The system automatically exits the calibration routine and is ready for operation.
u
AGC and AOC are automatically switched on once calibration is complete. To switch off AGC refer to
‘Switching Automatic Gain Control (AGC) on or off’, page 14
.
u
If the LED continues double-flashing after repeatedly passing the chosen reference mark it is not being detected.
•
Ensure that the correct readhead configuration is being used. Readheads can either output all reference marks or only output a reference mark where a reference selector magnet is fitted depending on the options
chosen when ordering.
•
Check reference mark selector magnet is fitted in the correct location relative to readhead orientation
(‘RTLC40 / FASTRACK installation drawing’, page 4)
.
Calibration routine manual exit
u
To exit the calibration routine at any stage cycle the power to the readhead or connect the ‘Remote CAL’ output pin to 0 V for < 3 seconds. The LED will then stop flashing.
LED
Settings stored
Blue single flashing
None, restore factory defaults and recalibrate
Blue double flashing
Incremental only
Blue (auto-complete)
Incremental and reference mark