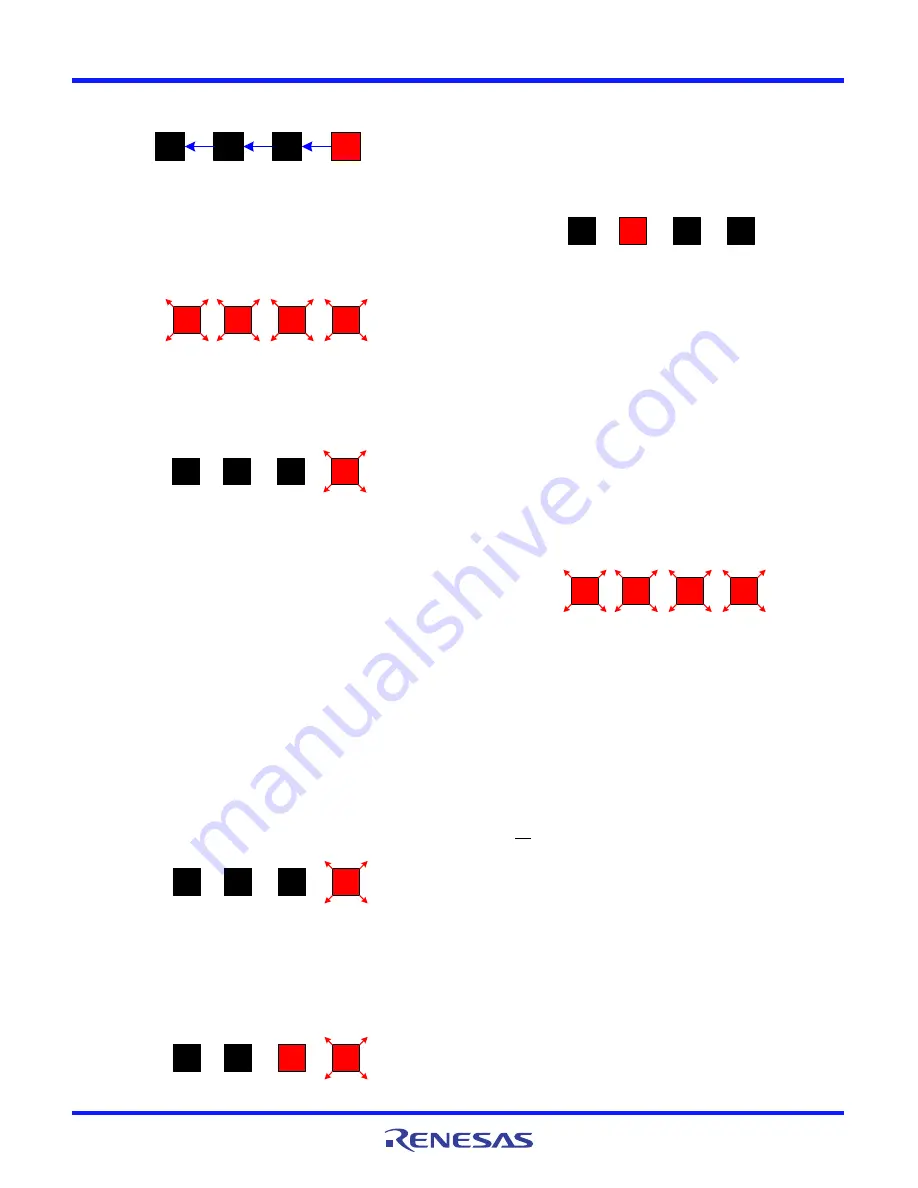
AN1899 Rev 0.00
Page 4 of 24
January 8, 2014
HIP2103-4DEMO1Z
9. Turn on the lab supply. Set SW1 (toggle switch) on. Observe
that the four LEDs turn on and off, one after another.
This initial flash of the LEDs indicates that power has been
applied. After the initial flash, all LEDs will be off. Operation
of the motor is now possible. If all four LEDs are flashing
simultaneously, SW6 is not configured correctly. Reconfigure
SW6 then turn off, then on, the toggle switch to restart.
10. Press the Start/Stop push button once. The RUN LED (led1)
will blink indicating that the motor has been started. The
motor at this point may not be rotating because minimal
voltage is being applied to the motor.
11. Slowly increase the voltage on the motor by rotating the
potentiometer, R13, to the right (CW). At some point the
motor will start to rotate slowly. The actual starting voltage is
dependent on the specific motor being used.
12. If the motor is vibrating back and forth instead of rotating, it
is possible that the Hall sensors or the motor leads were not
connected correctly. If the correct switching sequence has
been selected, all that should be necessary to correct this
misbehavior is to swap two of the motors lead (or to swap two
of the Hall sensor leads).
13. Continue to rotate the pot until the motor is running at a
moderate speed of roughly 25%. Do not run the motor with
maximum voltage until the setup check-out is completed.
14. Press again the START/STOP push button. The motor will free
wheel to a stop and the blinking led1 will turn off.
15. Press again the START/STOP button. The motor will
accelerate to the previous run speed (assuming that the
potentiometer was not rotated). The blinking led0 will also
turn on.
16. While the motor is running, press the REVERSE button. The
RUN LED (led1) will turn off and the REVERSE LED (led2) will
turn on without blinking. After a short pause while the motor
is freewheeling to a stop, the motor will restart rotating in the
opposite direction. The RUN LED will be blinking and the
REVERSE LED will continue to be on.
17. Press again the REVERSE button. As before, the motor will
stop. But this time the REVERSE LED will turn off. After a
pause, the motor will restart but this time rotating in the
forward direction.
18. While the motor is running, the motor can be hard braked by
pressing the BRAKE push button.
The BRAKE LED (led3) will be on without blinking. When the
motor is restarted, the BRAKE LED will turn off.
CAUTION: This braking method turns on simultaneously all of
the low side bridge FETs. This will force the motor to a very
rapid stop. It the motor is loaded, or if the motor is not
designed for a rapid stop, mechanical damage to the motor
or to the load can result. If you are not sure about using this
braking method, only apply the brake when the motor speed
is relatively slow.
19. If, while operating the motor turns off, and all 4 LEDs are
blinking, the current limit shut-down has been activated after
255 consecutive pulse-by-pulse current limits. This may
happen if the motor speed (with load) is accelerated too
quickly, or if there is a fault with the motor or connections, or if
the motor is stalled. The iLimit LED will turn on momentarily by
itself if the overcurrent duration is less than 255 pulse-by-pulse
current limits.
It is now safe to proceed with testing at higher power levels or
speeds.
DC Motor Setup (Full Bridge)
The HIP2103-4DEMO1Z can also be used to drive a conventional
brushed DC motor. The setup procedure is essentially the same
as the BLDC configuration except that Hall sensor inputs are not
used and only two motor connections are used, MB (TB4) and MC
(TB5). When configured in a full bridge topology, phase A (MA) is
disabled by setting the corresponding HIP2103 to sleep.
To setup the motor driver for a full bridge topology, set SW6:2 to
on and switches SW6:0, 3, 4 to off. Refer to Table 1 for complete
configuration details for SW6.
As with the BLDC configuration, the motor rotation direction can
be controlled. But unlike the BLDC configuration, the motor can
be reversed even if it has not yet stopped rotating. Be cautious
when reversing the motor before it has stopped rotating.
The motor can also be braked by grounding both motor leads
similar to the BLDC motor.
DC Motor Setup (Half bridge)
The HIP2103-4DEMO1Z can also be used to drive a conventional
brushed DC motor with a half bridge Topology. The setup
procedure is essentially the same as the BLDC configuration
except that Hall sensor inputs are not used and only two motor
connections are used, MB (TB5) and the negative connection of
led1
led3
led2
At initial turn on, leds will turn on and
off one at a time starting with led1
led4
led1
led3
led2
led4
SW6 is not configured corrrectly
led1
led3
led2
While the motor is rotating, the RUN LED is blinking
RUN
REVERSE
BRAKE
led4
i LIMIT
led1
led3
led2
RUN
REVERSE
BRAKE
led4
i LIMIT
led1
led3
led2
RUN
REVERSE
BRAKE
led4
i LIMIT
led1
led3
led2
RUN
REVERSE
BRAKE
led4
i LIMIT
led1
led3
led2
RUN
REVERSE
BRAKE
led4
i LIMIT