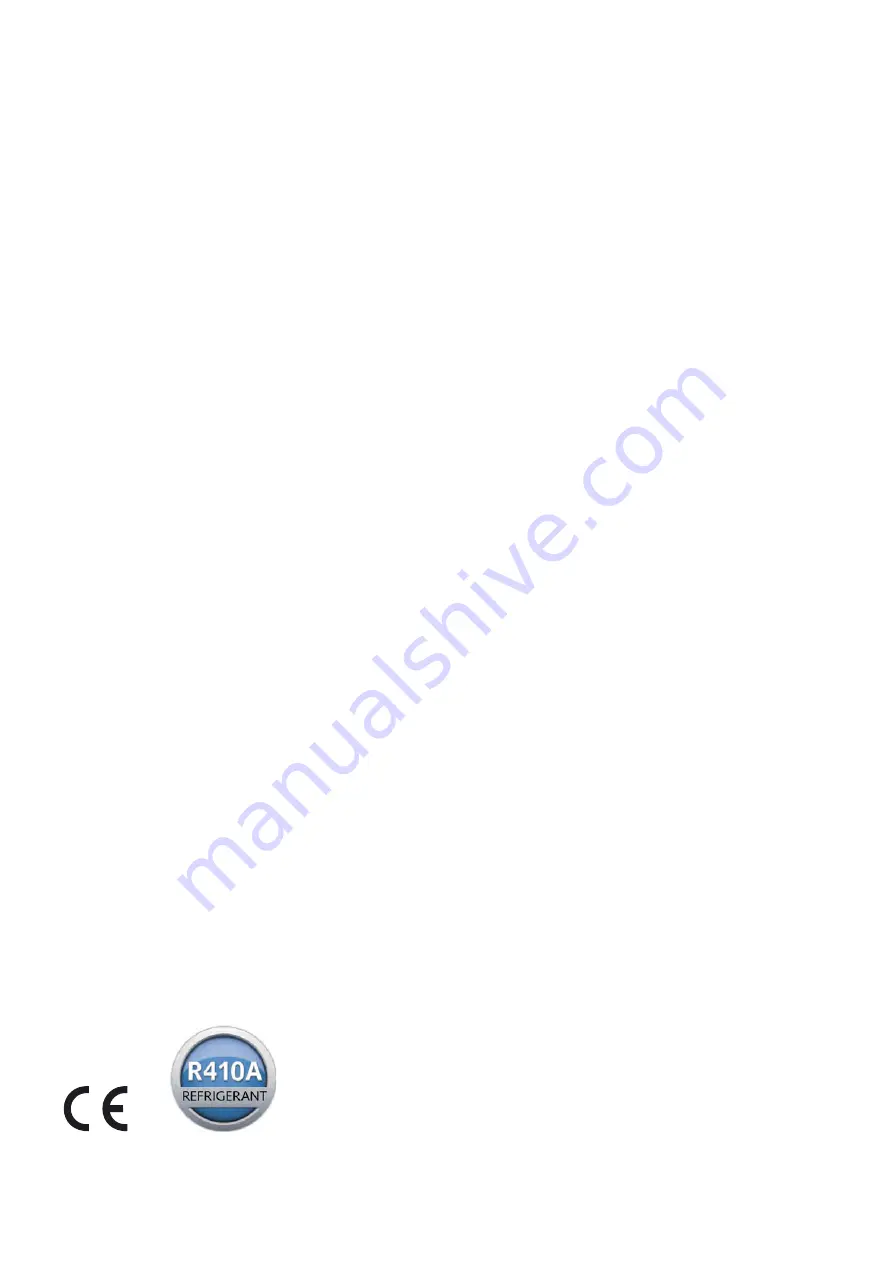
Installation and operating instructions (translation of the orig-
inal)
Read these operating instructions carefully before commis-
sioning / using this device!
These instructions are an integral part of the system and must
always be kept near or on the device.
Subject to modifications; No liability accepted for errors or mis-
prints!
Summary of Contents for RXT 1053 DC
Page 62: ...Resistance values for probes T1 T2 T3 and T4 K Ohm K Ohm K Ohm K Ohm REMKO RXT DC 62 ...
Page 63: ...Resistance values for probe T5 K Ohm K Ohm K Ohm K Ohm 63 ...
Page 70: ...No Designation 31 Cooling fin 32 Fin motor 33 Refrigerant connections cover REMKO RXT DC 70 ...
Page 82: ...REMKO RXT DC 82 ...
Page 83: ......