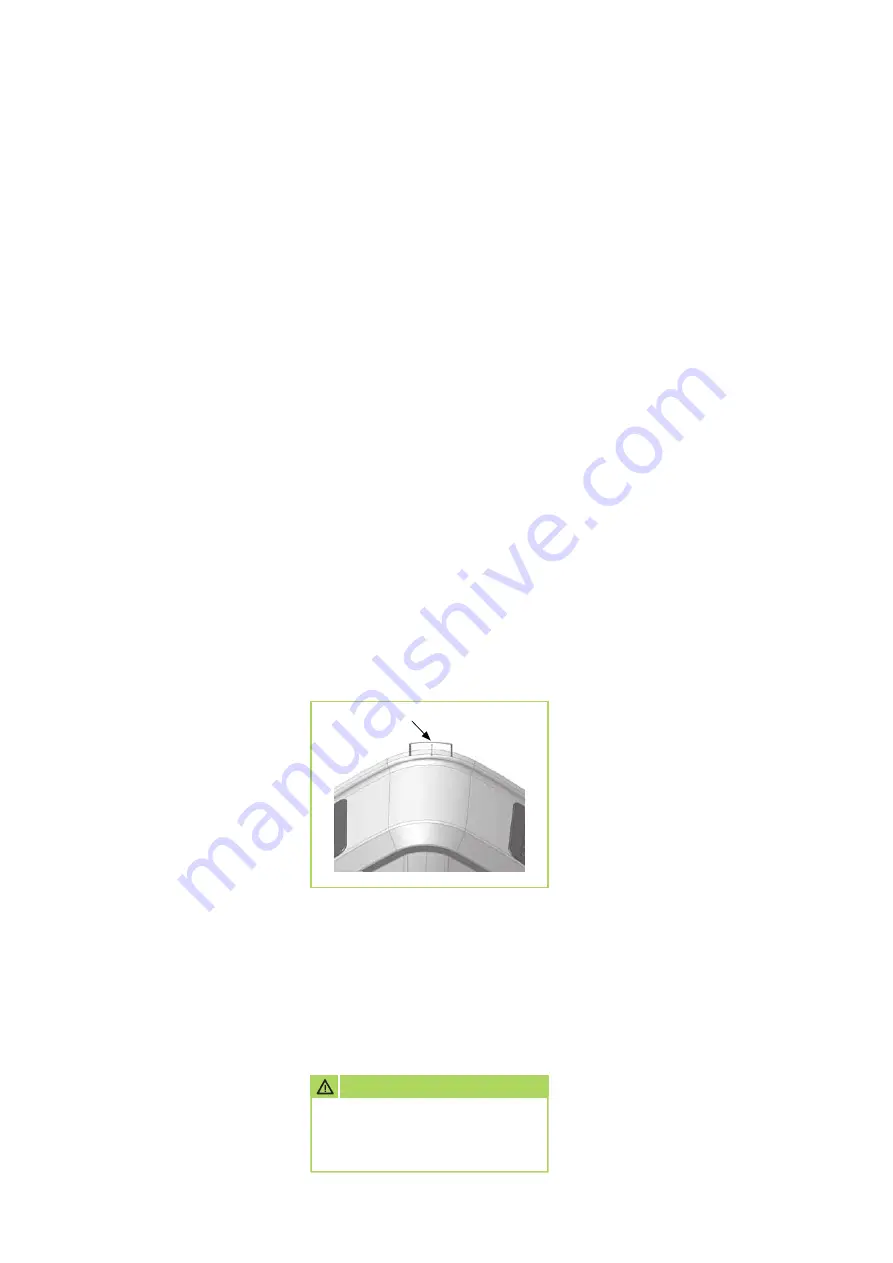
10
REMKO PWL
Set the switch of the respective
control unit to the „Off“ or „0“
position.
Precautions for extended periods
of non-use
■
Disconnect the electrical con-
nection in all poles.
■
Shut-off the hydraulic connec-
tion.
■
Where there is a risk of frost,
the entire system must be
drained if no suitable antifreeze
agent has been added to the
heating medium (water).
(See also page 9)
Decommissioning
Care and maintenance
ATTENTION
It does not suffice to switch off
the unit only via the switch!
During initial commissioning
During initial commissioning, all
regulating, control and safety
devices must be checked for their
proper functioning and correct
adjustment.
■
The power consumption of the
fan must be measured.
The nominal current must not
exceed the values on the rating
plate at the respective opera-
ting speeds.
■
Check the motor protection
function of the fan.
■
Check the complete system for
de-energised installation and
possible vibrations.
■
Check the heating/cooling
medium supply pipes for correct
connection, tightness and insu-
lation.
■
It must be ensured that no more
condensate is produced as in
this case the condensate pump
is also disconnected from the
supply and no longer operatio-
nal.
■
Wait for the fan to stop.
■
Shut-off the water circuit and
lock to prevent unauthorised
opening.
■
Allow the fin heat exchanger to
cool down.
Cleaning the units
■
The surfaces of the units must
be cleaned only dry or with a
moist cloth and a small amount
of soap solution if necessary.
■
Under no circumstances use
high-pressure cleaners or steam
jet equipment to clean the
mounted unit.
■
Do not use caustic cleaning
agents or those containing
solvents.
■
Only suitable cleaning agents
must be used even to remove
heavy fouling.
■
Clean all air inlets and air outlet
louvres.
■
Clean the fan impeller. If ne-
cessary, remove the motor or
protection grille.
■
Clean the heat exchanger fins
either by blowing out, suction
or with a soft brush.
The units generally require no
maintenance. The units and fin
exchanger surfaces must be vi-
sually inspected every six months
and before the start of the heating
period.
In dust-laden environments, the
units must be inspected at shorter
intervals.
For this purpose, the cover of the
unit must be detached from the
supporting part of the unit by re-
moving the 3 securing clips at the
corners.
For inspection purposes, the cover
must be held under the supporting
part with the aid of holding straps.
The cover can be removed com-
pletely from the unit if required by
loosening the strap adjuster on the
holding straps.
During removal, it must be en-
sured that the suction hose and
condensate pump sensor are also
disconnected from the supporting
part.
Securing clip
Important precautions to be taken
prior to all maintenance
■
The units must be disconnected
from the supply in all poles and
locked to prevent unauthorised
reconnection.
Summary of Contents for PWL 101-3
Page 2: ......