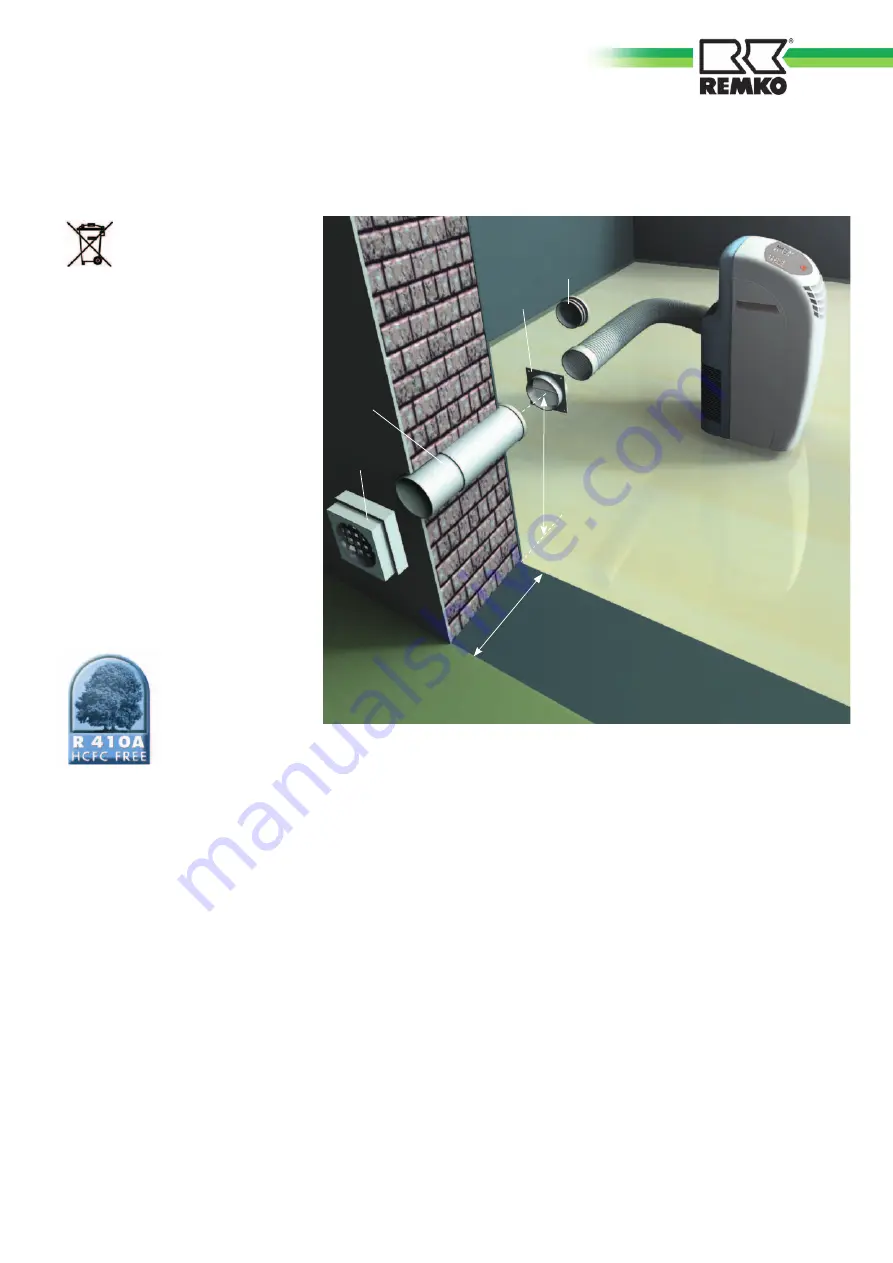
10
Protective
grille
Sealing cap
Telescopic
pipe
min. 400 mm
Trap
max. 480
mm
Environment and Recycling
■
Dispose of the packaging in an
ecofriendly manner.
■
Do not dispose of the device in
domestic rubbish.
■
Both the refrigerant and the plant parts
are subject to special disposal
conditions.
■
The refrigerant used belongs to the
chlorofluorocarbon refrigerant group. If
it is released into the air due to damage
to the cooling circuit, injury to the respi-
ratory organs of people and animals will
not occur.
Installation Instructions for the Wall
■
Create a core hole in the outside wall
(max.- wall thickness of 480 mm) with a
diameter of at least 135 mm.
■
Take the minimum distance of 430 mm
between the floor (mounting surface of
the device) and the centre of the wall
bushing into consideration.
■
Insert the telescopic pipe into the wall
bushing
■
To prevent cold bridges, insulate the
telescopic pipe with suitable insulating
material.
■
Wall the telescopic pipe into the core
hole in such a way that it is flush to both
sides of the wall.
■
Mount the protection grill on the out-
side of the wall (make sure it is protect-
ed from rain).
■
Fix the trap to the inside.
■
The “top“ label on the trap must be
legible from the inside!
■
When taking the device out of service,
for example, at the beginning of winter,
close the opening of the trap using the
sealing cap to prevent air circulation.
Fig. 19
Installation diagram
for the wall bushing
Disposal of the old
device
The unit production is subject to
continuous quality control.
Only high-quality materials are used,
the majority of which are recyclable.
You also contribute to environmental
protection by guaranteeing that your
old equipment is disposed of in an
environmentally friendly manner.
For this reason, bring the old equip-
ment only to an authorised recycling
company or to a corresponding
disposal site.