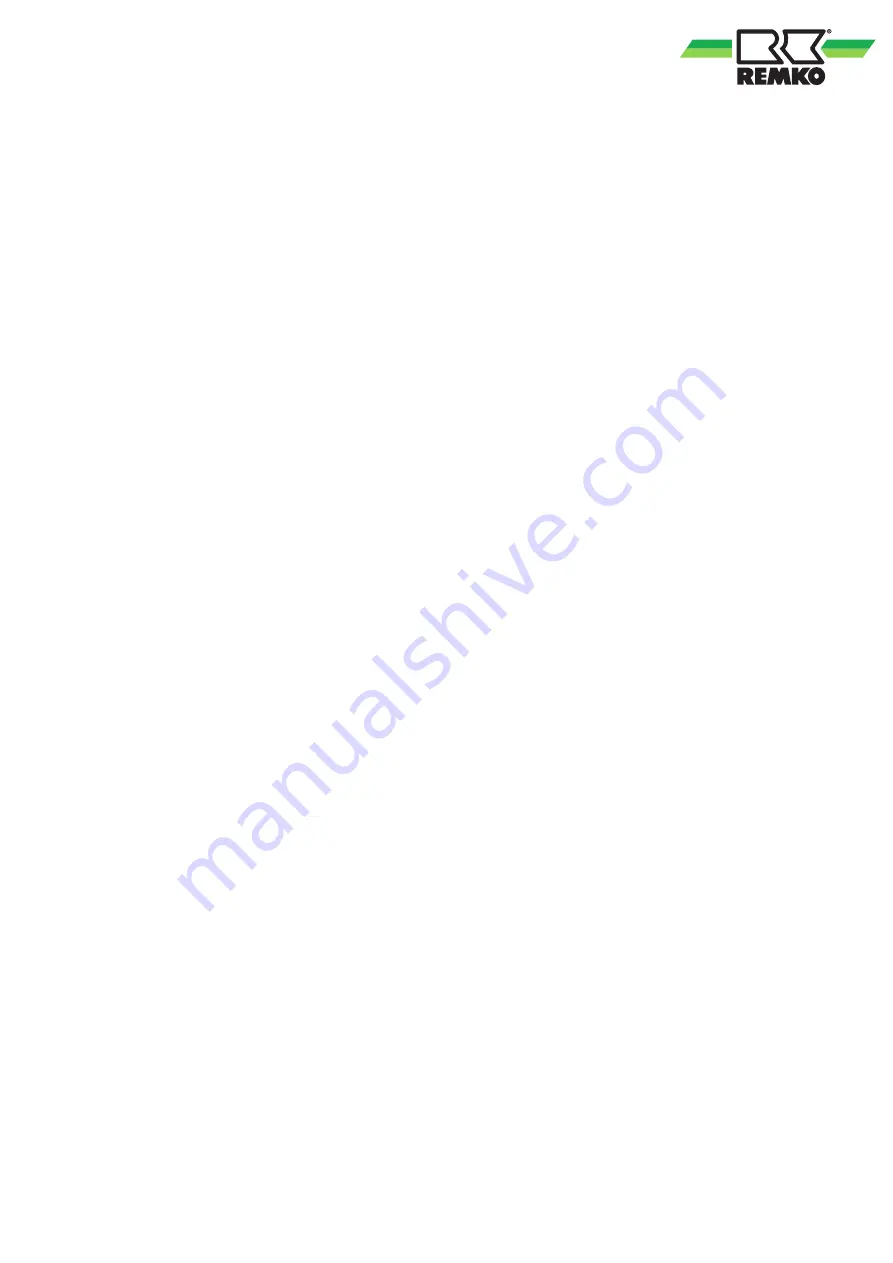
1.6 Safety notes for the operator
The operational safety of the units and compo-
nents is only assured providing they are used as
intended and in a fully assembled state.
n
The units and components may only be set up,
installed and maintained by qualified per-
sonnel.
n
Protective covers (grille) over moving parts
must not be removed from units that are in
operation.
n
Do not operate units or components with
obvious defects or signs of damage.
n
Contact with certain unit parts or components
may lead to burns or injury.
n
The units and components must not be
exposed to any mechanical load, extreme
levels of humidity or extreme temperature.
n
Spaces in which refrigerant can leak sufficient
to load and vent. Otherwise there is danger of
suffocation.
n
All housing parts and device openings, e.g. air
inlets and outlets, must be free from foreign
objects, fluids or gases.
n
The units must be inspected by a service tech-
nician at least once annually. Visual inspec-
tions and cleaning may be performed by the
operator when the units are disconnected from
the mains.
1.7 Safety notes for installation,
maintenance and inspection
n
Appropriate hazard prevention measures must
be taken to prevent risks to people when per-
forming installation, repair, maintenance or
cleaning work on the units.
n
The setup, connection and operation of the
units and its components must be undertaken
in accordance with the usage and operating
conditions stipulated in this manual and comply
with all applicable regional regulations.
n
Local regulations and laws such as Water
Ecology Act must be observed.
n
The power supply should be adapted to the
requirements of the units.
n
Units may only be mounted at the points pro-
vided for this purpose at the factory. The units
may only be secured or mounted on stable
structures, walls or floors.
n
Mobile units must be set up securely on suit-
able surfaces and in an upright position. Sta-
tionary units must be permanently installed for
operation.
n
The units and components should not be oper-
ated in areas where there is a heightened risk
of damage. Observe the minimum clearances.
n
The units and components must be kept at an
adequate distance from flammable, explosive,
combustible, abrasive and dirty areas or
atmospheres.
n
Safety devices must not be altered or
bypassed.
1.8 Unauthorised modification
and changes
Modifications or changes to units and components
are not permitted and may cause malfunctions.
Safety devices may not be modified or bypassed.
Original replacement parts and accessories
authorised by the manufactured ensure safety. The
use of other parts may invalidate liability for
resulting consequences.
1.9 Intended use
The units are designed depending on the model
and equipment exclusively as a control unit for the
heat pump and the heating system.
Any different or additional use shall be classed as
non-intended use. The manufacturer/supplier
assumes no liability for damages arising from such
use. The user bears the sole risk in such cases.
Intended use also includes working in accordance
with the operating and installation instructions and
complying with the maintenance requirements.
Under no circumstances should the threshold
values specified in the technical data be exceeded.
1.10 Warranty
For warranty claims to be considered, it is essential
that the ordering party or its representative com-
plete and return the "certificate of warranty" to
REMKO GmbH & Co. KG at the time when the
units are purchased and commissioned.
The warranty conditions are detailed in the "Gen-
eral business and delivery conditions". Further-
more, only the parties to a contract can conclude
special agreements beyond these conditions. In
this case, contact your contractual partner in the
first instance.
5