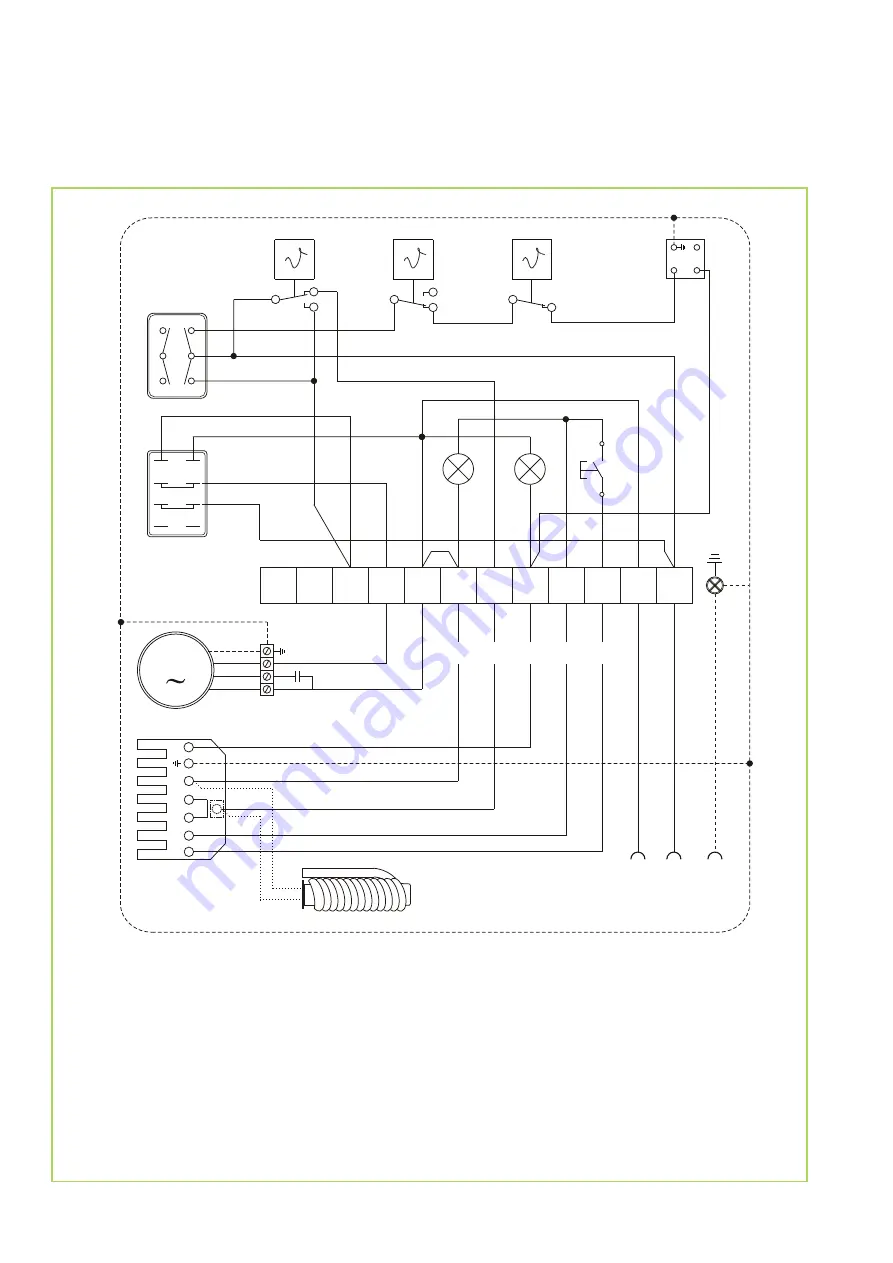
18
REMKO HTL 80/170
Electrical wiring diagram HTL 80
We reserve the right to modify the dimensions and design as part of the ongoing technical development process.
TW
RT
TR
STB
S1
WS
1A
2A
3A
4B
5B
6B
H2
H1
KL
1
2
3
4
5
6
7
8
9
L1
N
T1
T2
S
3
B
4
I
II
10
11
12
2
1
3
S2
M
HR
N
blau
schwarz
1
1
1
2
2
2
4
4
#2
#4
#3
#1
HW 07.13
N
PE
L1
N
230 V / 50 Hz
C
#5
ÖV
Option (EDV-Nr.: 1071411)
A
B
11
14
31
34
12
32
Legend:
C = Capacitor
H1 = Operating lamp (green)
H2 = External burner fault lamp (red)
HR = Auxiliary relay
KL = Terminal block
M = B3 Fan motor
ÖV = Multiflex oil pre-heating (option)
RT = Thermostat receptacle
S1 = Operating switch
S2 = Reset button - burner relay
STB = Safety temperature limiter
TR = Temperature controller
TW = Temperature monitoring device
WS = Burner connector, 7-pole
(only fitted with factory burner delivery)