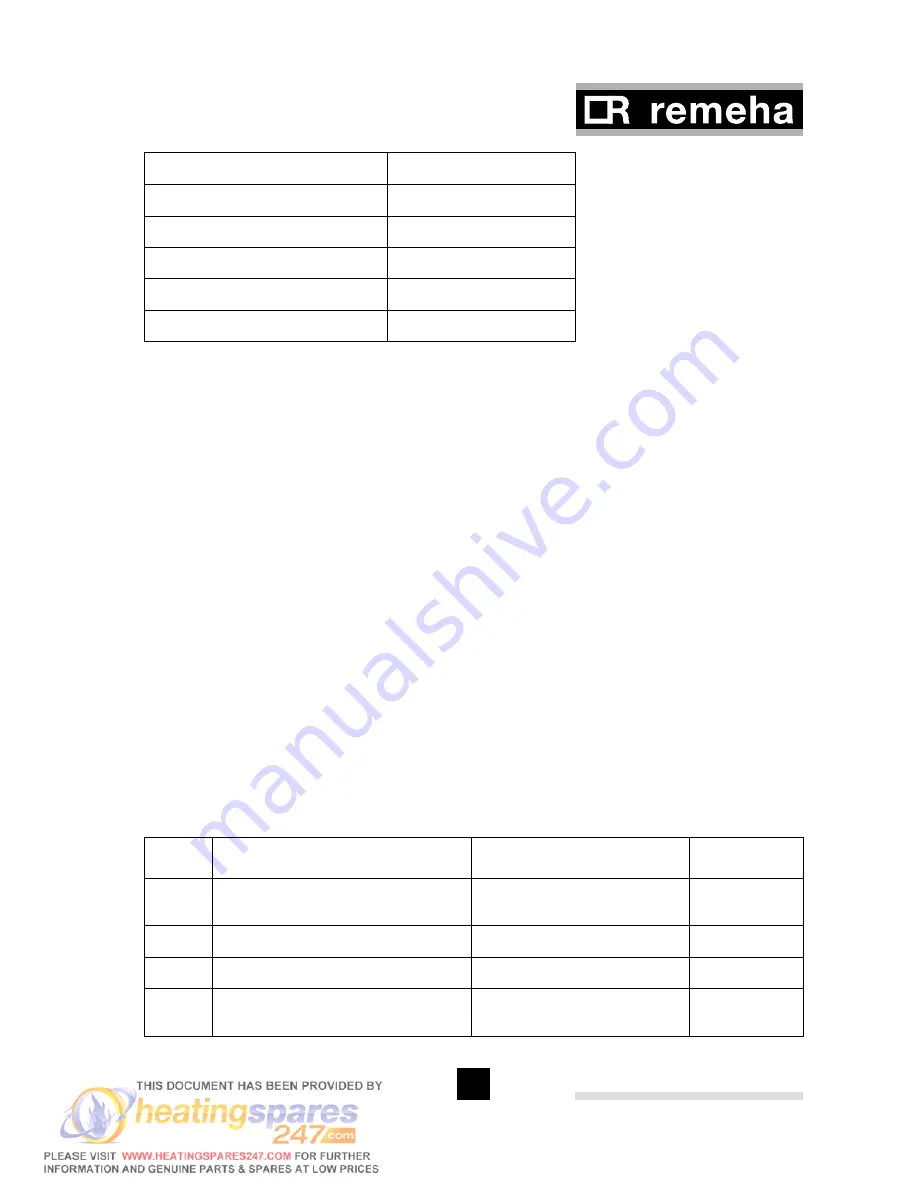
23
t
-display
Description
Second segment
[y
Operation mode
0
HTG and DHW off
1
HTG and DHW on
2
HTG on and DHW off
3
HTG off and DHW on
Table 08 Boiler control option
* NOTE:
Booster function n/a in UK
6.6 Setting mode service level (
X00
)
(only for the qualified service engineer)
To prevent accidental, unauthorised access by non-qualified persons the control
system requires an input code to gain access to the second level of boiler control.
- Press the ‘
m
’ - and ‘
s
’-keys simultaneously and hold. The
‘code’
-display now
shows a letter
c
with a random number in the
t
-display.
- While holding both keys pressed, set the
t
-display to
12
, using the [
+
] or [
-
]-
keys and press the ‘
e
’-key.
- The display will flash twice confirming acceptance of the access code.
- Release the keys and
c12
will dissappear from the display. You are now in the
service mode.
WARNING:
changing factory defaults without reference to the tables contained in this
manual may result in incorrect operation.
- To delete the service code press the ‘
reset’
-key once.
- If no keys are pressed over a 15 minute period the service code will delete
automatically.
Code
Description
Setting range
Preset
$
Flow temperature set point
during forced part load
20
-
90
ºC
79
%
High limit temperature set point
90
–
!0
(= 110°C)
)0
(=100)*
^
Fan speed at full load (HTG)
10
–
70
hundreds
62
&
Fan speed at part load (HTG
and DHW)
10
–
60
hundreds
12