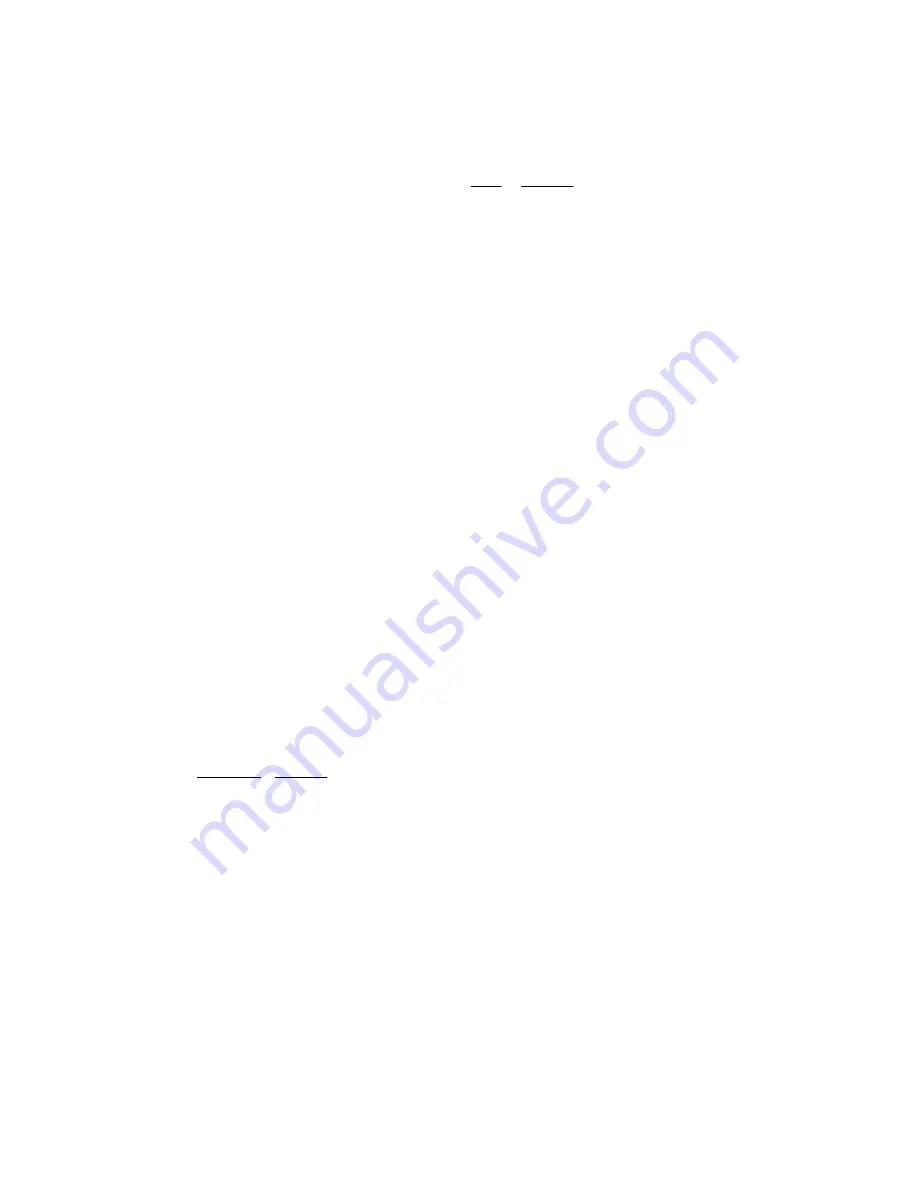
4:15
9.
Turn the OS pot slowly CW
until the trip point is slightly
greater than the maximum
application motor speed. Use
Figure 4-5C to determine the
equivalent voltage reading of
the overspeed trip point.
10. Start the controller.
11. With no input pulse reference,
verify that the motor is not
rotating and that no IETs exist.
12. Add a pulse reference at a low
frequency. Note the motor’s
rotation. If motor shaft rotation
is incorrect:
•
Give the controller a Stop
command.
•
Turn power OFF.
•
After verifying D-C bus
voltage is zero and the
POWER LED is not
illuminated, change the
position of switch 2SW-6 on
the hinged panel.
•
Turn power ON.
•
Give the controller a Start
command.
13. Give the controller a Stop
command.
14. Determine the maximum pulse
frequency required for the
application, using the following
formula:
Max
Pulse
Freq
(Hz)
Encoder
(PPR)
Max Motor
Speed (RPM)
60
4
Gear Ratio
X
X
=
Note:
Gear ratio is an integer
scaling constant set with an
Operator’s Terminal. The default
value is 4; the integer range is 1
through 10.
Example: If a 2000 RPM base
speed motor with a 2500 PPR
encoder is to operate at base
speed,
Max
Pulse
Freq
(Hz)
2500
2000
4
Gear Ratio
X
X
=
(PPR)
RPM
60
= 83.3KHz
83.3 KHz input corresponds to
2000 RPM on this motor/encoder
combination.
15. Give the controller a Start
command.
16. With the reference pulse
frequency at 0 Hz, quickly
increase the reference to
maximum. The motor will
accelerate to the maximum
speed. Note that, if the
reference frequency is
changed too quickly, the
controller will IET and the POS
LED will illuminate. If the
acceleration time is too long,
turn the PG pot 1/8 turn CW
and accelerate the motor
again. Repeat the motor
acceleration process until the
desired time is achieved.
Note:
The shortest acceleration
time is limited by current limit.
When the PG pot no longer has
any effect, the acceleration rate is
at its maximum for the application.
17. Give the controller a Stop
command.
18. Turn power OFF.
19. After verifying the D-C bus
voltage is zero and the
POWER LED is not
illuminated, remove the
voltmeters and any other
instrumentation connected
during startup.
20. Close and secure the
controller enclosure door, if
applicable.
Note
:
In position control, while the
motor is rotating, a position error
exists depending on its speed and
position loop gain. In the event
where the rotation is 2000 RPM,
number of pulses is 2500 PPR,
and the position loop gain is the
minimum, the position error will be
about 2.7 revolutions.
Artisan Technology Group - Quality Instrumentation ... Guaranteed | (888) 88-SOURCE | www.artisantg.com