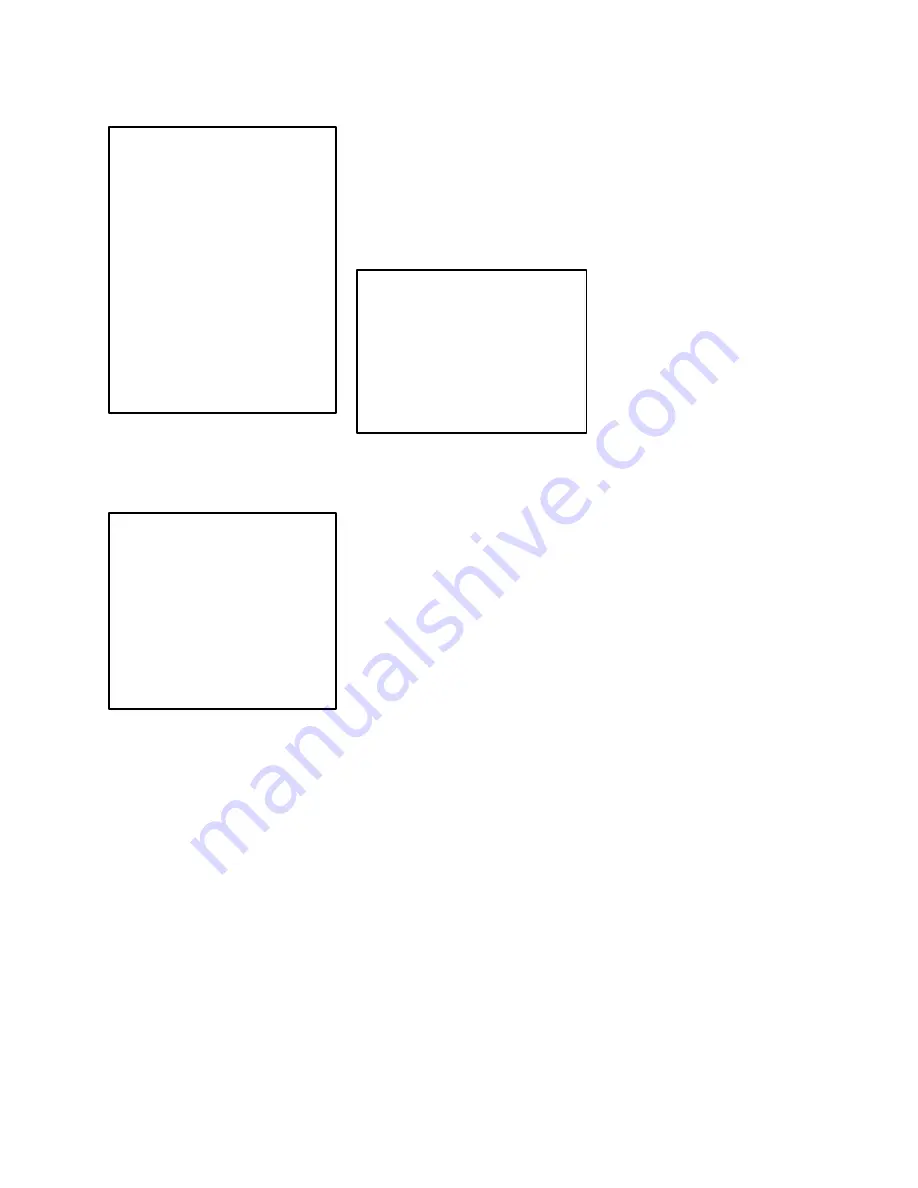
4:9
7.
Wire the controller for Speed
reference using Figure 3-12.
WARNING
VERIFY THE START CON-
TACTS ARE OPEN AND A
START SIGNAL IS NOT
PRESENT BEFORE APPLY-
ING POWER. ELECTRICAL
NOISE, IMPROPER WIRING,
OR MALFUNCTIONING
COMPONENTS COULD
CAUSE THE MOTOR TO RO-
TATE WHILE THE CONTROL-
LER IS SET AT ZERO SPEED.
FAILURE TO OBSERVE THIS
PRECAUTION COULD RE-
SULT IN BODILY INJURY.
8.
Verify that the Start contacts
are open, a Start signal is not
present, and the Speed
reference input is 0 volts.
DANGER
THE REMAINING STEPS
ARE MADE WITH POWER
ON. EXERCISE EXTREME
CARE BECAUSE HAZARD-
OUS VOLTAGE EXISTS.
FAILURE TO OBSERVE THIS
PRECAUTION COULD RE-
SULT IN SEVERE BODILY
INJURY OR LOSS OF LIFE.
9.
Turn power ON.
Note:
The POWER ON, the RDY,
and the SZ LEDs should
illuminate.
10. Check blower rotation. Air flow
should be in the direction of
the main motor. If it is not,
interchange the power leads
to studs 2 and 4. (Refer to
Figure 3-11a.)
11. Give the controller a Start
command. The RUN LED
should illuminate.
12. Make sure the drive shutdown
interlocks, such as safety
switches installed around the
driven machine, are
operational. When activated,
they must shut down the drive.
Note:
The following regulator DIP
switch controlled functions are not
enabled while the controller is
running: PG, OL, INC, and DIR.
These functions must be initialized
to be operative. To initialize, stop
the controller, remove all input
power, make the desired regulator
switch setting(s), and re-apply
power.
CAUTION
Make sure electrical commons
are not intermixed when moni-
toring voltage and current
points in the controller. Failure
to observe this precaution
could result in damage to, or
destruction of, the equipment.
13. Check motor shaft rotation. If
the motor is not rotating,
slowly increase the Speed
reference until the motor
rotates. If shaft rotation is
correct, proceed to Step 14. If
shaft rotation is incorrect:
•
Give the controller a Stop
command. Wait until the
motor has completely
stopped.
•
Turn power OFF.
•
After verifying the D-C bus
voltage is zero (using a
voltmeter connected to
faceplate terminals 147 (+)
and 145 (–)) and the
POWER LED is not
illuminated, change the
position of switch 2SW-6 on
the hinged panel.
•
Turn power ON.
•
Give the controller a Start
command.
14. Place a digital voltmeter (20
VDC scale) on 2CN pin
connectors 8(+) and 23(COM).
Note:
This analog D-C signal is
proportional to speed.
15. Increase the Speed reference
input until the voltmeter reads
4.8 VDC. This corresponds to
a motor speed of 1750 RPM
when using a 2500 PPR
encoder.
16. If the meter does not read 4.8
VDC or a different maximum
speed is required, adjust the
SR pot until the proper speed
is reached. The SR test point
will read 8.0 VDC at 2000
RPM speed.
If a
faster maximum speed
is
required:
•
Turn the SR pot CW until the
proper maximum speed is
reached. If the controller
IETs and the SFB LED
illuminates, the over-speed
trip point has been
exceeded.
•
Turn the OS pot 1/8 turn
CW.
•
Push the Reset pushbutton
(4SW).
•
The POWER ON, the RDY,
and the SZ LEDs should
illuminate.
•
Repeat this Step until the
desired speed is reached.
If a
slower maximum speed
is required:
•
Turn the SR pot CCW until
the proper maximum speed
is reached.
•
Turn the OS pot CCW until
the controller IETs and the
SFB LED illuminates.
•
Turn the OS pot 1/8 turn
CW.
•
Push the Reset pushbutton
(4SW).
17. Decrease the Speed
reference to zero volts.
18. Give the controller a Stop
command.
19. Turn power OFF.
20. Proceed to “Perform Startup
Procedure 2 with Motor
Coupled”.
Artisan Technology Group - Quality Instrumentation ... Guaranteed | (888) 88-SOURCE | www.artisantg.com