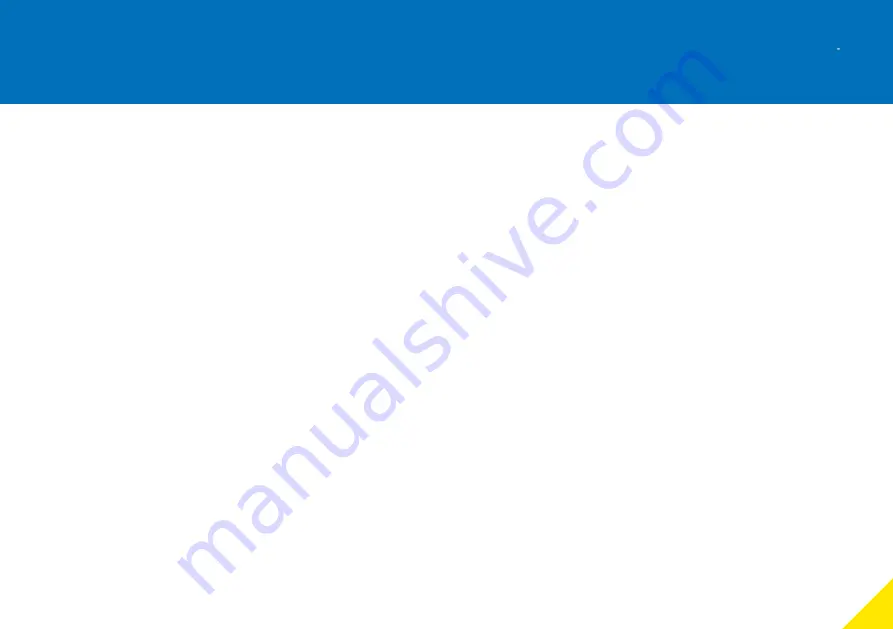
13
T
DAVIT
Spark Formation
There is an increased danger of ignition when
certain material pairings clash, namely non-
corrosion-resistant steel or cast iron against
aluminium, magnesium or pertinent alloys. This
applies especially in the case of rust or surface
rust. When assembling the product and inserting
fastening components, these must therefore be
clear of rust and debris of any kind. As stated
previously, care must be taken to ensure the
product is handled in a suitable manner, never
thrown down and always placed carefully onto
the ground.
REID recommends the use of corrosion resistant
tools when assembling this product to prevent
the possibility of any sparks.
Static Electricity
For Zone 1 and 2 applications, there is a potential
risk of static electricity build-up leading to an
incentive spark. Although the risk of such ignition
is unlikely, the system must be earthed during
assembly and use. The sockets should be in
direct contact with the ground and there should
be no membrane separating the socket from the
ground. If the route to earth for the structure
cannot be guaranteed, then an earthing cable
should be used.
Inspection, Maintenance & Repair
Special attention should be given to dust
deposits on the structure, especially in areas
where the profiles come into contact, and should
be wiped clean and care taken not to apply
materials that could create electrostatic charging.
Additionally, the kingpin should be checked to
ensure it rotates freely and the lower bearing
must be ensured to be fixed to the structure with
no possibility of a build-up of debris between
the contact surfaces.
The structure is predominantly constructed from
aluminum which will not rust. However, there are
steel components used throughout. These are
the fasteners, shackles and sockets. Where there
is sign of any rust deposits on the aluminium
structure, it should be wiped clean as above and,
where there is sign of rust on a steel component,
that component should be removed from use
and the structure not used until a replacement
is fitted.
If using the product in explosive atmospheres,
in addition to the Regular Inspection and
Maintenance information above, these additional
instructions should be followed:
Inspections must be instigated by the user prior
to each use if used in a potentially explosive
atmosphere.
Inspections and maintenance must be carried
out at a safe distance away from an explosive
atmosphere.
Summary of Contents for T DAVIT
Page 1: ...US REIDLIFTING COM Assembly Operation Guide TDAVIT...
Page 17: ...17 TDAVIT Variants Options Type VW...
Page 21: ...21 TDAVIT Variants Options Type T...
Page 25: ...Release trolley brake Use the hand chain to move the trolley along the beam 25 TDAVIT 12 13...
Page 26: ...Variants Options...