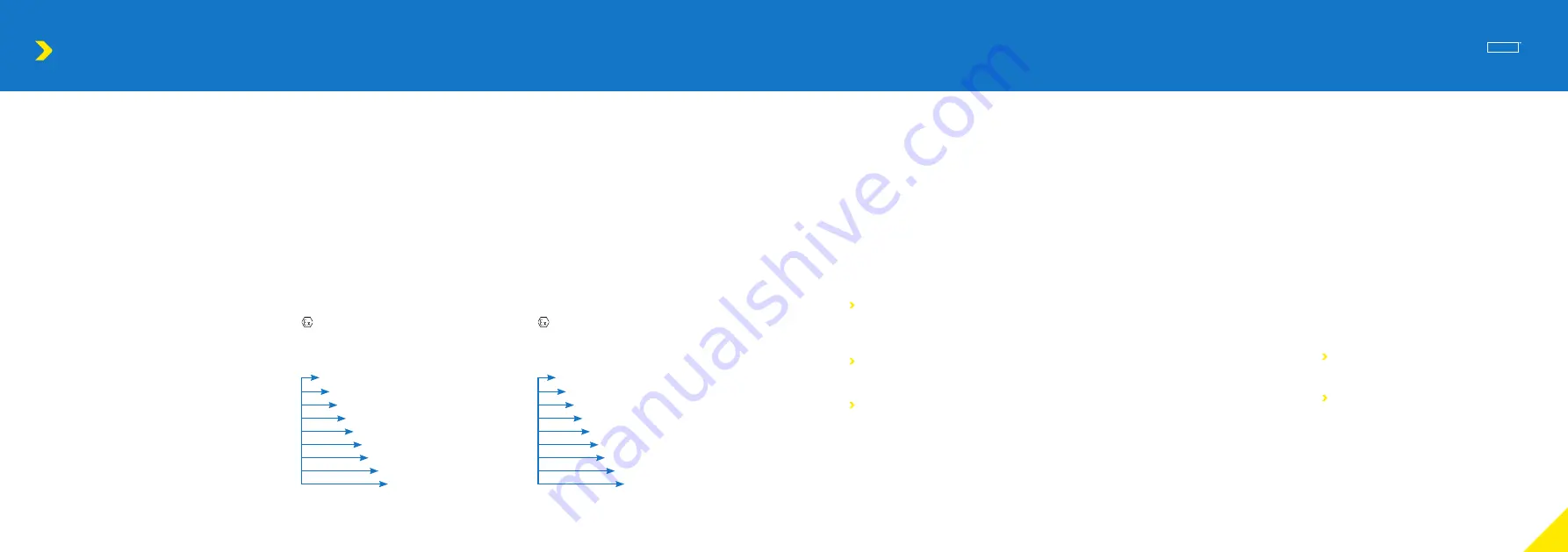
13
PORTA
GANTRY
500-3000
ATEX
This product has been designed for use in
explosive atmospheres in line with the following
requirements and information. Any use which
differs or exceeds this is considered incorrect
and REID Lifting Ltd will not accept any
responsibility or liability for damages resulting
from false application. The risk is solely with the
user. If the product has been customised in
any way, then it may not comply with standards
and no longer be suitable for use in explosive
atmospheres. If this is the case, then the product
will not have any of the markings below. If in
doubt, please contact your REID representative.
Classification [Zone 2]
As standard, the product meets the requirements
of Category 3 equipment for use in Zone 2
explosive atmospheres, providing a normal level
of protection where mixtures of air and gases,
vapours or mists or by air and dusts mixtures are
unlikely to occur or, if they do occur, are likely
to do so only infrequently and for a short period
only.
The product will have the following identification
on the serial label:
Classification [Zone 1]
Available as an upgrade, the product can
be supplied to meet the requirements of
Category 2 equipment for use in Zone 1
explosive atmospheres, providing a high level
of protection where mixtures of air and gases,
vapours, mists or by air and dusts mixtures are
likely to occur.
The product will have the following identification
on the serial label:
ATEX
Spark Formation
There is an increased danger of ignition when
certain material pairings clash, namely non-
corrosion-resistant steel or cast iron against
aluminium, magnesium or pertinent alloys. This
applies especially in the case of rust or surface
rust. When assembling the product and inserting
fastening components, these must therefore be
clear of rust and debris of any kind. As stated
previously, care must be taken to ensure the
gantry is handled in a suitable manner, never
thrown down and always placed carefully onto
the ground.
For Zone 1 and 2 applications, the height of
the sytem should not be adjusted using the
ratchet mechanism and/or geared wheel
within those zones
REID recommends the use of corrosion
resistant tools when assembling this system to
prevent the possibility of any sparks.
For ATEX Zone 1 use, stainless steel castor
brackets are fitted to reduce the possibility of
a spark.
Static Electricity
For Zone 2 applications, there is a potential
risk of static electricity build-up leading to
an incentive spark. Although the risk of such
ignition is unlikely, the system must be earthed
during assembly and use. This can be achieved
by attaching an earthing lead to a convenient
location on metallic parts of both the system and
trolley.
For additional protection in Zone 1 applications,
the system is fitted with anti-static trolley rollers,
stainless steel fasteners and therefore does not
need to be earthed.
However, the effectiveness of the conductivity
during operation can be affected by a dirty tread
or other environmental influences and therefore
must be checked periodically by the operator.
Inspection, Maintenance & Repair
Special attention should be given to dust
deposits on the structure, especially in areas
where the profiles come into contact, and should
be wiped clean and care taken not to apply
materials that could create electrostatic charging.
Additionally, the bearings in the trolley rollers
and castors should be checked to ensure they
rotate freely.
The structure is predominantly constructed from
aluminium which will not rust. However, there
are steel components used throughout. These
are; fasteners, castors, master-link, trolley rollers,
A-frame height adjustment gearing system (if
fitted) and the height adjustment ratchet (if
fitted).
Where there is sign of any rust deposits on the
aluminum structure, it should be wiped clean
as above and, where there is sign of rust on a
steel component, that component should be
removed from use and the structure not used
until a replacement is fitted.
If using the product in explosive atmospheres,
in addition to the Regular Inspection and
Maintenance information above, these additional
instructions should be followed:
Inspections must be instigated by the user
prior to each use if used in a potentially
explosive atmosphere.
Inspections and maintenance must be carried
out at a safe distance away from an explosive
atmosphere.
As Standard for Zone 2 Environments:
II 3 GD
Ex h IIC T6 Gc
Ex h IIIC T85°C Dc
Tamb -20°C to +55°C
As an upgrade for use in Zone 1 environments:
II 2 GD
Ex h IIC T6 Gb
Ex h IIIC T85°C Db
Tamb -20°C to +55°C
II – Equipment Group
2/3 – Atex Category
GD – Gas & dust
h- non- electrical protection concept
IIC / IIIC – IEC equipment group
T6 / T85°C – temperature classification
Gc /Gb – equipment protection level (gas)
Dc/Db – equipment protection level (dust)
Tamb – ambient temperature range
II – Equipment Group
2/3 – Atex Category
GD – Gas & dust
h- non- electrical protection concept
IIC / IIIC – IEC equipment group
T6 / T85°C – temperature classification
Gc /Gb – equipment protection level (gas)
Dc/Db – equipment protection level (dust)
Tamb – ambient temperature range