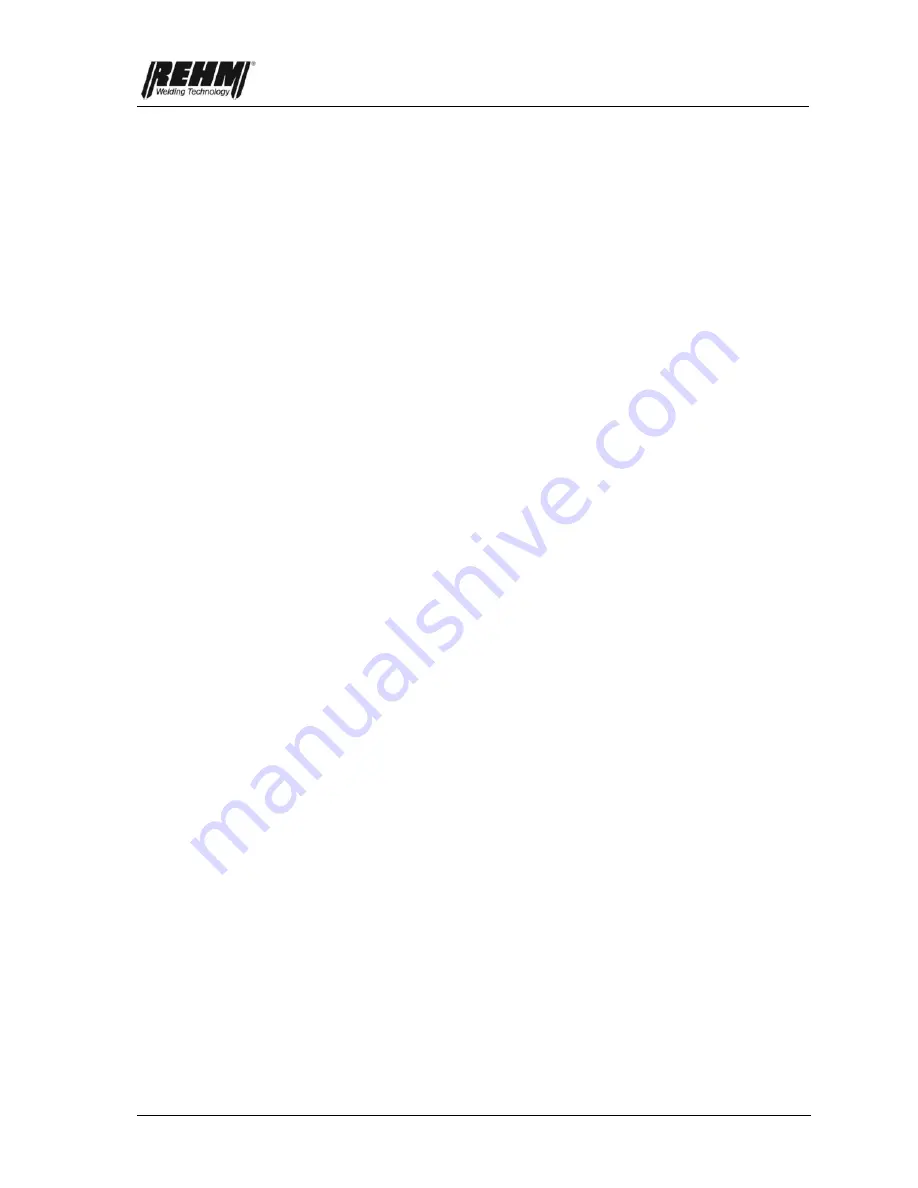
Operation
66
6.8
Practical notes
The practical user tips below represent just an overview of the wide range of
applications of REHM TIG welding units. For questions regarding specific
welding tasks, materials, inert gases or welding equipment, see the professional
literature or manufacturer recommendations.
When TIG welding you differentiate between materials, those that are welded
under direct current, and those welded under alternating current. Direct current
materials are non-alloyed, alloyed, highly alloyed steels, as well as copper,
nickel, titanium and their alloys. Alternating current is generally used for
aluminium and the associated alloys.
Various tungsten electrodes are offered and used for TIG welding. The
differences lie in the proportion and type of doping elements in tungsten
electrodes. The compositions are set out in DIN EN ISO 6848 (formerly EN
26848) and are generally made up of thorium oxide, ceroxide, zircon oxide or
lanthan oxide. The advantages of tungsten electrodes containing oxides are:
•
better ignition characteristics
•
more stable arc
•
greater current resilience
•
longer stand time
REHM supplies their torches with tungsten electrode WC 20 (grey) as standard.
The most frequently used electrode diameters and their resilience can be found
in the relevant technical literature. Remember that the values specified there are
calculated with machines that do not have the balance range of the REHM TIG
units. The guideline is that the current is too high for a given electrode if it drips
or has a broom-like structure. You can choose between lower current or, when
using alternating current, using a larger minus proportion in the balance setting.
When welding with direct current, the electrode is pointed.
The REHM TIG welding units can also use pointed electrodes for alternating
currents welding with the balance settings in the minus region. This has the
advantage that the arc is even more concentrated and effective. This also usually
increases the welding speed.
Remember when grinding the electrode, the grind direction should be along the
length of the electrode. To avoid risks, only use grinding units and extraction
systems suitable for the purpose.
Argon is usually used as inert gas for TIG welding. For some applications,
helium, argon/helium mixes, or argon/hydrogen mixes may also be used. With
the increase in helium, the arc ignition is more difficult and the application of heat
higher. The amount of inert gas required will depend on the electrode diameter,
gas nozzle size, welding current level and the movement of air at the place of
work. With a work piece thickness of 4 mm using argon as inert gas, the first
guideline is, for example, aluminium requires approximately 8 litres a minutes
and steel and chrome-nickel-steel 6 litres a minute. When using helium, the
required amount is considerably higher.
The standard lengths of the TIG torches are 4 m and 8 m. But longer torches
may also be connected to these machines. Depending on the task and current
level, the appropriate tungsten electrode, split pin and gas nozzle must be
selected. When using torches with two buttons, the two current regulators can be
used during welding to switch the current between two preset values.
Weldable materials
Tungsten
electrodes
Inert gases
TIG torches
Summary of Contents for INVERTIG.PRO digital 240 DC, 240 AC/DC
Page 1: ...GB OPERATING INSTRUCTIONS TIG inert gas welding units INVERTIG PRO digital 240 450 DC AC DC...
Page 7: ...Introduction 7 1 2 General description Figure 1 INVERTIG PRO digital...
Page 75: ...Circuit diagrams 75 9 Circuit diagrams...
Page 76: ...Circuit diagrams 76...
Page 77: ...Circuit diagrams 77...
Page 78: ...Circuit diagrams 78...
Page 81: ...Components 81 Figure 53 Exploded view of an INVERTIG PRO digital 240 DC 450 AC DC left...
Page 82: ...Components 82 Figure 54 Exploded view of an INVERTIG PRO digital 240 DC 450 AC DC right...
Page 87: ......