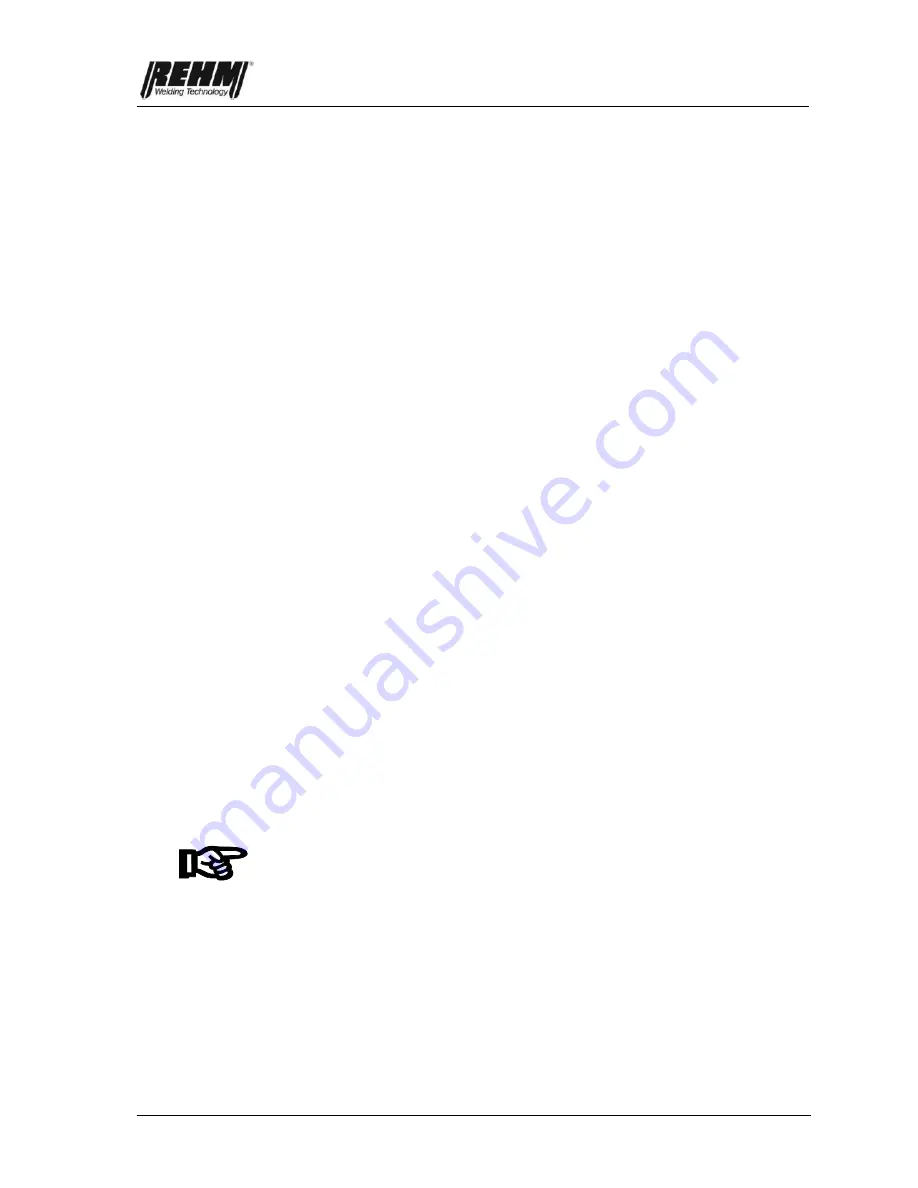
Putting into operation
62
5.4
Connecting the welding unit
Connect the REHM welding current source in accordance with the valid VDE
regulations to the power supply network and ensure that you meet all the
regulations stipulated by the appropriate professional associations.
When connecting the unit, pay attention to the specifications regarding the supply
voltage and network fuses. Safety mechanisms and fuses must always be set out
for the specified current. The required specifications can be found on the power
label of your unit.
Always switch the unit off when it is not in use.
Screw the cylinder pressure regulator onto the cylinder and check the seal of the
connection. Always close the bottle valve after completely work. Observe the
regulations of the appropriate professional associations.
5.5
Cooling the welding unit
Set the REHM welding unit up in such a way that the air inlets and outlets are not
affected. The duty cycle of the power components indicated can be reached only
with adequate ventilation (see "Technical data"). Ensure that no sanding dust,
dust or any other metal items or foreign objects are able to enter the unit.
5.6
Guidelines for working with welding power
sources
Welding tasks may only be carried out by specialists or trained personnel familiar
with the technology and procedures. When welding, wear protective clothing and
ensure that other people in the vicinity of the machine are not endangered. After
completing welding, leave the unit switched on for a few minutes so that the fan
runs a little longer and removes some of the residual heat from the unit.
5.7
Connecting welding cables or torches
The REHM TIG welding units are fitted with quick-fit socket systems for
connecting earth cables and TIG torches or electrode cables. The connection is
made by inserting and turning to the right. The inert gas hose is connected a via
quick connector to welding unit. The torch button socket is fitted into the socket
that is built in.
Important!
In order to prevent unnecessary losses of energy during welding ensure that all
of the connections of the welding cables are tightened and well insulated.
5.8
Connecting external components
External components are connected via the standard 7-pin remote control socket
on the back of the INVERTIG.PRO
digital
. These include the Rehm accessories
that are described in chapter 4 (remote foot controller P1, water cooling devices
TIG-COOL 2000 and TIG-COOL CART 2000, automation interface). The
electrical connection is made via a serial CAN connection.
Summary of Contents for INVERTIG.PRO digital 240 DC, 240 AC/DC
Page 1: ...GB OPERATING INSTRUCTIONS TIG inert gas welding units INVERTIG PRO digital 240 450 DC AC DC...
Page 7: ...Introduction 7 1 2 General description Figure 1 INVERTIG PRO digital...
Page 75: ...Circuit diagrams 75 9 Circuit diagrams...
Page 76: ...Circuit diagrams 76...
Page 77: ...Circuit diagrams 77...
Page 78: ...Circuit diagrams 78...
Page 81: ...Components 81 Figure 53 Exploded view of an INVERTIG PRO digital 240 DC 450 AC DC left...
Page 82: ...Components 82 Figure 54 Exploded view of an INVERTIG PRO digital 240 DC 450 AC DC right...
Page 87: ......