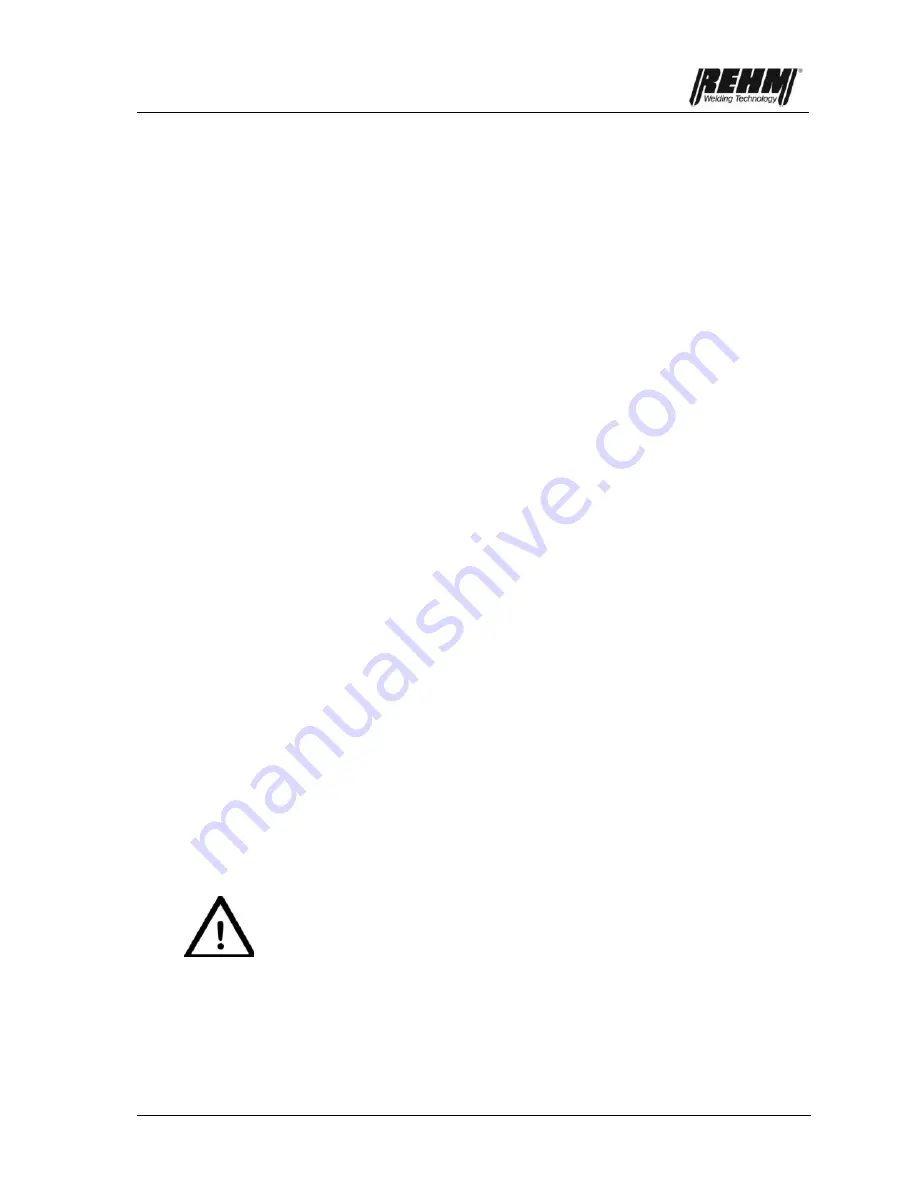
Operation
65
Inform people standing by of the dangers of the arc rays and the hot metal
sparks and protect them using a shield that is not flammable.
Pressurised gas bottles also present a potential danger. Strictly observe the
safety regulations of the relevant professional authorities and the suppliers.
Ensure that inert gas bottles are not able to fall. Never transport inert gas
bottles without their protective caps.
6.4
Fire prevention
Hot slag and sparks can cause fires if they come into contact with flammable
materials, liquids or gases. Remove all flammable materials from the welding
area and ensure a fire extinguisher is on stand-by.
6.5
Ventilation
Work places must be set up, whilst taking account of procedures, materials and
conditions of use, in such a way that the air the user breathes is free from
unhealthy materials (see TRBS 2131 and BGR 500 chapter 2.26).
Ensure that the welding area is well ventilated either by natural means or by
technical ventilation systems.
Do not weld painted or solvent treated work pieces as these may give off
poisonous gases.
6.6
Checks before starting
The prerequisites that
the unit is set up correctly in accordance with
Chapter 5, Putting into
operation
all connections (inert gas, torch connection) have been made in accordance
with
Chapter 5, Putting into operation
the appropriate maintenance has been carried out in accordance with the
maintenance interval
Chapter 8
,
Maintenance
the safety mechanisms and the components of the unit (in particular the torch
connector hoses) are checked by the operator and are functional.
the operator and other persons involved have put on the appropriate
protective clothing, and the working area has been shielded so that no
bystanders are at risk.
6.7
Connecting the earth cable
Warning!
Chapter 6.2 Electrical risks. Make sure that the welding current is not
able to flow through chains of lifting machinery, crane lines or other
current carrying parts.
Chapter 6.2 Electrical risks. Make sure that the earth cable is connected
to the work piece as close as possible to the welding area. Earth
connections affixed to points further apart reduce the effectiveness and
increase the risk of electrical shocks and stray current.
Summary of Contents for INVERTIG.PRO digital 240 DC, 240 AC/DC
Page 1: ...GB OPERATING INSTRUCTIONS TIG inert gas welding units INVERTIG PRO digital 240 450 DC AC DC...
Page 7: ...Introduction 7 1 2 General description Figure 1 INVERTIG PRO digital...
Page 75: ...Circuit diagrams 75 9 Circuit diagrams...
Page 76: ...Circuit diagrams 76...
Page 77: ...Circuit diagrams 77...
Page 78: ...Circuit diagrams 78...
Page 81: ...Components 81 Figure 53 Exploded view of an INVERTIG PRO digital 240 DC 450 AC DC left...
Page 82: ...Components 82 Figure 54 Exploded view of an INVERTIG PRO digital 240 DC 450 AC DC right...
Page 87: ......