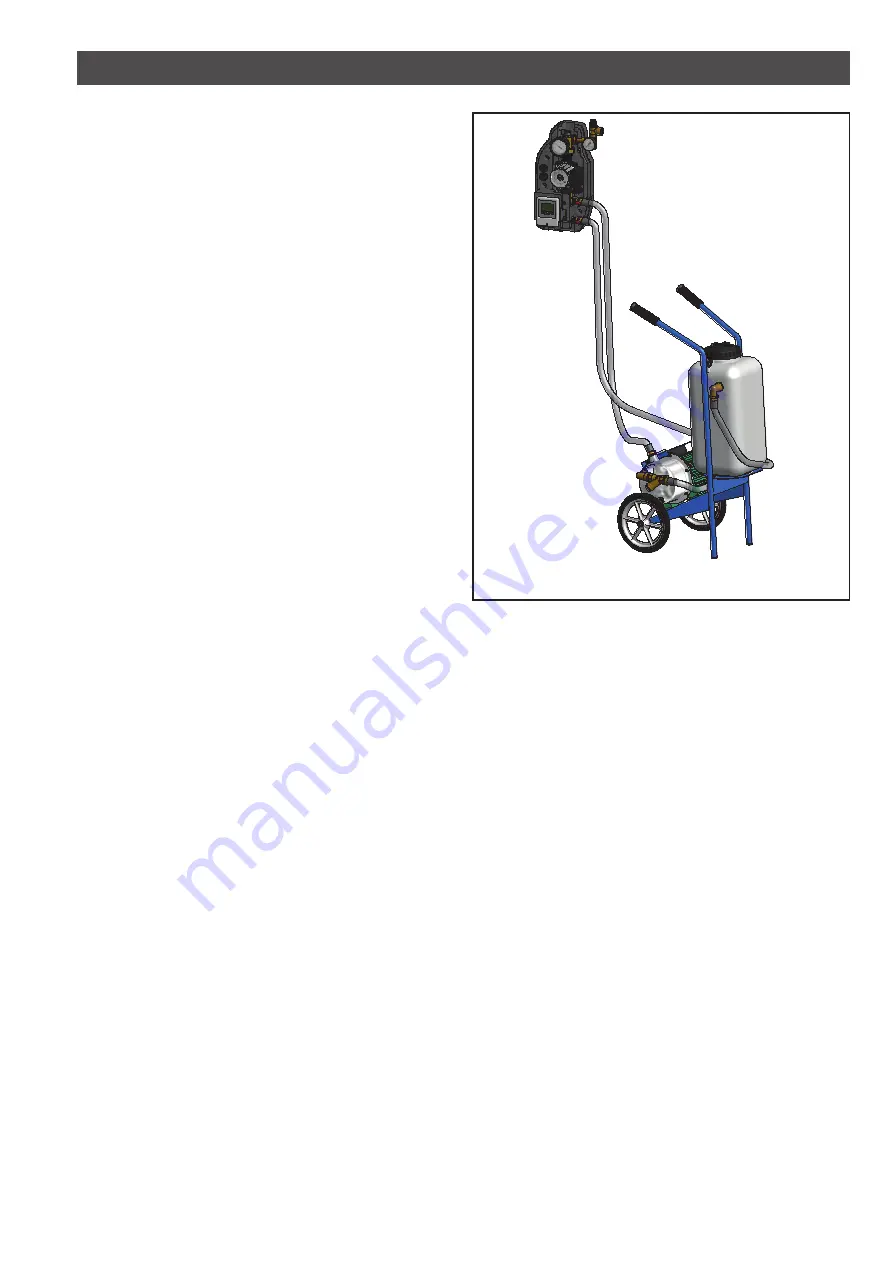
22
The below listed procedures are valid when a Regulus
pump station is used.
10.1 Filling
• in order to fill the system, use a filling device with a
reservoir for solar liquid and a filling pump (see Fig. 30)
• attach the filling hose to the feed valve and open the
valve completely
• please use antifreeze solar fluid Regulus - Solarten
super to fill the system
• attach the return hose to the bleed valve and open the
valve completely
• close the integrated ball valve in the flowmeter (the
groove in the flowmeter‘s adjusting screw must be
horizontal).
• open the check valve (valves - two for a twin-pipe
solar pump station) above the pump by turning the ball
valve by 45° (intermediate position between open and
closed)
• pour sufficient quantity of solar fluid into the reservoir
of the filling device, turn on the filling pump and fill the
solar thermal system.
10.2 Flushing
• flush the solar thermal system. for at least 15 minutes
using the filling device. In order to bleed air and possi-
ble impurities from the system perfectly, open shortly
the integrated ball valve of the flowmeter from time to
time (the groove vertically).
10.3 Air bleeding
• with the filling pump running, close the bleed valve and
increase the pressure up to about 5 bar
• close the feed valve and turn off the filling pump, open
the regulation screw on the flowmeter (groove horizon-
tally), do not disconnect the filling pump hoses!
• set the circulation pump(s) to the highest speed and
repeat switching on and off to air-bleed the system (an
air-free pump works almost noiselessly)
• watch the system pressure and when it starts falling,
increase it by turning on the filling pump and opening
the feed valve to 5 bar
• repeat air bleeding so long until the float in the
flowmeter‘s regulation valve takes a steady position
during pump operation and bubbles stop appearing in
the flowmeter. After that, let the circulation pump run
for at least 5 minutes.
• in case an automatic air vent/s is/are used anywhere
in the solar thermal system., close this valve after air
bleeding
10. SYSTEM FILLING, FLUSHING, LEAK TEST AND AIR BLEEDING
10.4 Leak test
• examine the whole system at 5 bar pressure (all con-
nections, solar collectors, valves etc.), no visible leaks
are allowed. Leave the system under pressure for at
least 2 hours, then examine the system once again
• consider the test result successful if no leaks appear
and/or no noticeable pressure drop appears in the
system
• set the working pressure by point 8.2 Calculation of
system working pressure
• set the pump to a suitable speed and set the flow by
the flowmeter and data in Tab. 1
• disconnect the hoses of the filling device and screw
caps on the feed and bleed valves
•
open entirely
the ball valve(s) above the pump
• after several days of operation, air-bleed the system
again.
Do not flush the system with water. Since it is impossible
to empty it completely, a risk of frost damage appears.
Fig. 30: Filling a solar system
Summary of Contents for KPG1H-ALC
Page 26: ...26 85 2150 1170 70 ø22 2193 21 5 15 CONNECTION DIMENSIONS ...
Page 28: ...28 ...
Page 30: ...30 ...
Page 31: ...31 ...