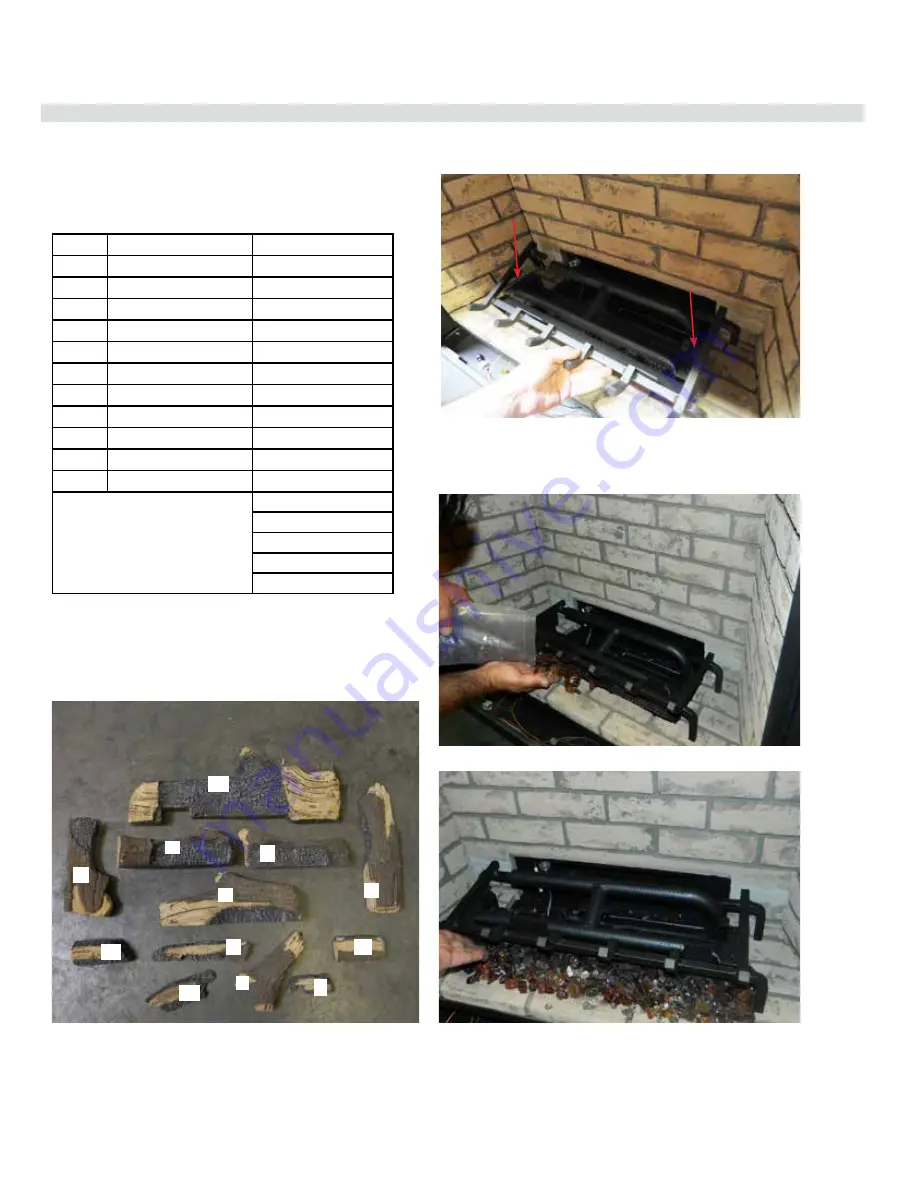
installation
Grandview
®
G800C-1 Gas Fireplace | 67
Log Set Installation
11.22.19
920-127a
LOG SET INSTALLATION
Page 1 of 4
1
Rear Log
2
Middle Left Log
3
Middle Right Log
4
Center Left Cross Log
5
Front Bottom 'Y' Log
6
Left Rear Log
7
Right Cross Log
8
Middle Front
9
Left Log Piece
10
Right Log Piece
11
Left Front Log Piece
12
Right Front Log Piece
Must also purchase (#761-938) Log
Grate and Ember package separate-
ly. The kit contains:
Log Grate
3/4" Ginger glass
Vermiculite
Black/White Embers
Log Support Plates
Read the instructions below carefully and refer to the diagrams.
If logs are broken do not use the unit until they are replaced.
Broken logs can interfere with the pilot operation.
The G800EC/G800C/G800C-1 log sets, #761-930 for Oak, #761-932
for Birch, contain the following pieces:
1
6
8
2
3
4
9
11
5
10
12
7
NOTE: Panels (brick, steel, or enamel) must be installed
prior to installing the log set.
1. Carefully remove the logs from the box and unwrap them. The logs
are fragile, handle with care -
do not force into position when
installing.
2. Install the log grate—secure with 2 screws in locations show below.
3. Install the supplied crystals over the ember lights underneath the
burner as shown. Place vermiculite and embers on top of the glass.
Do not place any media on the burner.
Diagram 1—Log ID
Diagram 2—Log Grate Install
Diagram 3—Install Glass
Diagram 4—Install Vermi Lava
G800EC/G800C/G800C-1