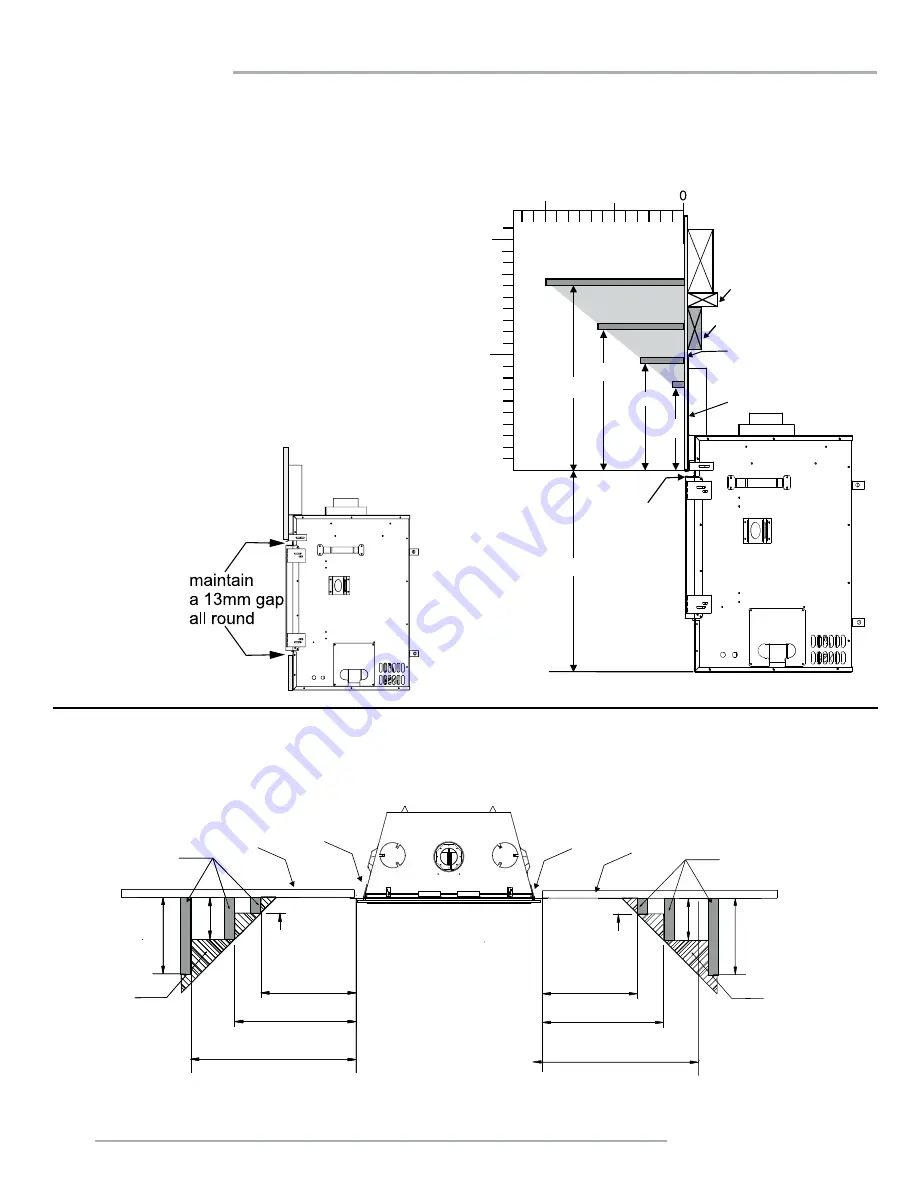
12
Regency GF950L Gas Fireplace
CLEARANCES FOR COMBUSTIBLE FINISHING WITH MANTEL
Due to the extreme heat this fireplace emits, the mantel clearances are critical.
Combustible finishing and mantel clearances are shown in the diagram
on the right. Finishing Trim must be used with combustible finishing.
Note: Maximum combustible finishing material thickness is 19mm
measured from the front of the fireplace opening. If total
finishing material is greater than 19mm, non-combustible
must be used.
Note:
Ensure the paint that is used on the mantel and the facing is
"high quality" or the paint may discolour.
COMBUSTIBLE MANTEL LEG CLEARANCES
Mantel leg & combustible finishing clearances as per diagram:
Combustible Material
(152mm)
(305mm)
0
To Unit
Base
(618mm)
(254mm)
Top of
Fireplace
Opening
(508mm)
(305mm)
(407mm)
(178mm)
Combustible
Stud
(On Edge)
Nailing Flange
Combustible facing
(min. 10mm- max. 19mm)
(234mm)
(200mm)
(100mm)
(309mm)
Allowable mantel
leg projection
181mm
254mm
330mm
38mm
MANTEL LEG
102mm
178mm
Allowable mantel
leg projection
181mm
254mm
330mm
38mm
MANTEL LEG
102mm
178mm
Allowable mantel
leg projection
181mm
254mm
330mm
38mm
MANTEL LEG
102mm
178mm
13mm Gap
13mm Gap
Combustible
Combustible
installation
IMPORTANT:
Summary of Contents for GF950L-LP
Page 60: ...60 Regency GF950L Gas Fireplace NOTES notes ...
Page 66: ...66 Regency GF950L Gas Fireplace ...
Page 68: ......
Page 69: ...Regency GF950L Gas Fireplace 69 NOTES notes ...
Page 70: ...70 Regency GF950L Gas Fireplace NOTES notes ...