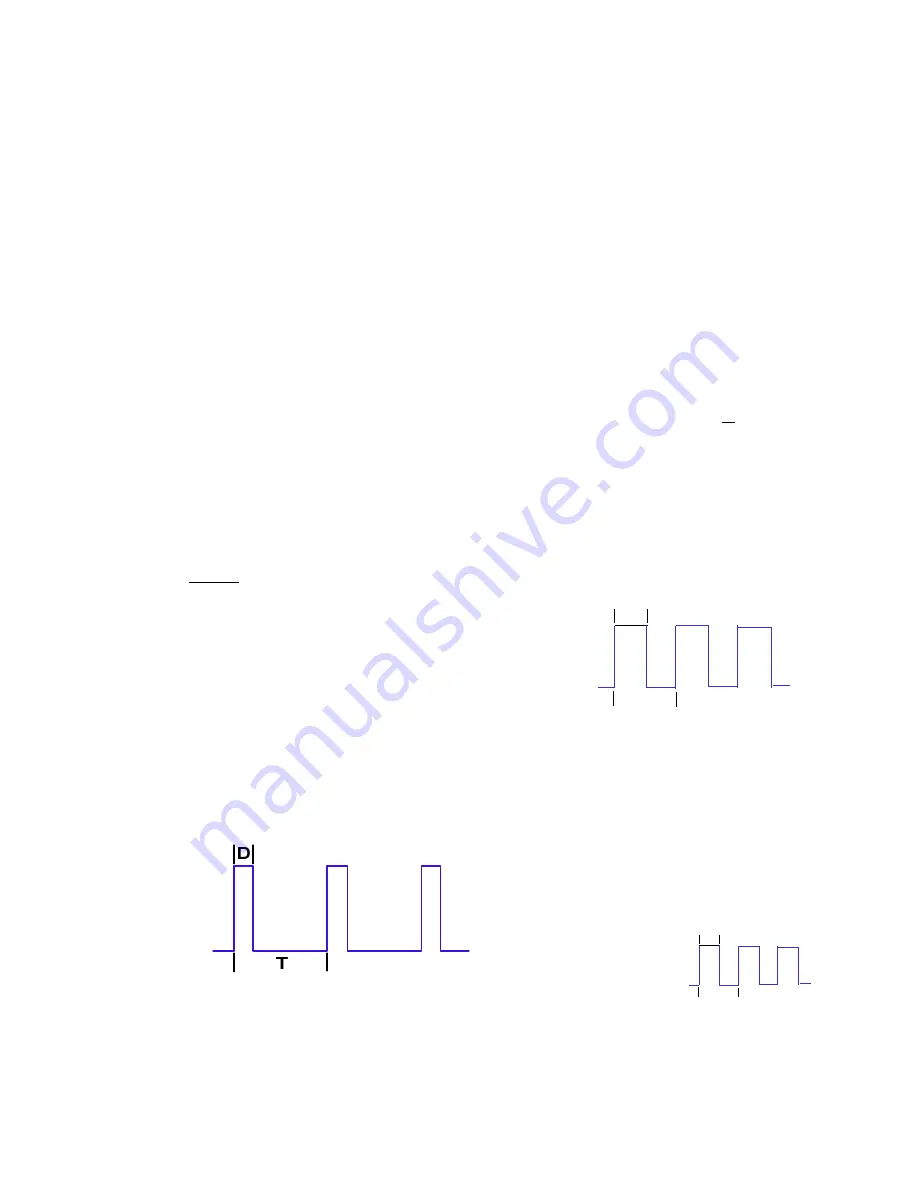
© 2006
GE ECM
by Regal-Beloit
- 36 -
Indoor Blower Motors
v0.2
If the manufacturer provides the information in their troubleshooting guides as to
what these dc voltages should be, the communication can be diagnosed with a dc
volt meter. Make sure the meter is set to dc volts and the polarity of the connections
is correct following the OEM guides.
The information provided below is strictly “nice to know” information. A
technician would not make the following checks to diagnose the motors
operation or output.
-
The motor does not look at the dc voltage on the PWM circuit. It is reading the
duty cycle as a representation of the desired motor output.
The following formula can be applied to the dc voltage readings to help
understand the % demand of the PWM signal (duty cycle)
For Example:
20 vdc is measure between terminals 3 and 15 (value T)
10 vdc is measure between terminals 3 and 10 (value D)
The percentage of demand (motor output or airflow) would be 50%.
10 (D) = .5 x 100 = 50%
20 (T)
The actual PWM signal would look like the example to
the right, where the signal is on for 50% of the cycle
and off for 50% of the cycle.
If the demand percentage was 20% the PWM signal
would be on for 20% of the cycle and off for 80% of
the cycle. This signal would like the example to the
below.
PWM (Duty Cycle)
D
T
Pin number
1
2
3
4
5
6
7
8
9
10
11
12
13
14
15
16
Connected to PWM common
NC*
Connected to PWM common
NC*
NC*
NC*
NC*
NC*
NC*
PWM signal
NC*
NC*
NC*
NC*
Start/Stop signal: 9 - 23VDC
NC*
* Not Connected
Pin number
1
2
3
4
5
6
7
8
9
10
11
12
13
14
15
16
Connected to PWM common
NC*
Connected to PWM common
NC*
NC*
NC*
NC*
NC*
NC*
PWM signal
NC*
NC*
NC*
NC*
Start/Stop signal: 9 - 23VDC
NC*
* Not Connected
PWM (Duty Cycle)
D
T
% Demand = x 100
(in torque or airflow)
D
T