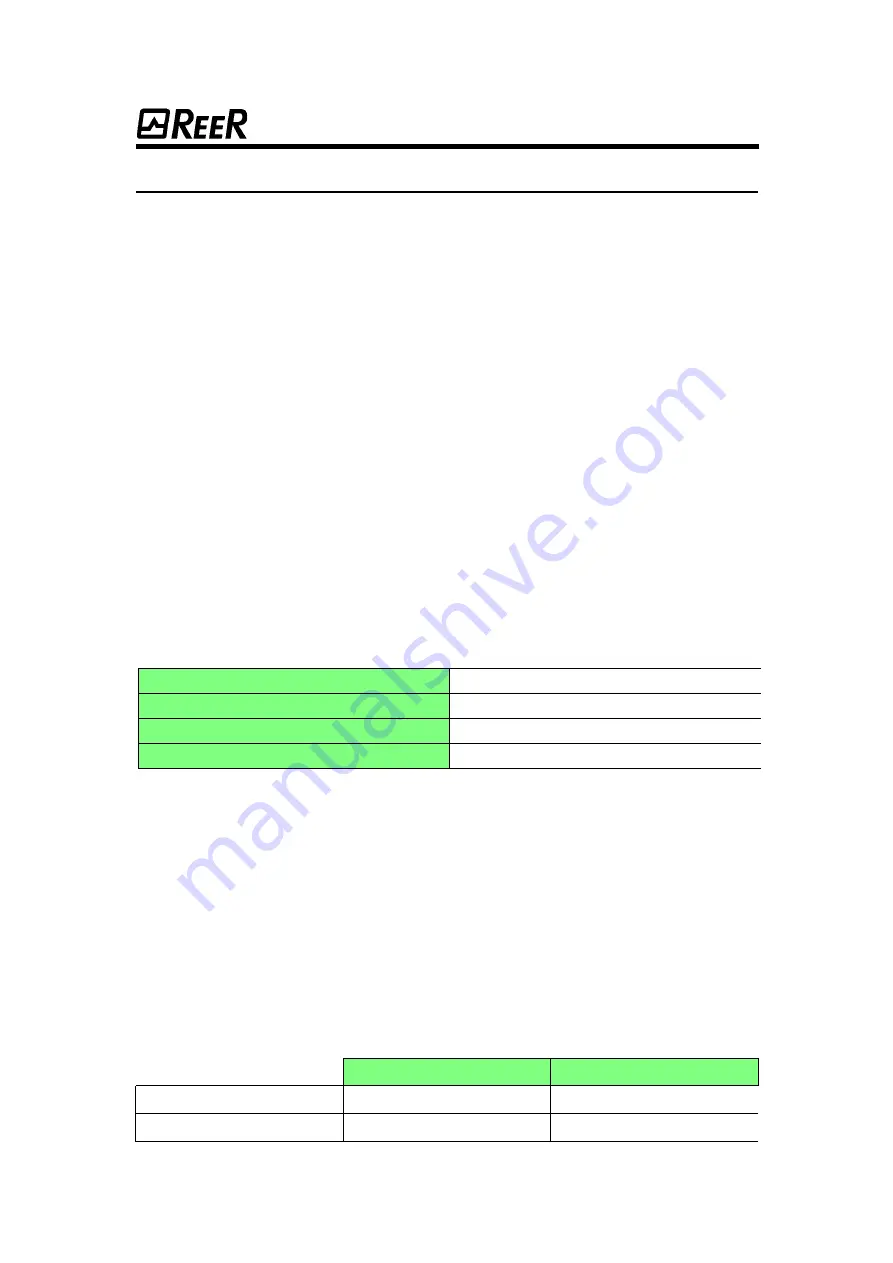
E L E CT R I CA L CON N E CT I ON
E L E CT R I CA L CON N E CT I ON
E L E CT R I CA L CON N E CT I ON
E L E CT R I CA L CON N E CT I ON
Wiring should be carried out according to wiring diagram shown on page
27. Before connecting the device, make sure your power supply features
correspond to the product specifications:
Emitter, receiver and control unit should be powered with
Emitter, receiver and control unit should be powered with
Emitter, receiver and control unit should be powered with
Emitter, receiver and control unit should be powered with
24V
24V
24V
24V
dc
±
20% (refer to power consumptions on page
20% (refer to power consumptions on page
20% (refer to power consumptions on page
20% (refer to power consumptions on page 11 and
11 and
11 and
11 and 12).
12).
12).
12).
No other devices shall be connected to the emitter and receiver connectors.
For a good reliability, the output capacitance of the power supply should
have at least a value of 2000
µ
F for ampere of current input (refer to power
consumptions on page 11).
Load features.
Load features.
Load features.
Load features.
The control unit AU S3 is equipped with two output relays A and B (with
guided contacts). Even if these relays are specified for higher coil voltages
and load currents, make sure that the load features comply with the
indications of the following table to guarantee a correct operation and
avoid damage or quick ageing of A and B internal relays.
For loads with higher switching characteristics use K1 and K2 additional
relays.
Use of additional relays K1 and K2.
Use of additional relays K1 and K2.
Use of additional relays K1 and K2.
Use of additional relays K1 and K2.
If additional relays K1 and K2 are used to increase the number of contacts
available on the AU S3 control unit or to increase the switching capacity of
its inner relays A and B, connection diagram B (page 27) must be used.
•
K1 and K2 must be safety relays with guided contacts.
•
Used K1 and K2 contacts as indicated in the following table.
•
The feedback control is set if K1-1(NO) and K2-1 (NC) are
connected in serial between terminal 5 and 6 on the control unit
(commutated signal: 20mA/24V
dc
).
!
Minimum switching voltage
15V
dc
Minimum switching current
20mA
Maximum switched voltage
125V
ac
Maximum switched current
2A
K1 relay
K2 relay
Feedback control
K1-1 normally open
K2-1 normally closed
Machine stopping circuitry
K1-2 normally closed
K2-2 normally open
25
25
25
25
Summary of Contents for ARGOLUX AS 1103
Page 2: ......