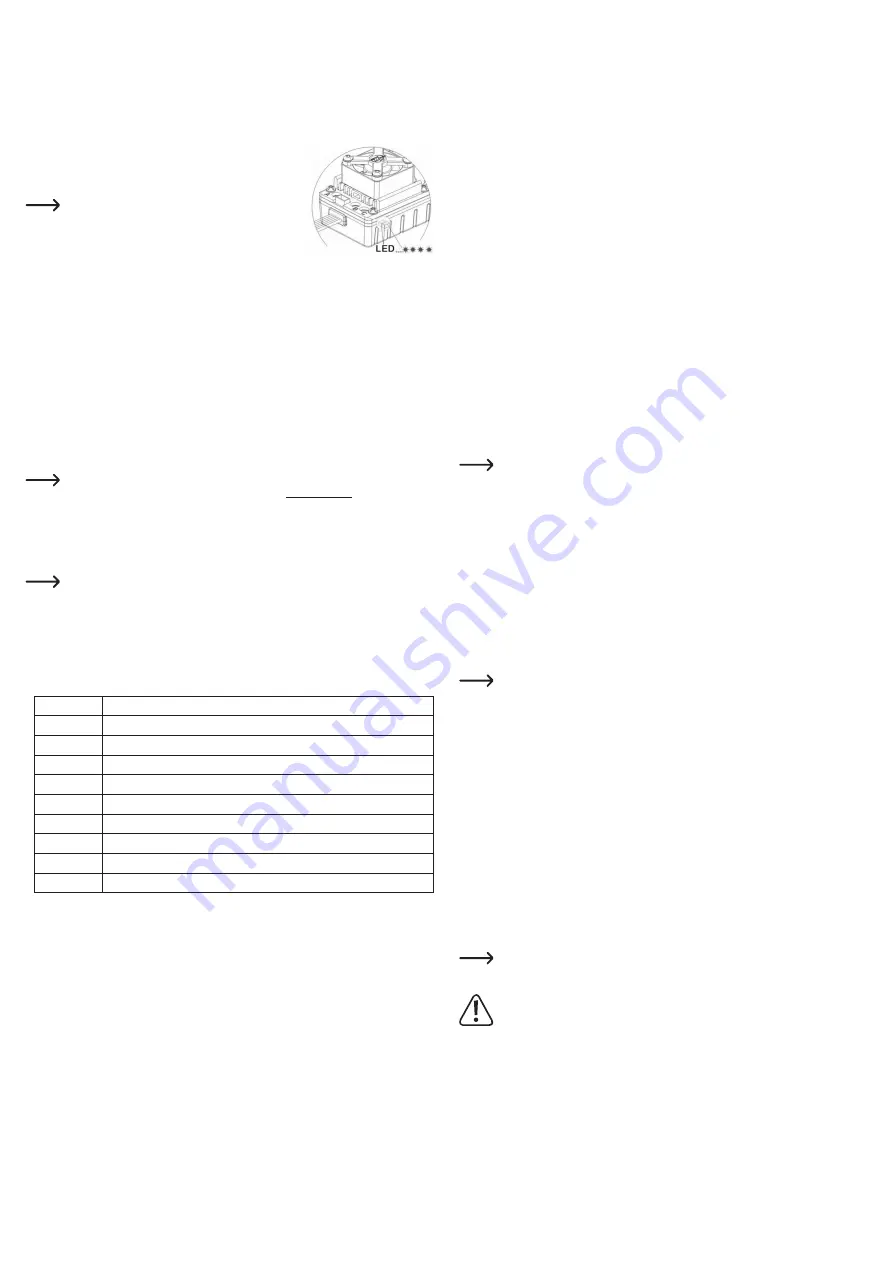
Programming
a) Programming of full throttle and idle position
To programme the full throttle position for forwards/backwards drives, and the idle position, proceed as
follows:
• Switch on the transmitter and leave the throttle/brake lever in idle position. Move the trim for drive func-
tion to the middle. Path limits and ABS must not be programmed, if computer transmitters are used. If the
programme does not work as desired, the control direction of the throttle lever must be set to reverse.
• Switch off the speed controller and then connect the drive battery.
• Keep the setup button pressed down and switch on the speed control-
ler. Release the setup button immediately when the LED (see image
on the right) in the speed controller starts flashing red and the motor
emits a sound signal.
The sound signal is caused by briefly activation of the brush-
less motor. However, depending on the motor it can be very
muted or you may not hear it. In this case, pay attention to the
LEDs on the speed controller.
• Now, press the programming button once with the throttle/brake lever in
idle. The LED on the speed controller briefly flashes green. The motor
emits a sound signal.
• Move the throttle/brake lever into full throttle position for forwards movement (pull the throttle/brake lever
all the way towards the handle) and hold it in this position. Now, press the programming button once.
The LED flashes twice in green. The motor emits two sound signals. The full throttle position for forward
driving is saved.
• Move the throttle/brake lever into full throttle position for backwards movement (pull the throttle/brake lever
all the way forwards away from the handle) and hold it in this position. Now, press the programming button
once. The LED flashes three times in green. The motor emits three sound signals. The full throttle position
for reverse driving is saved.
• Release the throttle/brake so that it sits in the idle position. Neither the red nor the green LED must now
be lit. The programme for the idle position is saved. Motor and speed controller are ready for operation
after approx. three seconds. If you switch on the speed controller again, it is now ready for operation with
the settings made above.
b) Programming of special functions
With a separately available programming board, all possible settings of the speed controller can
be programmed very easily. Pay attention to the notes at www.conrad.com on the corresponding
product page.
• Connect the speed controller with a drive battery, press the programming button (keep pressed!) and
switch on the speed controller. The red LED flashes.
Press and hold the programming button until the green LED flashes.
You are now in the programming environment and you can programme the menu items described below.
The 5 menu items are displayed in an endless loop.
1x flash is menu item 1, 2x flashes is menu item 2, etc. up to menu item 5. Subsequently, the
loop starts again with menu item 1.
Once the desired menu item is reached (1, 2, 3, 4 or 5), you can release the programming but-
ton. You are now in the sub-menu of the selected menu item.
The red LED now signals the current setting for the selected menu item.
• To select the desired setting in the sub-menu (for description, see c), press the programming button until
the red LED and the emitted sounds signal the desired setting.
Settings
Red LED f signal sound
1
1x short
2
2x short
3
3x short
4
4x short
5
1x long
6
1x long + 1x short
7
1x long + 2x short
8
1x long + 3x short
9
1x long + 4x short
• Once you have selected and programmed the desired setting, switch off the speed controller. This will
save the setting. If you want to programme another menu item, you must start the programming procedure
again.
c) Available programming options
Menu item 1 = Drive mode
Here, you can select the drive mode (1 = only forwards possible; 2 = forwards and reverse with pause when
changing possible; 3 = forwards and reverse without pause when changing possible).
When toggling between forwards and reverse in drive mode 2, the mode is not switched immediately, but with
a pause to protect the gears, wheels and battery capacity.
Menu item 2 = Motor brake
If the throttle lever on the transmitter is moved from the forwards position to idle, the motor brake is activated.
This function corresponds to the motor brake in a “real” car, when you lift your foot off the accelerator pedal
but do not step on the brake pedal.
The motor brake can be programmed in eight steps. The higher the set value, the stronger the brake. The
following values can be set:
1 = 0%; 2 = 5%; 3 = 10%; 4 = 20%; 5 = 40%; 6 = 60%; 7 = 80%, 8 = 100%
Menu item 3 = Low-voltage detection
The low-voltage detection is possible for the operation of the model with LiPo as well as NiMH batteries.
It is particularly recommended to activate this function when using LiPo batteries to avoid dangerous deep
discharge of the batteries.
For LiPo batteries, the set values refer to one voltage value per battery cell.
Example: When 3.0 V is set, a 2-cell battery would reach the low-voltage threshold at a battery voltage of
6.0 V (2 cells x 3.0 V = 6.0 V). The speed controller would now switch off the motor to avoid deep discharge
of the battery.
If you use a NiMH battery, the calculation of the number of cells is done based on the battery voltage meas-
ured by the speed controller when switching on. If a voltage of 9.0 to 12.0 V is detected after switching on the
speed controller, it is switched off as if using a 3-cell LiPo battery. If a voltage of less than 9.0 V is detected,
the speed controller is switched off as if using a 2-cell LiPo battery.
Example: If you connect a fully charged 6-cell NiMH battery with approx. 8.4 V of battery voltage and the
shutdown voltage per (LiPo) cell is set to 2.6 V, the low-voltage detection will switch off the motor when a
battery voltage of 5.2 V (2 x 2.6 V = 5.2 V) is reached.
The following setup values are possible:
1 = no low-voltage detection; 2 = 2.6 V/cell; 3 = 2.8 V/cell; 4 = 3.0 V/cell; 5 = 3.2 V/cell, 6 = 3.4 V/cell
We recommend to set 3.2 V/cell for LiPo batteries.
The battery voltage is monitored permanently. If a low-voltage is detected even momentarily, the
power is reduced to 50% for two seconds. The motor is switched off after another 10 seconds.
If the voltage of a LiPo battery is less than 3.5 V per cell, the speed controller can no longer be
activated. In this case, stop driving and recharge the battery fully.
Menu item 4 = Start dynamics
You can set the start dynamics in 9 steps with this function.
The higher the set value, the more aggressive the motor reacts to the control commands made at the trans-
mitter. It is important to note that the battery can deliver the current required for this (use LiPo battery with
higher C-rate). If the motor “stutters” on the highest start dynamics level and the battery is not flat (or powerful
enough), the gear ratio might have to be changed.
Menu item 5 = Brake effect
Here you can set the brake effect when moving the control lever at the transmitter during forwards driving
into the end stop position reverse (or brake).
The following values can be set: 1 = 25%; 2 = 50%; 3 = 75%; 4 = 100%.
The higher the set value, the stronger the brake effect. The higher the brake effect is set, the
higher the stress experienced by gears and wheels.
d) Restoring factory settings
If you press the programming button for approx. three seconds with the speed control switched on, the red
and the green LED will flash at the same time. Afterwards, only the red LED flashes and therefore indicates
that the factory settings were restored.
When restoring to factory settings, all previously made settings, including idle position programmes are reset.
Afterwards, you must programme the speed controller again starting with the programming of the idle posi-
tion.
To do this, switch off the speed controller and start re-programming (see “Programming of full throttle and
idle position”).
Connection to the receiver
Connect the three-pole plug of the speed controller to the corresponding channel of the receiver. Make
absolutely sure you have the correct receiver configuration (see operation instructions for the receiver as
well as the inscription on the receiver).
Yellow/white/orange connecting line: Control signal
Red cable: Operating voltage
Brown/black cable: GND/Minus
The speed controller features a BEC. This means that the battery supplies the receiver directly
with power via the speed controller. If the BEC is used as the power supply of the receiver unit,
do not use a receiver battery!
Important!
If a separate receiver power supply is used instead of the integrated BEC, the red wire in the
middle of the speed controller’s three-pin receiver plug has to be interrupted and insulated.
Failure to comply with this indication will destroy the trip controller! The warranty will be void!