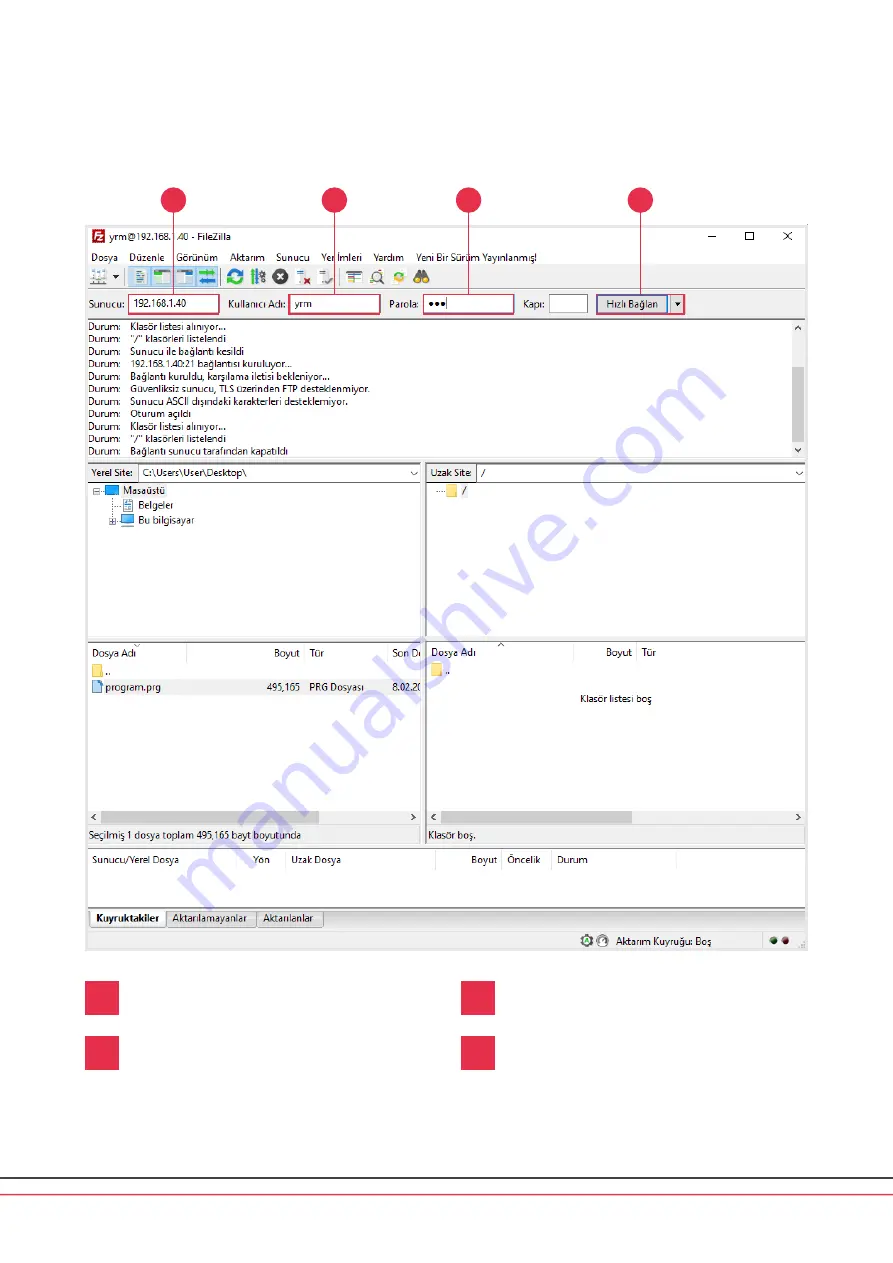
34
redon.com
INSTALLING PROGRAMS WITH FILEZILLA
3
2
1
4
Type the machine’s IP address in the
(Sunucu) (Server) field.
1
Type
(yrm) in the
(Kullanıcı Adı) (Username) field.
2
Type
(yrm) in the (Parola) (Password) field.
Establish a connection by clicking
the
(Hızlı Bağlan) (Quick Connect) button.
3
4
Summary of Contents for GTR
Page 1: ...REDON GTR USER MANUAL redon com ...
Page 2: ...redon com ...
Page 15: ...15 PRODUCT CONTENTS 8 mm x 7 5 mt Pneumatic Hose 1 Pc Network Cable 5 mt Air Gun ...
Page 41: ...41 USER INTERFACE JOG JOG Manuel Movement x y z ...
Page 42: ...42 redon com USER INTERFACE JOG JOG Manuel Movement ...
Page 44: ...44 redon com USER INTERFACE ATC ATC Main Menu Tool Changing ...
Page 83: ...83 NOTES ...
Page 84: ...84 redon com NOTES ...
Page 85: ...85 NOTES ...
Page 86: ...86 redon com NOTES ...
Page 87: ...87 NOTES ...
Page 88: ...redon com ...