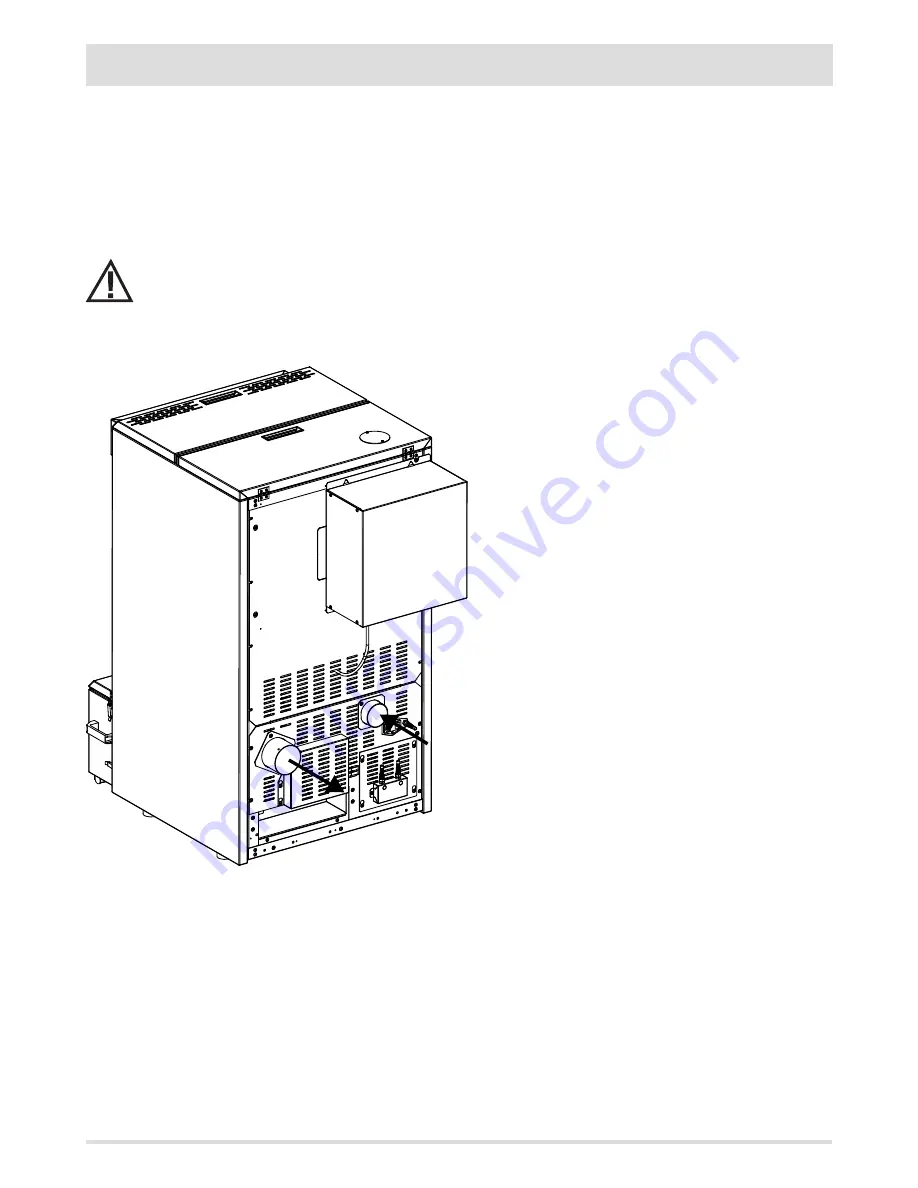
24
I
U
24
4-UNPACKING
The end user is responsible for product storage, disposal or possible recycling in compliance with the relative applicable
laws in force
. Position the product and proceed with connecting it to the chimney.
If the product must be connected to an exhaust pipe that goes through the rear wall (to enter the chimney), make sure not to force it in.
Attention!!
If the boiler smoke outlet is forced or used improperly to lift it or position it, the operation of the boiler can be
damaged irreparably.
U = SMOKE OUTLET DIAMETER 100 mm
I = COMBUSTION AIR INLET DIAMETER 80 mm