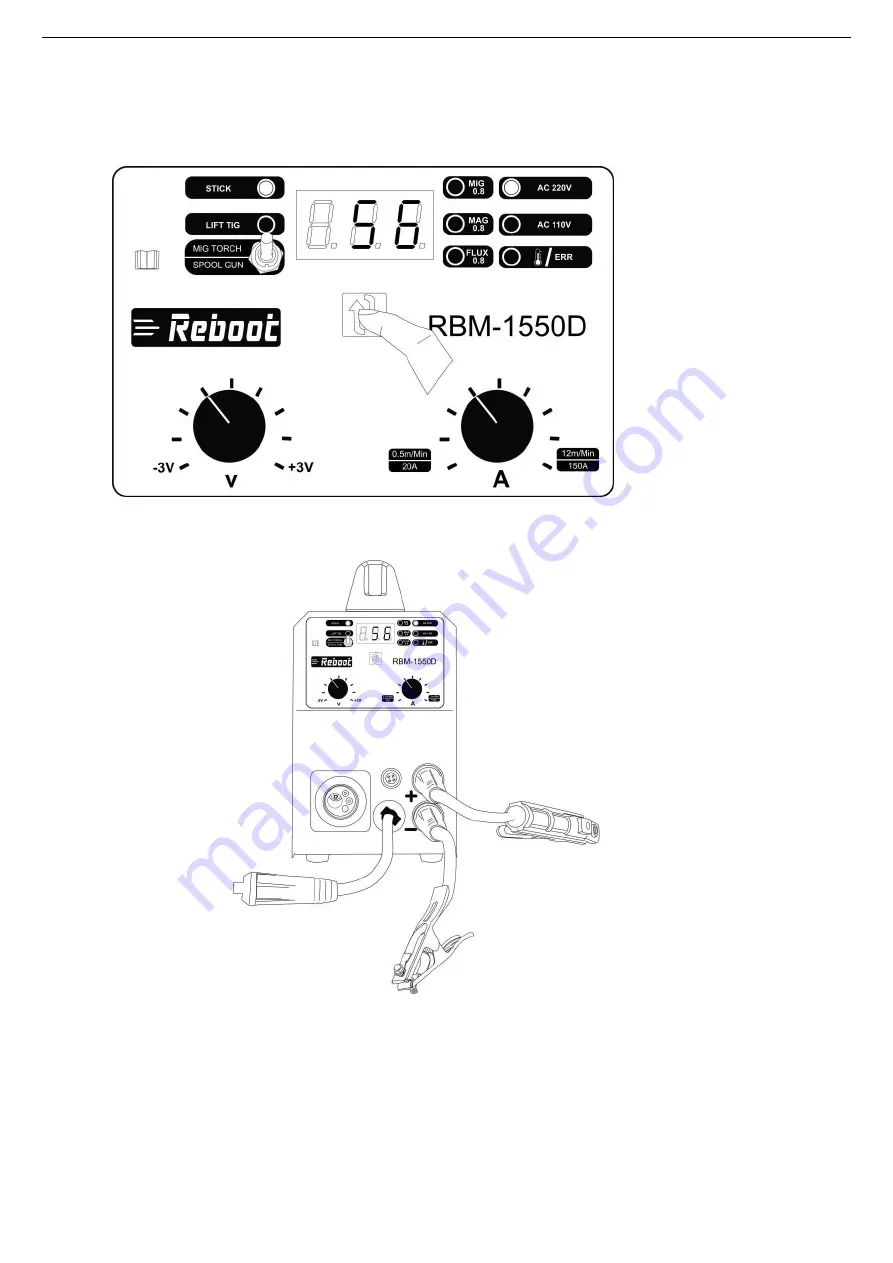
Version Number: RBM1550-20210414A1
5
If you want to repair some broken fences or fix brackets, you like to use traditional welding rods for operation,
you can use REBOOT RBM1600 MMA mode for welding.
1 Select “MMA” process.
2 Connect welding holder and ground clamp.
3 To adjust the current, Knob “A” only the current can be adjusted.
Note:
1) The welding rod specification supported by reboot RBM1600 is below 4.0(5/32in), usually 2.5(3/32in) and
3.2(1/8in). European style generally uses E6013, American style generally uses E7018, and stainless