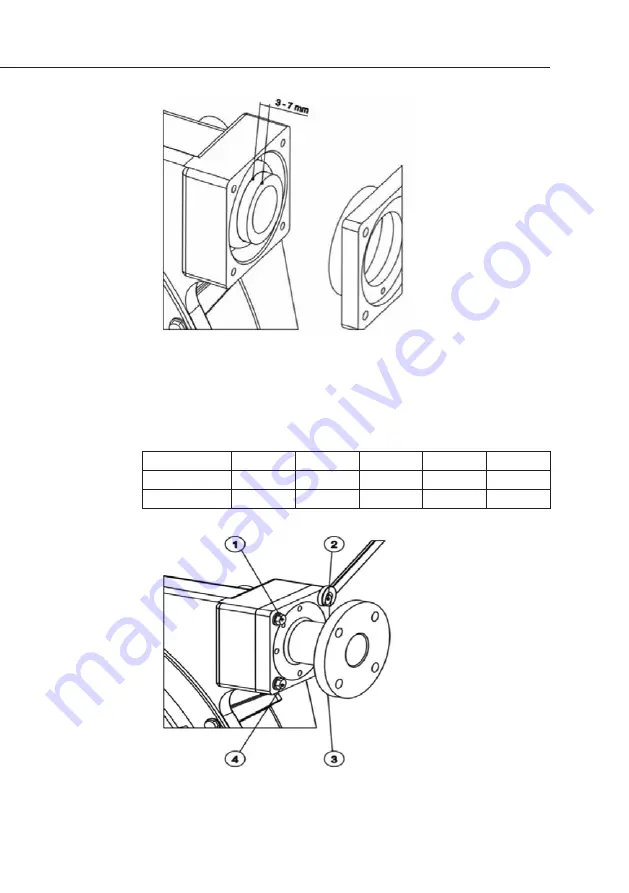
Operating instructions
Peristaltic Pump IP Series
17
Fig 5:
Way to proceed
with the screws
tightening.
6 Fasten the press flange and the connections to the pump
casing, tightening progressive the bolts in clock wise (1,
3, 2, 4, 1, 3, 2, 4, etc.), until the flange becomes totally
tighten.
Torque setting
Model
IP-30
IP-40
IP-50
IP-60
IP-70
Press flange
25 Nm
30 Nm
35 Nm
55 Nm
40 Nm
Connection
20 Nm
20 Nm
20 Nm
20 Nm
20 Nm
Fig 4:
Required distance
between the end
of the hose and
the press ring.