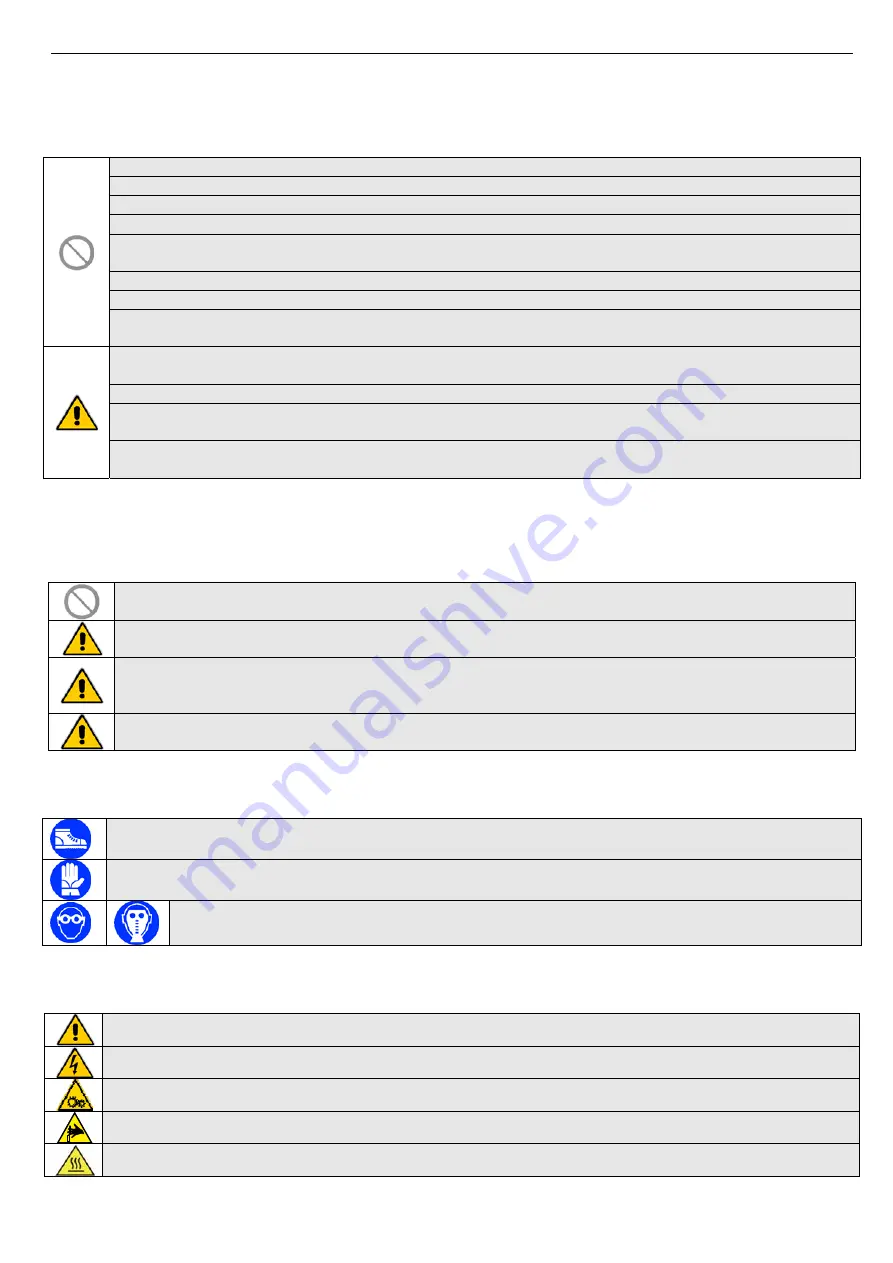
UM / UM PLUS
Chillers and inverter air / water heat pumps with axial fans
6
4
GENERAL SAFETY GUIDELINES
Before beginning to operate on UM / UM Plus units every user has to be perfectly knowledgeable about the functions of the
equipment and its controls and has to have read and understood the information listed in this manual.
It’s strictly forbidden to remove and/or tamper with any safety device.
Children or unassisted disabled persons are not allowed to use the appliance.
Do not touch the appliance when barefoot or parts of the body are wet or damp.
Do not clean the unit when the power is ‘ON’.
Do not pull, remove or twist the electrical cables coming out from the unit, even if it is disconnected from the main
power supply.
Do not step with your feet on the appliance, sit down and/or place any type of object.
Do not spray or pour water directly on the unit.
Do not dispose of, abandon or leave within reach of children packaging materials (cardboard, staples, plastic bags,
etc.) as they may represent a hazard.
Any routine or not-routine maintenance operation shall be carried out when the equipment has been shut down,
disconnected from electric power sources.
Do not put neither your hands nor insert screwdrivers, spanners or other tools into moving parts of the equipment.
The equipment supervisor and the maintenance man have to receive suitable training for the performance of their
tasks in safety.
Operators have to know how to use personal protective devices and have to know the accident-prevention guidelines
contained in national and international laws and norms.
4.1
WORKERS’ HEALTH AND SAFETY
The European Community has adopted a number of directives on workplace’s health and safety, which include 89/391/CEE,
89/686/CEE, 2009/104/CE, 86/188/CEE and 77/576/CEE directives. Every employer shall implement such provisions and ensure
that their workers to respect them. We observe therefore that
Do not tamper with or replace parts of the equipment without the specific consent of the manufacturer. The
manufacturer shall have no responsibility whatsoever in case of unauthorised operations.
Using components, expendable materials or spare parts that do not correspond to those recommended by the
manufacturer and/or listed in this manual may be dangerous for the operators and/or damage the equipment
The operator’s workplace has to be kept clean, tidy and free from objects that may prevent free movements.
Appropriate lighting of the work place shall be provided so as to allow the operator to carry out the required
operations safely. Poor or too strong lighting can cause risks.
Ensure that work places are always adequately ventilated and that aspirators are working, in good condition and in
compliance with the requirements of the laws in force.
4.2
PERSONAL SAFETY EQUIPMENTS
When operating and maintaining the UM / UM Plus units, use the following personal protective equipment.
Protective clothing: Maintenance men and operators have to wear protective clothing that complies with the basic
safety requirements currently in force. In case of slippery floors, users have to wear safety shoes with non-slip soles.
Gloves: During maintenance or cleaning operation protection gloves have to be used
Mask and goggles: Respiratory protection (mask) and eye protection (goggles) should be used during
cleaning and maintenance operations.
4.3
SAFETY SYMBOLS
The unit features the following safety signs, which has to be complied with:
General hazards
Electric
shock
hazard
Presence of moving organs
Presence of surfaces that may cause injures
Presence of hot surfaces that can cause burns