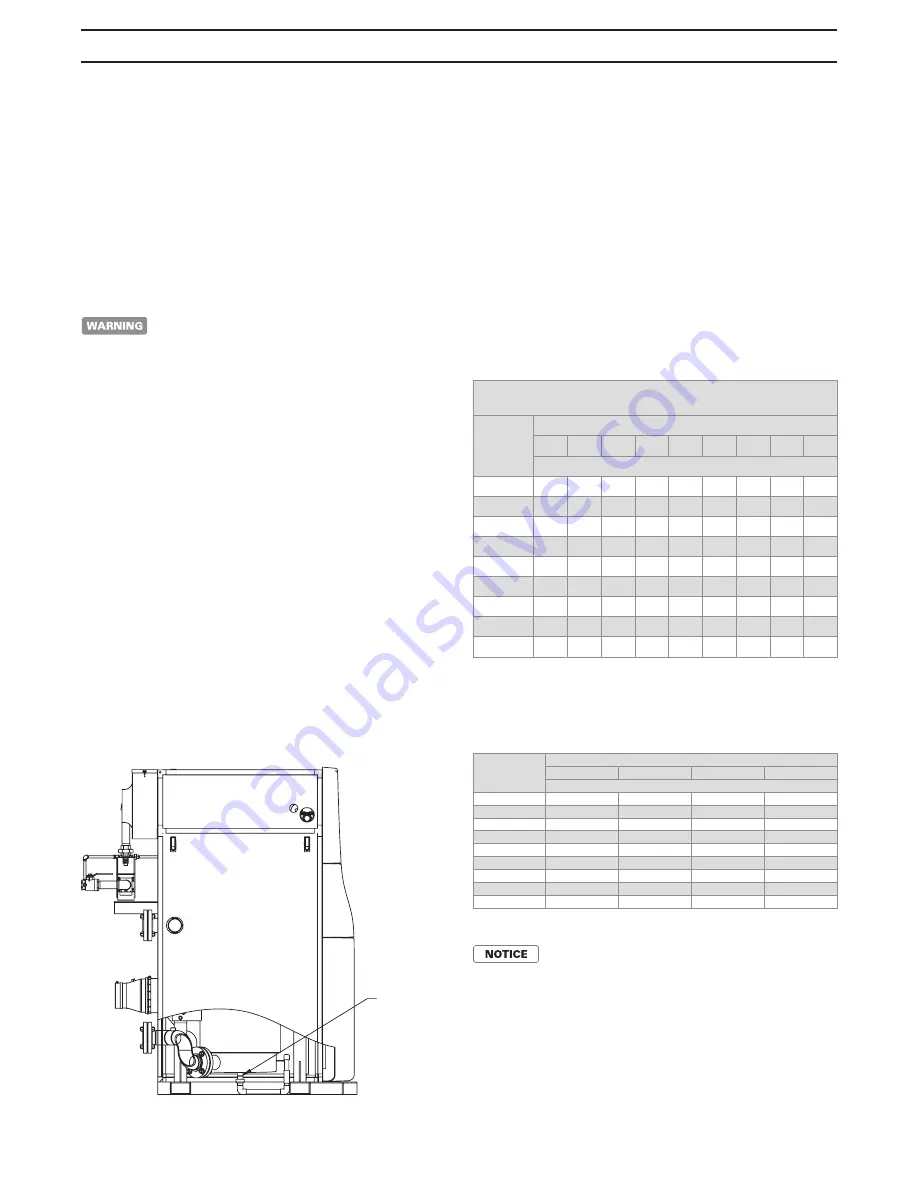
25
Cast Iron Condensing Boilers – Installation Manual
FlexCore Stainless Steel Condensing Boilers – Installation Manual
Figure 17 depicts the proper way to connect the boiler
to the gas supply piping. The manual shut-off valve
MUST be installed in the supply piping. It should be
installed
5 ft, 1 m above the floor where required by
local codes. Provide a sediment trap at the bottom of the
vertical section of the gas supply pipe upstream of the
gas controls.
A ground joint union should be installed between the
boiler gas controls and the supply piping. Each of these
items are needed to ensure long life and ease of
servicing. Always use a pipe sealant that is suitable for
use with with the type of gas (NG/LP) being used.
Table 8 - Gas Pipe Capacity
Figure 16 - FlexCore Series Condensate Drain
CONDENSATE PIPING
The condensate trap provided with the boiler must be
attached to the bottom pan and piped to a suitable floor
drain (consult local code) or condensate pump. If a
condensate neutralization device is required by local
code, it must be positioned prior to boiler room drain. Fill
the condensate trap with water, check and maintain water
level in trap during operation prior to start-up.
GAS SUPPLY PIPING
Check the boiler rating plate to make sure that
the boiler is for the type of gas that
will be used. If it isn’t, do not connect the
boiler to the gas supply. Failure to comply with
this warning can result in extensive property
damage, severe personal injury or death!
The FlexCore comes from the factory ready to be piped
to the gas supply. If for any reason the boiler is not for
the type of gas available at the installation site, call your
RBI representative to resolve the problem.
Table 8 should be used to ensure that the gas supply
piping is sized properly. If more than one appliance is
supplied by the same supply pipe, the piping must be
sized based on the maximum possible demand. Do not
neglect the pressure drop due to pipe fittings. Table 8
should be used in conjunction with Table 9 to ensure
that the gas supply piping has the capacity to meet the
demand.
Maximum pipe capacity in ft
3
/hr based on 0.60 specific gravity gas
at a pressure of 0.5 psig or less and a 0.3" WC pressure drop.
Nominal
Iron Pipe
Size
Pipe length in feet
10
20
30
40
50
60
80
100
150
Maximum gas volume of pipe (ft
3
/hr)
1"
520 350 285 245 215 195 170 150 120
1
1
/
4
"
1050 730 590 500 440 400 350
305
250
1
1
/
2
"
1600 1100 890 760 670 610 530
460
380
2"
3050 2100 1650 1450 1270 1150 990
870
710
2
1
/
2
"
4800 3300 2700 2300 2000 1850 1600 1400 1130
3"
8500 5900 4700 4100 3600 3250 2800 2500 2000
4"
17,500 12,000 9700 8300 7400 6800 5800 5100 4100
5"
31,700 21,800 17,500 15,000 31,300 12,000 10,300 9110 7320
6"
51,300 35,300 28,300 24,200 21,500 19,500 16,700 14,800 11,900
Note: Multiply the gas volume by 0.62 for propane flow capacity in
ft
3
/hr. Multiply the propane flow capacity by 2500 Btu/ft3 to determine
the propane Btu/hr capacity for a given pipe size and length.
Table 9 - Equivalent Pipe Length Chart
A lockup style regulator, supplied by others,
must be installed, see Figure 17, if gas
pressure exceeds (14 in WC). The regulator,
when installed as shown, must be installed
at a distance of at least 10 pipe diameters
from the boiler main gas valve. All boilers are
calibrated and factory test fired at
(7 in ± 1.0) WC.
Nominal
Iron Pipe
Size
Type of pipe fitting
90° Elbow
Tee
1
Gas Valve
2
Gas Cock
2
Equivalent pipe length, (ft)
1"
2.6
5.2
0.6
1.5
1
1
/
4
"
3.5
6.9
0.8
1.9
1
1
/
2
"
4.0
8.0
0.9
2.3
2"
5.2
10.3
1.2
3.0
2
1
/
2
"
6.2
12.3
1.4
3.5
3"
7.7
15.3
1.8
4.5
4"
10.1
20.2
2.4
6.0
5"
12.6
25.2
2.9
7.3
6"
15.2
30.4
3.5
13.4
Notes: 1. For flow through branch.
2. For flow at full open.
CONDENSATE
DRAIN
RIOM-0214_A