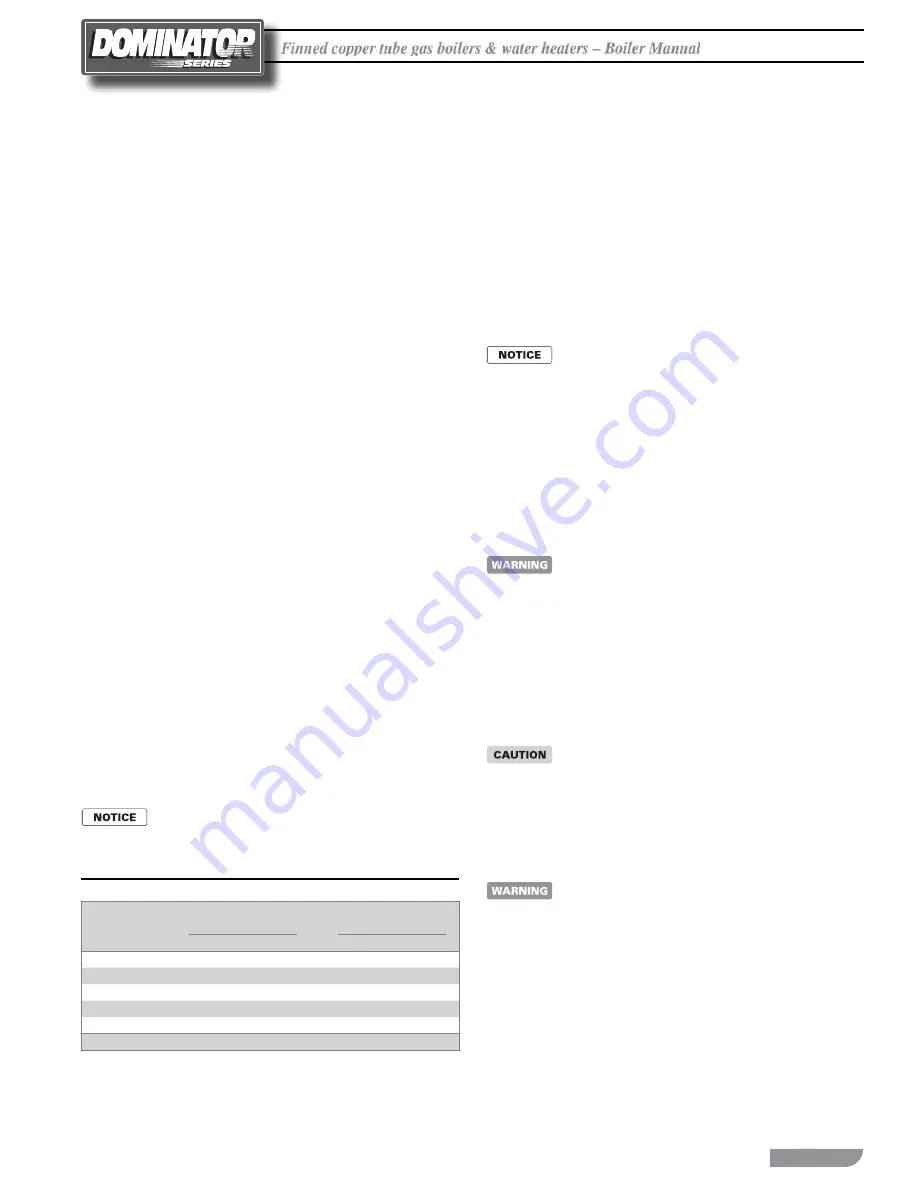
Fi
d
b
b il
&
h
B il
M
l
Finned copper tube gas boilers & water heaters – Boiler Manual
3
F
F
In Canada, the installation must be in accordance with the
requirements of CSA B149.1 or .2, Installation Code for Gas Burning
Appliances and Equipment.
If installed in the Commonwealth of Massachusetts, you MUST
FOLLOW the additional instructions contained in the back of this
manual, MACODE-3.
The owner should maintain a record of all service work performed
with the date and a description of the work done. Include the name
of the service organization for future reference.
Direct all questions to your RBI distributor or contact the
RBI Customer Service Department, 260 North Elm Street, Westfield,
MA 01085 for U.S. or 7555 Tranmere Drive, Mississauga ONT
L5S 1L4 for Canada. Always include the model and serial numbers
from the rating plate of the boiler/water heater in question.
RATINGS & CAPACITIES
Before undertaking the installation of the Dominator Series boil-
er/water heater check the rating plate to ensure that the unit has
been sized properly for the job. The "Net I=B=R Ratings" specify
the equivalent amount of direct copper radiation that the unit
can supply under normal conditions. Also ensure that the unit
has been set up for the type of gas available at the installation
site. Other important considerations are the availability of an adequate
electrical supply, fresh air for combustion and a suitable chimney
or vent system.
BOILER/WATER HEATER LOCATION
1. This boiler/water heater is suitable for indoor and outdoor instal-
lations. Locate the boiler/water heater in an area that provides
good access to the unit. Servicing may require the removal of
jacket panels. Allow the minimum clearances between adjacent
construction and the boiler/water heater as listed in Table 1.
Service clearances are not mandatory, but are
recommended to ensure ease of service should it be
required.
Table 1
Clearance to
Combustibles
Service
Clearance
in
mm
in
mm
Top
6
153
20
508
Back
6
153
24
610
Left Side
6
153
24
610
Right Side
6
153
24
610
Front
6
153
30
762
Flue
6
153
2. An optimum site will be level, central to the piping system, close
to a chimney or outside wall and have adequate fresh air for
combustion. Ensure that the boiler/water heater is level from
front to back and from side to side. Use metal shims to level
the boiler/water heater. Electrical and electronic components
must also be protected from exposure to water during operation
and maintenance. DO NOT install this boiler/water heater in
a location that would subject any of the gas ignition components
to direct contact with water or excessive moisture during
operation or servicing.
3. Ensure that the floor is structurally sound and will support the
weight of the boiler/water heater.
The Dominator may be installed directly on combus-
tible flooring, but never on carpeting.
4. Locate the boiler/water heater in an area that will prevent water
damage to adjacent construction should a leak occur or during
routine maintenance. If such a location doesn't exist, a suitable
drain pan that's adequately drained must be installed under the
unit.
5. DO NOT place this boiler/water heater in a location that would
restrict the introduction of combustion air into the unit or subject
the air inlet to a negative pressure, see “GENERAL VENTING
GUIDELINES”.
Never store combustible materials, gasoline or any
product containing flammable vapors or liquids in the
vicinity of the boiler/water heater. Failure to comply
with this warning can result in an explosion or fire
causing extensive property damage, severe personal
injury or death!
6. NEVER place this boiler/water heater in a location that would
subject it to temperatures at or near freezing. See the “Freeze
Protection” section on page 13.
Units installed outdoors MUST be protected from ice
and snow accumulation or the unit may be damaged
voiding the warranty!
COMBUSTION AIR & VENTILATION
This boiler/water heater must be supplied with
combustion air in accordance with Section 5.3, Air
for Combustion & Ventilation, of the latest revision
of the National Fuel Gas Code, ANSI Z223.1/NFPA
54 and all applicable local building codes. Canadian
installations must comply with CSA B149.1 or .2
Installation Code for Gas Burning Appliances and
Equipment, or applicable provisions of the local
building codes. Failure to provide adequate combustion
air for this boiler/water heater can result in excessive
levels of carbon monoxide which can result in severe
personal injury or death!