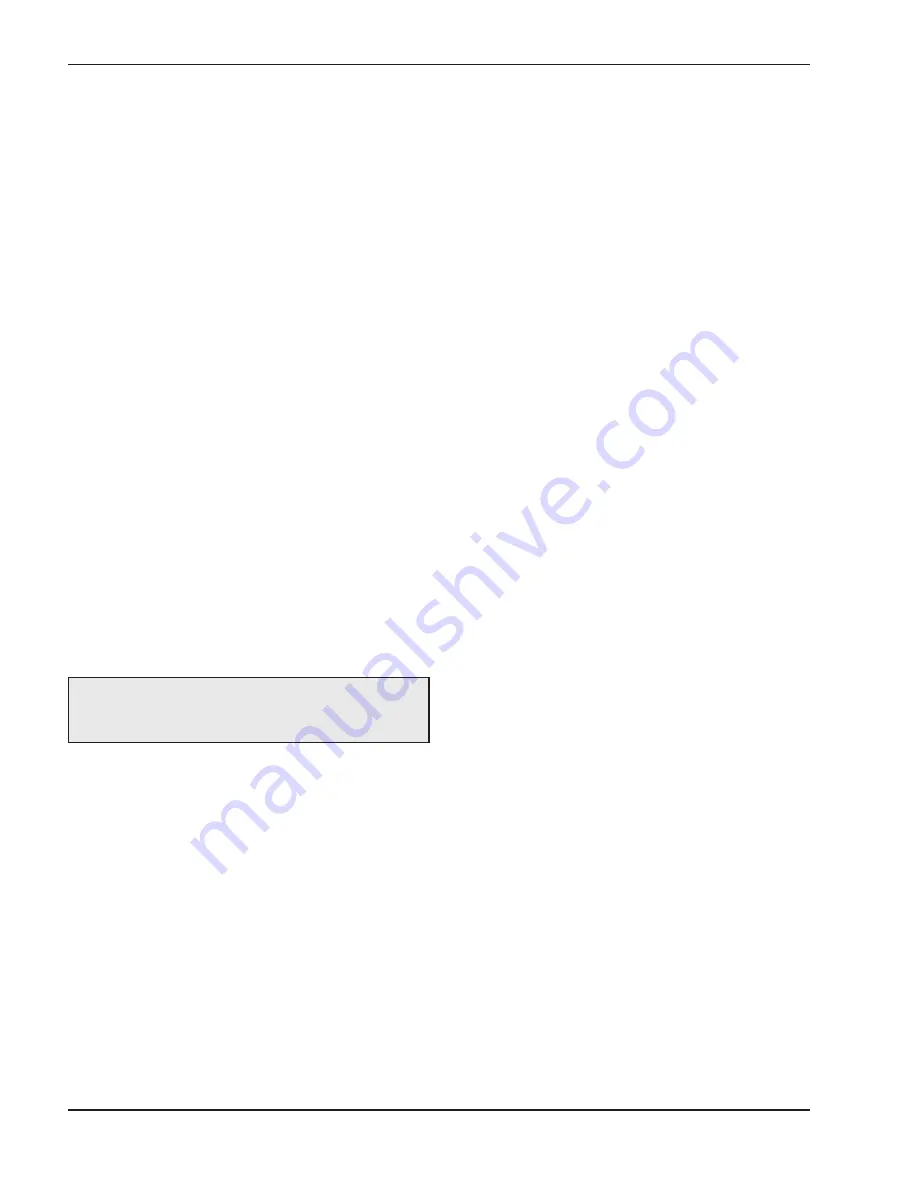
30
Vent Terminal Location
1. Condensate can freeze on the vent cap. Frozen
condensate on the vent cap can result in a blocked
flue condition.
2. Give special attention to the location of the vent
termination to avoid possibility of property dam-
age or personal injury.
3. Gases may form a white vapor plume in winter.
The plume could obstruct a window view if the
termination is installed near windows.
4. Prevailing winds, in combination with below-freez-
ing temperatures, can cause freezing of
condensate and water/ice build-up on buildings,
plants or roofs.
5. The bottom of the vent terminal and the air intake
shall be located at least 12 in. above grade, includ-
ing normal snow line.
6. Un-insulated single-wall Category IV metal vent
pipe shall not be used outdoors in cold climates
for venting gas-fired equipment without insulation.
7. Through-the-wall vents for Category IV appli-anc-
es shall not terminate over public walkways or
over an area where condensate or vapor could
create a nuisance or hazard or could be detrimen-
tal to the operation of regulators, relief valves, or
other equipment.
8. Locate and guard vent termination to prevent
acci-dental contact by people or pets.
9. DO NOT terminate vent in window well, stairwell,
alcove, courtyard or other recessed area.
10. DO NOT terminate above any door, window, or
gravity air intake. Condensate can freeze, causing
ice formations.
11. Locate or guard vent to prevent condensate from
damaging exterior finishes. Use a rust-resistant
sheet metal backing plate against brick or mason-
ry surfaces.
12. DO NOT extend exposed vent pipe outside of
building beyond the minimum distance required
for the vent termination. Condensate could freeze
and block vent pipe.
U.S. Installations
Refer to the latest edition of the National Fuel Gas
Code.
Vent termination requirements are as follows:
1. Vent must terminate at least 4 ft below, 4 ft
hori-zontally from or 1 ft above any door, window
or gravity air inlet to the building.
2. The vent must not be less than 7 ft above grade
when located adjacent to public walkways.
3. Terminate vent at least 3 ft above any forced air
inlet located within 10 ft.
4. Vent must terminate at least 4 ft horizontally, and
in no case above or below unless 4 ft horizontal
distance is maintained, from electric meters, gas
meters, regulators, and relief equipment.
NOTE:
During winter months check the vent cap
and make sure no blockage occurs from build-up of
snow or ice.
Use only the special gas vent pipes listed for use
with Category IV gas burning heaters, such as the
AL29-4C stainless steel vents offered by Heat Fab
Inc. (800-772-0739), Protech System, Inc. (800-766-
3473), Z-Flex (800-654-5600) or American Metal
Products (800-423-4270). Pipe joints must be positive-
ly sealed. Follow the vent manufacturer’s installation
instructions carefully.
Extractors, Draft Inducers, and Motorized Flue
Dampers
When extractors or inducers are used in the vent-
ing system, they must be interlocked with each
connected appliance, to ensure proper operation. If
individual motorized dampers are used, they must be
interlocked to their respective appliance. See Field
Wiring Connection section of this manual for proper
wiring instructions, using Fan/Damper dry contacts
and external interlock.
Support of Vent Stack
The weight of the vent stack or chimney must not
rest on the heater vent connection. Support must be
pro-vided in compliance with applicable codes. The
vent should also be installed to maintain proper clear-
ances from combustible materials. Use insulated vent
pipe spacers where the vent passes through combus-
tible roofs and walls.