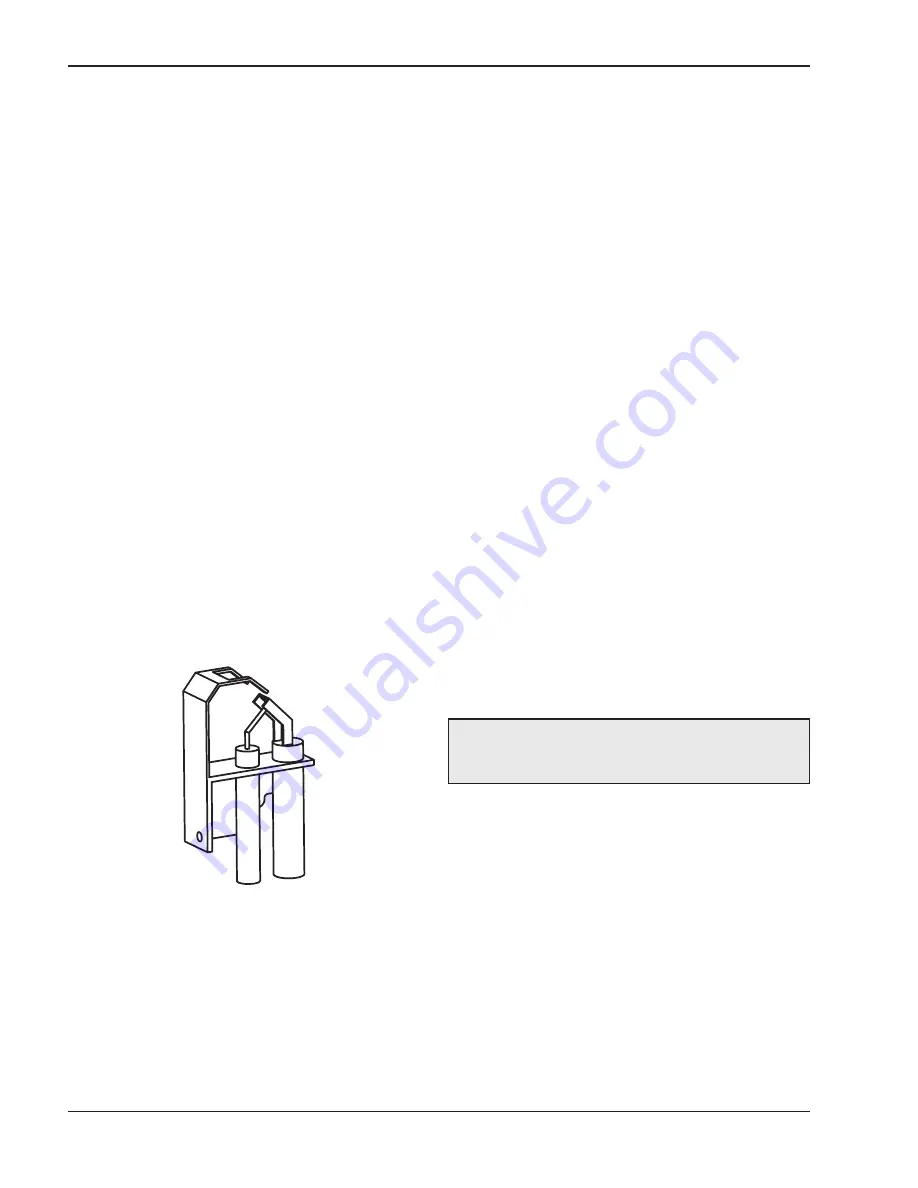
28
10. Carefully slide out the burner tray assembly.
11. Reverse above procedure to reinstall.
Gas Valve Removal
1. Shut off main electrical power switch to heater.
2. Shut off gas supply to the heater.
3. Remove front door.
4. Disconnect gas line from gas valve.
5. Disconnect wires, pilot tubing and bleed line, if
required.
6. Remove (2) screws that secure gas valve to jack-
et.
7. Turn vertical gas pipe from manifold slightly and
unscrew gas valve.
8. Reverse above procedure to re-install.
Main Burner And Orifice Removal
1. Remove burner drawer. See burner drawer
removal procedure.
2. Remove (8) screws from the hold down brackets.
3. Remove (8) screws from the left and right sides of
the Manifold assembly. Detach the manifold
assembly from the burner tray assembly.
4. Use a long 3/8” socket wrench to remove orifices
from the atmospheric gas manifold, 9/16” for Low
NOx.
5. Remove burners by raising the bracket on the
back end of the burners up and out of their slots.
6. Reverse above procedure to re-install.
Pilot Removal
1. Disconnect pilot tubing from gas valve.
2. Remove (4) screws from control box. Open the
control box.
3. Remove the pilot wire from the ignition wire.
4. Remove (2) screws that mount the pilot bracket to
the air manifold assembly.
5. Pull the pilot bracket downward and outward.
6. Reverse above procedure to re-install.
Combustion Fan Removal
1. Remove burner drawer. See burner drawer
removal procedure.
2.
Remove (4) screws the mount the combustion
blower to the manifold assembly.
3. Reverse above procedure to re-install.
Normal Inspection Procedures
First and third month after initial start up and then on
an annual basis. If problems are found, refer to
Trouble Shooting Guide for additional directions.
1. Remove top of heater and inspect heat exchanger
for soot and examine venting system.
2. Remove rear header and inspect for scale
deposits.
*3. Inspect pilot and main burner flame and firing rate.
*4. Inspect and operate all controls and gas valve.
*5. Visually inspect system for water leaks.
*6. a.
Oil pump motor and bearing assembly, if oil
cups are provided.
b. Disconnect pump from header and check con-
dition of pump impeller. Check condition of
bearing by attempting to move impeller from
side to side. Replace any parts showing wear.
c. Check pump coupler for wear and vibration.
7. Check flow switch paddle (if provided).
8. Clean room air intake openings to assure ade-
quate flow of combustion and ventilation air.
9. Keep heater area clear and free from combustible
materials, gasoline, and other flammable vapors
and liquids.
*Should be checked monthly. (Takes approximately
15 minutes).
Repair Section
Tube Cleaning Procedure (Typical)
Establish a regular inspection schedule, the frequency
depending on the local water condition and severity of
service. Do not let the tubes clog up solidly. Clean out
deposits over 1/16" in thickness.
Fig. 32: IID Pilot
CAUTION:
Combustion air must not be contami-
nated by corrosive chemical fumes which can
damage the heater and void the warranty.
Summary of Contents for 2600401
Page 17: ...17 Wiring Diagrams Fig 15 Standing Pilot Model 0260 FIELD INSTALLED...
Page 18: ...18 Fig 16 Intermittent Ignition Device IID Model 0260...
Page 19: ...19 Fig 17 Intermittent Ignition Device IID Models 0330 0400...
Page 20: ...20 Fig 18 Intermittent Ignition Device IID Model 0261 Low NOx...
Page 21: ...21 Fig 19 Intermittent Ignition Device IID Models 0331 0401 Low NOx...
Page 37: ...37...
Page 38: ...38...
Page 39: ...39...