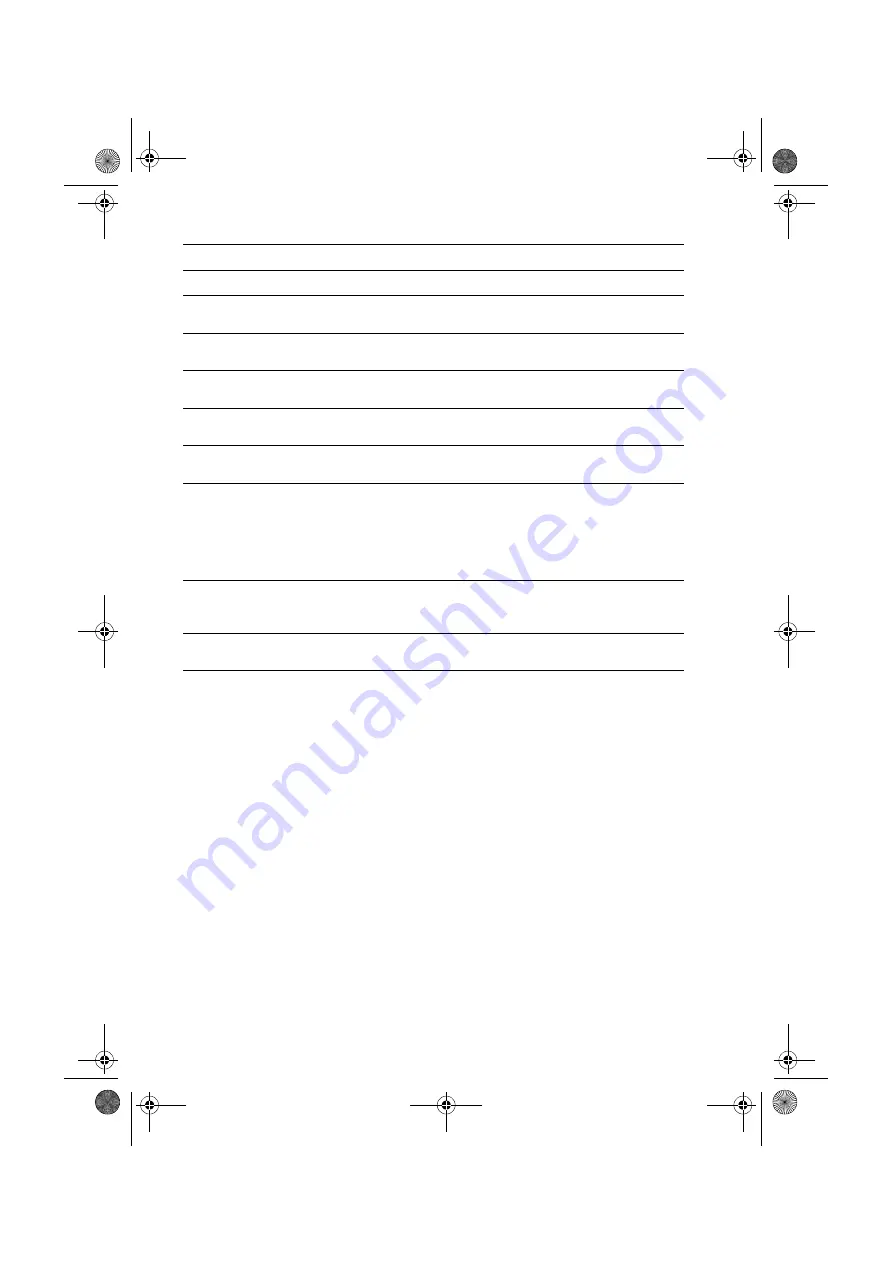
30
General maintenance
Wheel drive
Routine maintenance
After each trip, flush inside the drive unit by inserting a hose pipe
in the free slot on the back cover.
The autopilot will not ‘talk’ to other
SeaTalk instruments
Cabling problem – make sure all the cables are
connected properly.
Position information not received
Navigator not transmitting the correct position
data.
The autopilot will not auto advance to
the next waypoint
No bearing to waypoint information received
from the navigator.
The control unit display shows a series
of rotating dashes
Compass deviation correction is running
The control unit display shows a series
of stationary dashes
The control unit is not receiving data – check the
cabling.
The control unit display shows
NO DATA
The signals received by the navigator are too
weak for reliable navigation – refer to the
navigator handbook for further action.
OR
Wind trim data is not available – check the
connection to the wind instrument.
Wheel drive: drive belt slips in Auto
mode (motor operates but drive does
not turn wheel)
Tighten the clutch
Wheel drive: drive belt drags in
Standby mode
Loosen the clutch
SYMPTOM
SOLUTION
81131_8.book Page 28 Thursday, October 7, 2004 11:03 AM
Summary of Contents for E12093
Page 2: ...81131_8 book Page 118 Thursday October 7 2004 11 03 AM...
Page 6: ...81131_8 book Page 37 Thursday October 7 2004 11 03 AM...
Page 37: ...81131_8 book Page 76 Thursday October 7 2004 11 03 AM 35...
Page 38: ...User notes 81176_4 fm Page 22 Tuesday April 18 2006 9 26 AM...
Page 39: ...User notes 81176_4 fm Page 22 Tuesday April 18 2006 9 26 AM...
Page 40: ...www raymarine com...