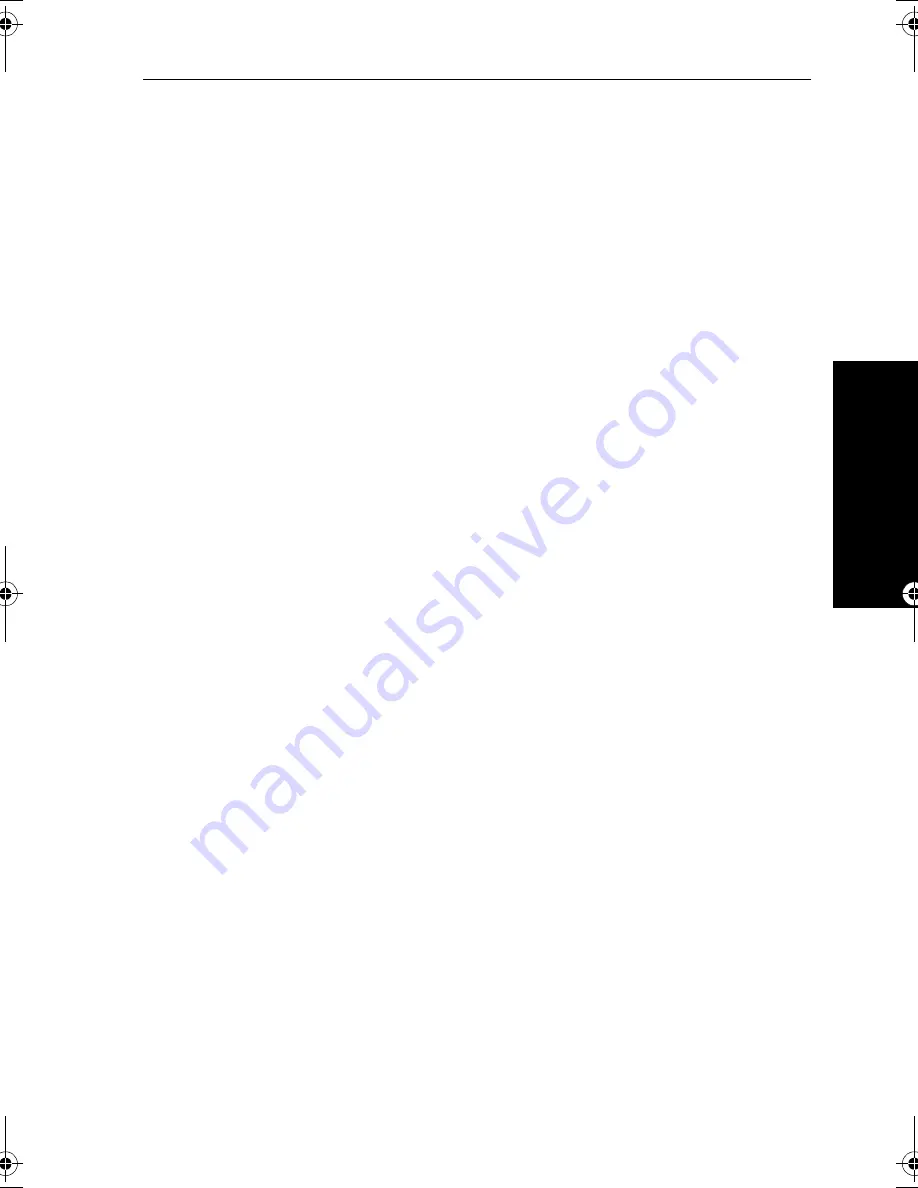
Chapter 2: Using the Wheel Pilot
17
2
U
sin
g
the Wh
eel
Pi
lo
t
2.4 Using Track mode
In Track mode, the wheel pilot maintains a track between waypoints
created on a navigation system. The wheel pilot computes any course
changes to keep your boat on track, automatically compensating for
tidal streams and leeway. To operate in Track mode, the wheel pilot
must receive cross track error information from either:
•
a SeaTalk navigator, or
•
a non-SeaTalk navigation system transmitting NMEA 0180 or
0183 data
Note: using NMEA 0180 navigators
NMEA 0180 equipment only transmits cross track error up to ±0.3
nm. This means that even if you are 5 nm to starboard of track, the
transmitted data will still be 0.3 nm.
If you attempt to engage Track mode with the boat more than 0.3 nm
from track, the boat will overshoot excessively and may even circle.
For this reason, the Larger Cross Track Error alarm (seepage 24) is
displayed whenever cross track error is 0.3 nm or greater.
The requirement to remain within 0.3 nm of track also limits the
maximum allowable angular error between the track course and the
boat’s heading. If the angular error is too great, the autopilot will be
unable to cancel it within the 03 nm limit, leading to the problems
outlined above.
NMEA 0183 transmit cross track error up to 99.99 nm and so enables
Track mode to operate with larger cross track errors. However, the
autopilot will still display the alarm if cross track error exceeds
0.3 nm in case there are any hazards close to the intended track.
Selecting Track mode
When you select Track mode, the wheel pilot can acquire the track in
one of two ways:
•
automatic acquisition – when both cross track error and bearing to
waypoint data are available
•
manual acquisition – when Cross Track Error is the only available
information
81194_1.book Page 17 Wednesday, July 25, 2001 12:10 PM
Summary of Contents for Autohelm ST3000
Page 2: ...ST3000 Wheel Drive Autopilot Owner s Handbook Document number 81194 1 Date June 2001...
Page 11: ...6 ST3000 Wheel Drive Autopilot Owner s Handbook 1 Introduction...
Page 12: ...Part 1 Using the Wheel Pilot Part 1 Using the Wheel Pilot...
Page 13: ...Part 1 Using the Wheel Pilot...
Page 33: ...28 ST3000 Wheel Drive Autopilot Owner s Handbook 2 Using the Wheel Pilot...
Page 37: ...32 ST3000 Wheel Drive Autopilot Owner s Handbook 3 Maintenance Fault Finding...
Page 38: ...Part 2 Installing the Wheel Pilot Part 2 Installing the Wheel Pilot...
Page 39: ...Part 2 Installing the Wheel Pilot...
Page 73: ......