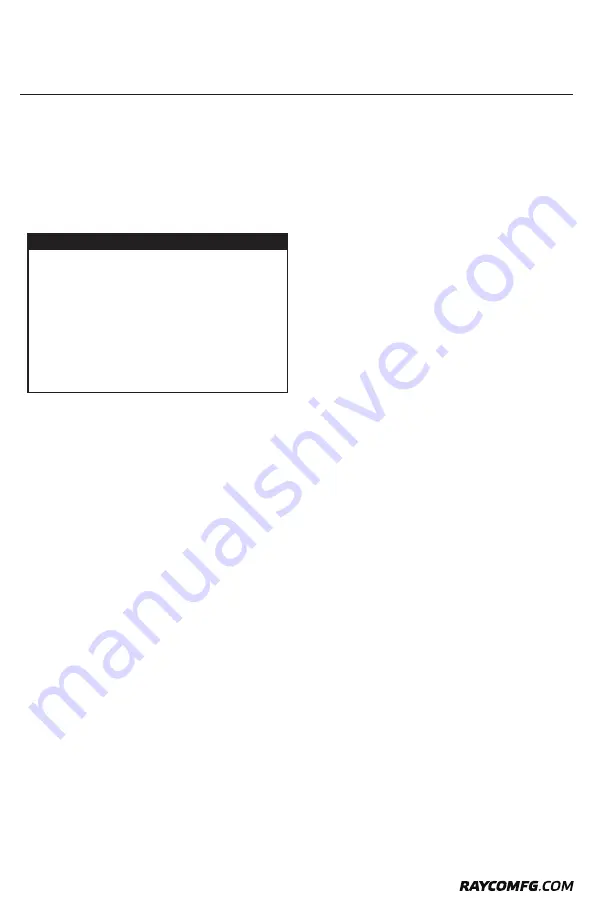
RCT150A Operator • Service • Maintenance Manual
28
Allow the engine to warm up before increasing throttle
Starting Procedure Continued
1. Only responsible, properly instructed individ u als should
operate this ma chine. Inexperienced operators must
always be carefully supervised.
2. Make sure that no one is working on, under neath or close
to the machine before starting the engine or beginning
to move the ma chine. Make sure that the area is free of
personnel.
3. Make no alterations or modifications to your Rayco
crawler unless requested or rec om mend ed by Rayco
Manufacturing Inc.
4. Start the engine only from the operator’s seat. Never
“short” across the starter terminals, or across the battery.
Shorting can damage the electrical system.
5. Inspect the condition of the seat belt and its mounting
hardware. Replace any parts that are worn or damaged in
any way. Regardless of appearance, replace the seat belt
every three years. Do not use a belt extension.
6. Make sure that no one is working on, under neath or close
to the machine before starting the engine or beginning
to move the ma chine. Make sure that the area is free of
personnel.
7. Make no alterations or modifications to your Rayco
crawler unless requested or rec om mend ed by Rayco
Manufacturing Inc.
8. Make sure that all machine lights are working properly.
Make sure that the machine lighting system can sufficiently
illuminate the job site. If more lighting is required, set up
auxiliary lighting before attempting to work.
9. When starting the engine, the machine controls which
cause machine movements must be in the OFF position.
These controls include joysticks and joystick buttons and
switches. These controls are self centering and default
to OFF, or are illuminated to indicate the need to turn
off before starting. Make sure that nothing is leaning or
pressing against any of these controls when starting the
engine. Unexpected movement can cause death, personal
injury, or property damage.
10. Do not start the engine or move any of the controls if
there is a “DO NOT OPERATE” or similar warning tag
attached to the machine.
11. Check with the local utilities for the locations of buried
pipes and cables where applicable, before operating
the machine.
12. Clear all personnel from the machine and from the area.
13. Clear all obstacles from the path of the machine. Beware
of hazards such as wires, ditches, etc.
14. Make sure that all windows are clean. Secure the door
in the closed position.
15. 1Adjust the rear view mirrors to allow for optimal vision.
16. Make sure that the machine backup alarm, horn (if
equipped) and all other warning devices are working
properly.
Rollover Protective Structure
(ROPS)
• To avoid the possible weakening of the ROPS/FOPS
structure, do not alter the structure by welding, cutting,
adding weight, or drilling holes into the structure.
• Do not mount fire extinguishers, first aid kits, lights or other
items to the ROPS/FOPS structure. Welding brackets
or drilling holes in the ROPS/FOPS can weaken the
structure. See your Rayco dealer for mounting guidelines.
• Any alteration that is not specifically authorized by Rayco
invalidates the certification for the ROPS/FOPS. The
protection that is offered by the ROPS/FOPS will be
impaired if the ROPS/FOPS has structural damage.
Damage to the structure can be caused by an overturn,
falling objects, etc.
• Use of the ROPS/FOPS in a damaged, modified or
abused condition, or with a prior overturn, is unsafe
and the operator protection is no longer suitable and
must be replaced.
Operation
NOTICE
The operator must be satisfied that no one is
endangered before lowering the attachments.
All machine controls are controlled by pilot pressure.
This means that the machine controls cannot be
manipulated with the engine off. If the engine
cannot be started to lower the attachments to the
ground, then the attachments should be supported
with suitable jack stands or an equivalent, until the
machine is serviced and the engine can be started.
Summary of Contents for RCT150A 2019
Page 48: ...RCT150A Operator Service Maintenance Manual 48 Hydraulic Schematic 806401 Rev A 210 bar ...
Page 49: ...RCT150A Operator Service Maintenance Manual 800 392 2686 49 Hydraulic Schematic 806401 Rev A ...
Page 50: ...RCT150A Operator Service Maintenance Manual 50 Hydraulic Schematic 806401 Rev A ...
Page 52: ...RCT150A Operator Service Maintenance Manual 52 Hydraulic Schematic 806401 Rev A ...
Page 53: ...RCT150A Operator Service Maintenance Manual 800 392 2686 53 Hydraulic Schematic 806401 Rev A ...
Page 62: ...RCT150A Operator Service Maintenance Manual 62 Troubleshoot ...
Page 63: ...RCT150A Operator Service Maintenance Manual 800 392 2686 63 Troubleshoot ...
Page 64: ...RCT150A Operator Service Maintenance Manual 64 Troubleshoot ...
Page 65: ...RCT150A Operator Service Maintenance Manual 800 392 2686 65 Troubleshoot ...
Page 66: ...RCT150A Operator Service Maintenance Manual 66 Troubleshoot ...
Page 67: ...RCT150A Operator Service Maintenance Manual 800 392 2686 67 Troubleshoot ...
Page 68: ...RCT150A Operator Service Maintenance Manual 68 Troubleshoot ...
Page 69: ...RCT150A Operator Service Maintenance Manual 800 392 2686 69 Troubleshoot ...
Page 70: ...RCT150A Operator Service Maintenance Manual 70 Troubleshoot ...
Page 71: ...RCT150A Operator Service Maintenance Manual 800 392 2686 71 Troubleshoot ...
Page 72: ...RCT150A Operator Service Maintenance Manual 72 Troubleshoot ...
Page 73: ...RCT150A Operator Service Maintenance Manual 800 392 2686 73 Troubleshoot ...