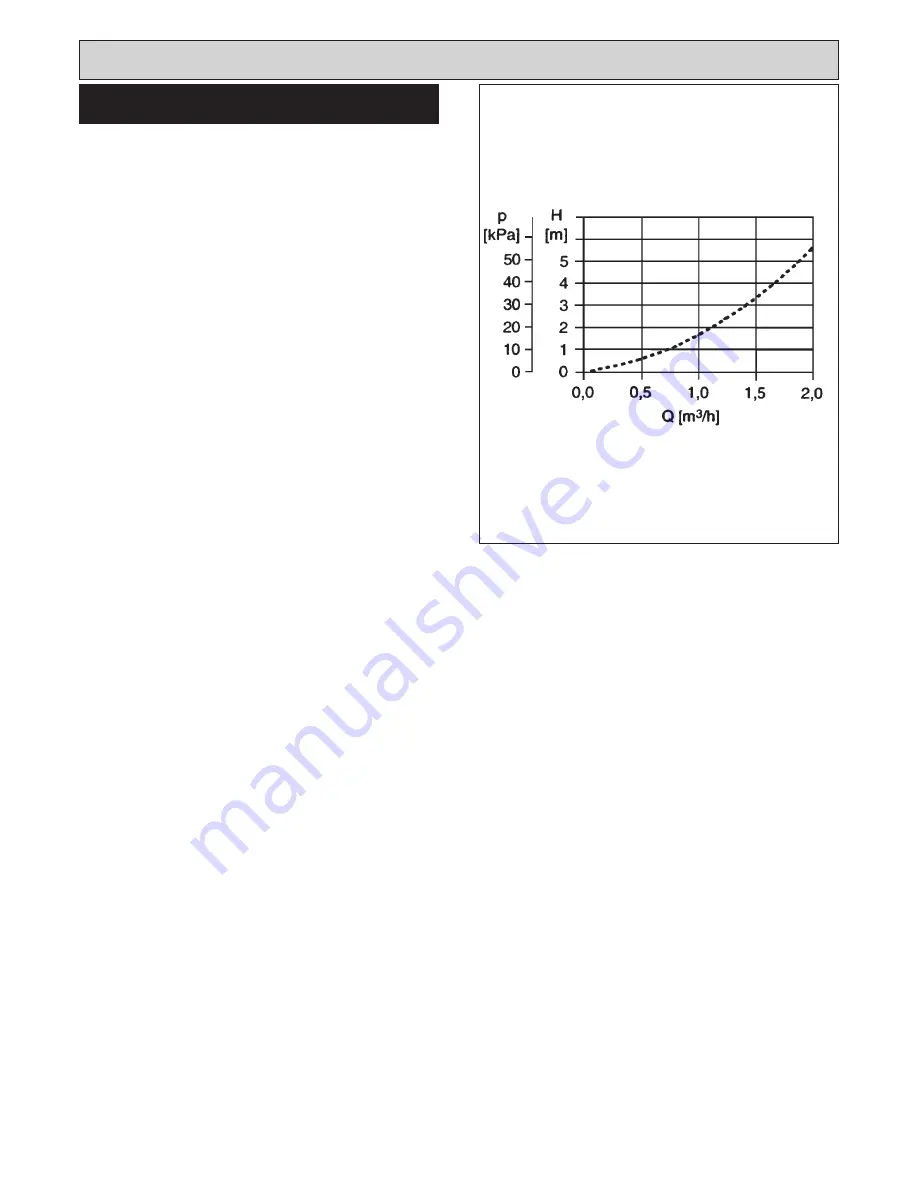
Site Requirements
9
Space and water heating systems should be in accordance
with the relevant recommendations of BS 5410: Part 1.
In a combined central heating and domestic hot water
system, the hot water storage vessel must be of the
indirect cylinder type to BS 1566: Part 1. The hot water
storage vessel should be insulated with not less than
75mm thick mineral fibre or its equivalent.
Cisterns and pipework should not be situated in areas
which may be exposed by freezing conditions and should
be insulated.
Draining taps must be located in accessible positions
which permit the draining of the whole system, including
the heat storage vessel. Draining taps should be at least
1/2 in BSP nominal size and be in accordance with BS
2879.
The appliance boiler section should be connected to
cistern water supply, subject to a maximum head of 3 bar
(30m), minimum of .1 bar (1m).
The heating system must be designed (and adjusted if
necessary) to give temperature differential across the
boiler at full output of 10-14°C. Where horizontal runs are
used the pipes should rise upwards in the direction away
from the appliance.
Circulating Pump
It is recommended that the selected pump be sized to suit
the boiler pressure loss and therefore adequate to give
the required temperature differential between the flow and
return. (See Fig. 4).
The pump should be able to meet the requirements of the
system design and fit in a readily accessible position.
Isolating Valves
Isolating valves (preferably of the keyless type) must
be fitted to the inlet and outlet of the circulating pump
to facilitate service and replacement of pump without
draining the system.
Inhibitor
A corrosion inhibitor
MUST
be added to the heating
system to protect the heat exchanger and pipework.
Inhibitor must also be replaced if the system is drained
after installation. As a precaution the heating system
MUST
also be flushed out prior to the addition of the
inhibitor to ensure any flux, debris is removed.
Sealed System Requirements
See Pages 18 and 19.
WATER CIRCULATION SYSTEM
Fig. 4
Pressure Loss Curve
Summary of Contents for Heatranger 480CD
Page 13: ...Installation Instructions 13 Fig 9 ...
Page 18: ...Sealed System Fig 19 18 ...
Page 21: ...21 ...
Page 22: ...22 ...
Page 23: ...23 ...