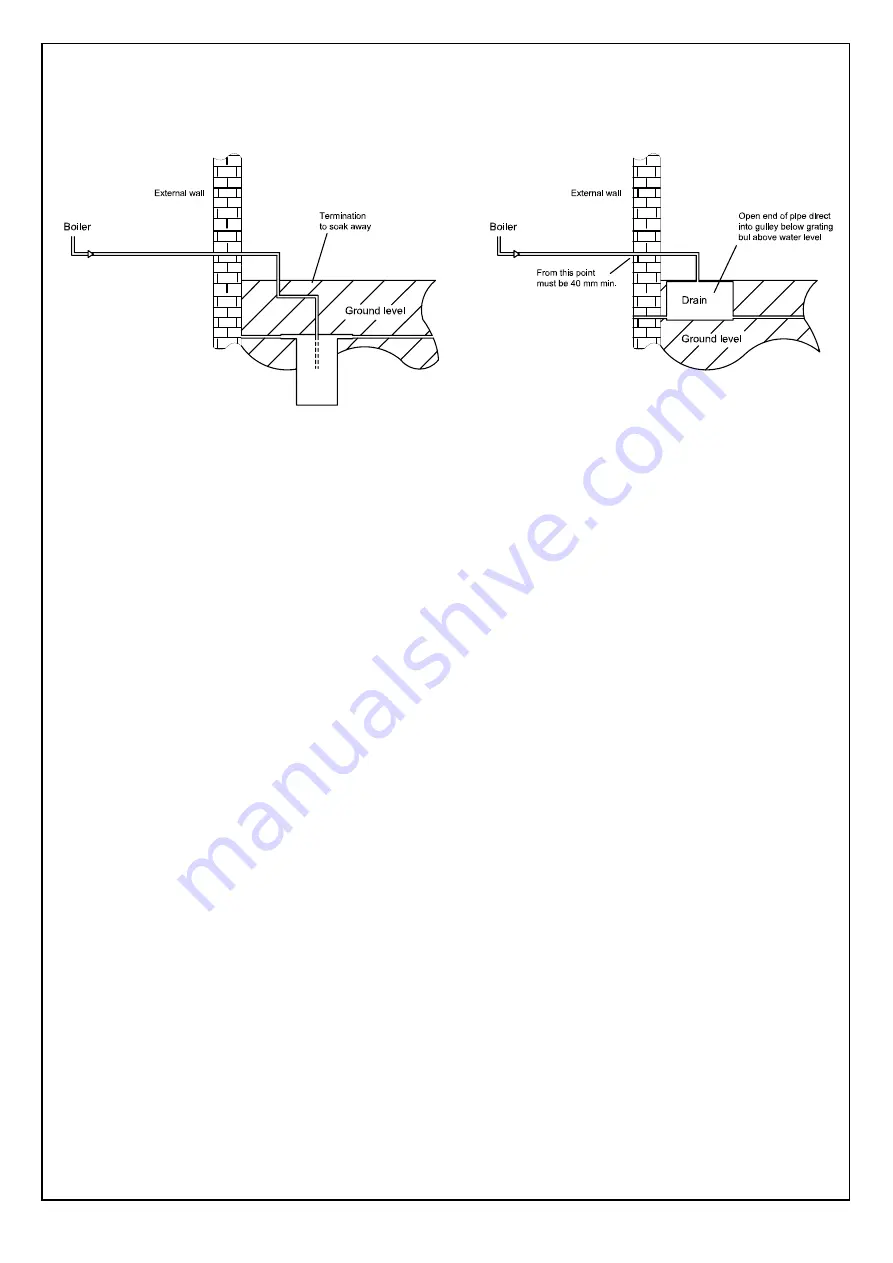
39
3 - TERMINATION TO SOAK AWAY 4 - TERMINATION TO DRAIN / GULLY
5.27
CONVERTING THE APPLIANCE
TO DIFFERENT GAS TYPES
Boilers are factory set to work for use
with Natural gas or LPG gas. This is
clearly marked on the packaging and
boiler data badge.
To convert a boiler from one gas to
another this operation must be carried
out by a qualified competent person,
with all necessary equipment
authorised by th
authorised by the manufacturer.
It will also be necessary to obtain a data badge
conversion kit directly from The White Boiler
Company.
1 - Remove the case.
2 - Check gas mains pressure at the gas
valve test nipple upstream (fig.35)
with boiler operating (sect.6.8).
3 - Adjust fan speed as sect.3
(technical data).
4 - Measure the level of CO2 as in section
as in section
6.9 and table 10, and adjust to correct
6.9 and table 10, and adjust to correct
data settings information.
data settings information.
5 - Affix new data badge.
6 - Replace in reverse order.
5.28 ELECTRICAL
CONNECTIONS
IMPORTANT:
Electricity supply must be as specified in
clause (sect. 4.22).
- When controls external to the appliance are
required, design of the external electrical
circuits should be undertaken by a
competent person. In accordance with the
IEE wiring regulations.
It is essential that all external controls
are VOLT FREE.
Factory fitted internal wiring must not be
disturbed when wiring external controls.
- To gain access to the electrical box remove
the front panel of the case as described in
clauses sect. 8.2.
8.2.
You can slide towards the top the
You can slide towards the top the
instrument panel box and push the retaining
instrument panel box and push the retaining
latches and remove the instrument panel
latches and remove the instrument panel
(sect. 8.24).
(sect. 8.24).
- Heat resistant flexible cable is fitted
- Heat resistant flexible cable is fitted
between the isolator and the terminal block
between the isolator and the terminal block
which is a 3 core cable
which is a 3 core cable of 0.75 mm
2
(24x0,2
mm) to BS 6500.
Make sure all wires to the appliance are
routed away from sharp edges and hot
surfaces.
The cable must be fastened with its cord
anchorage and connected so that should
the cable slip from the anchorage the
current carrying conductors become taut
before the earthing conductor. Securely
tighten all terminal screws and arrange
the cable with slack between the cord
anchorage and the terminal block.
WARNING:
If the supply cord is damaged, it must be
replaced by a service engineer (supply
cord available from The White Boiler
Company).
5.29 OUTDOOR SENSOR
For use, consult Outdoor Sensor
instructions.
Fig. 33
Fig. 34
Summary of Contents for White Boiler WH 80
Page 2: ...2 ...
Page 21: ...21 4 10 FLUE TERMINAL POSITION ...
Page 54: ...10 ELECTRICAL SYSTEM DIAGRAM 54 Fig 61 ...
Page 55: ...55 11 SPARE PARTS Fig 62 ...
Page 59: ......
Page 62: ...61 ...
Page 63: ...62 ...
Page 65: ...64 FLOWCHART FOR CO LEVEL AND COMBUSTION RATIO CHECK ON COMMISSIONING A CONDENSING BOILER ...
Page 66: ...65 12 1 ANALYSER CHECK LIST ...