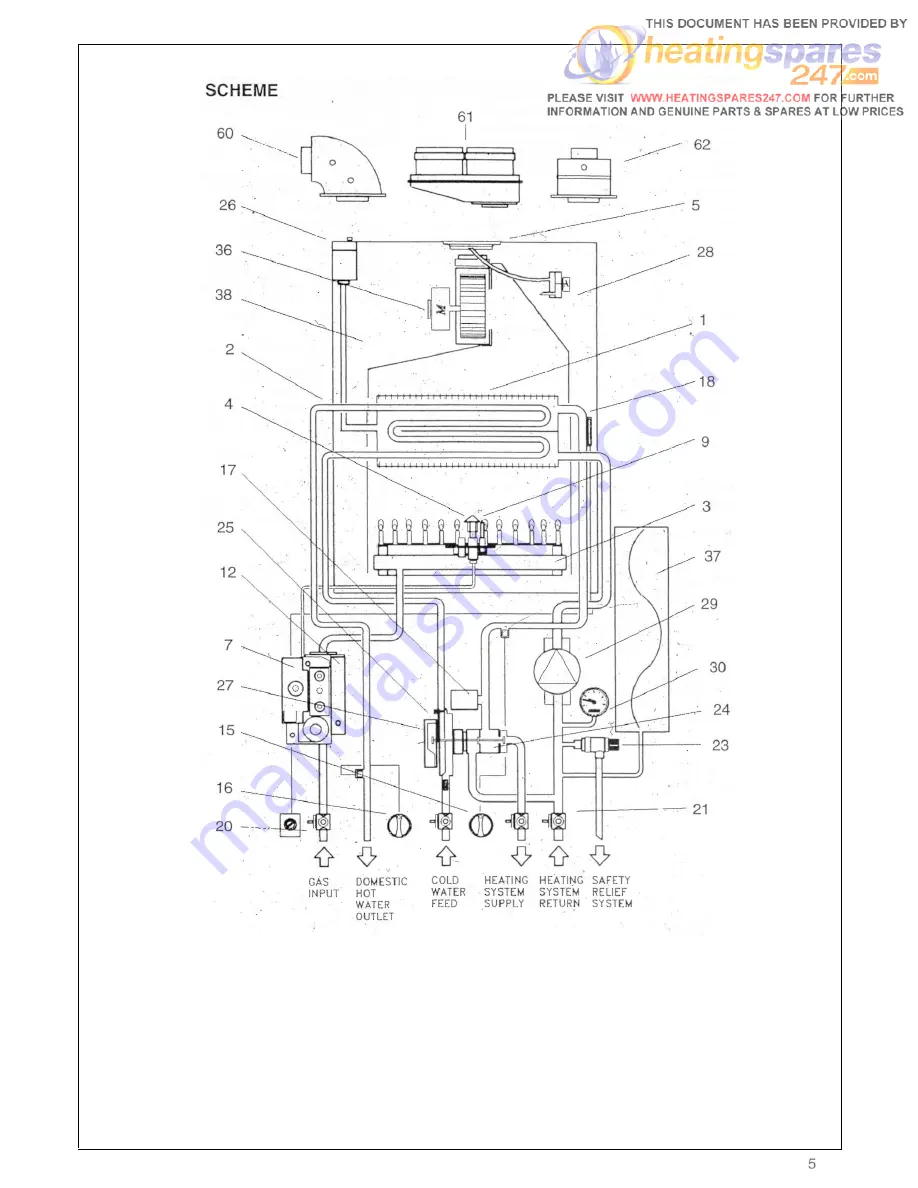
OPERATING
Fig. 2
KEY
1 - Heat exchanger
2 - Heat exchanger for D.H.W. water
3 - Burner
4 - Pilot burner
5 - Air restriction ring
7 - Electronic ignition
9 - Ignition electrode
12 - Modulating gas valve
15 - Heating control
16 - Hot water control
17 - Low water pressure switch
18 - Overheat cut-off thermostat
20 - Gas service cock
21 - Compression ball valves
23 - Safety relief system
24 - Three way valve
25 - Flow regulator
26 - Auto air vent valve
27 - D.H.W. pressure switch giving priority
28 - Air pressure switch
29 - Circulating pump
30 - Water pressure gauge
36 - Fan
37 - Expansion tank
38 - Sealed chamber
60 - Elbow header
61 - Twin header
62 - Straight header
Summary of Contents for RSF 84E
Page 42: ......
Page 45: ...SECTION 9 ELECTRICAL SYSTEM DIAGRAM Fig 94 46...
Page 46: ...47...
Page 47: ...48...
Page 48: ......
Page 52: ...SECTION 11 EXPLODED PARTS DIAGRAM...
Page 55: ...Chartists Way Morley Leeds LS27 9ET Telephone 0113 252 7007 Tfax 0113 238 0229...