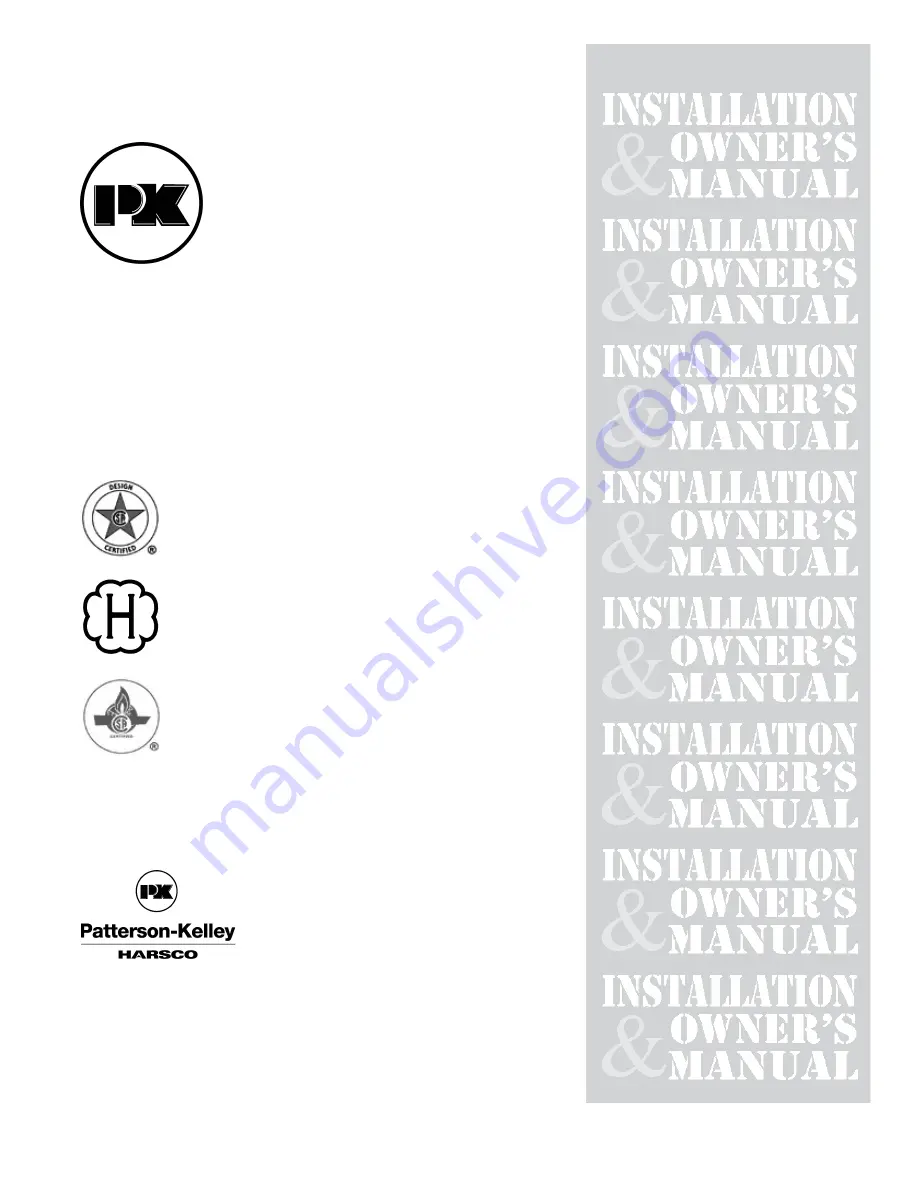
©2009 Patterson-Kelley, A Harsco Company
PATTERSON-KELLEY
MACH
®
C2500
GAS-FIRED BOILER
Model #:_______ Serial #______________________
Start-Up Date:
_______________________
100 Burson Street, P.O. Box 458,
East Stroudsburg, PA 18301
Telephone: (877) 728-5351,
Facsimile: (570) 476-7247
www.pkboilers.com
XLMACH- 09
C.S.A Design-Certified
Complies with ANSI Z21.13/CSA 4.9
Gas-Fired Low Pressure Steam and Hot Water
Boilers
ASME Code, Section IV
Certified by Patterson-Kelley
C.S.A Design-Certified
Complies with ANSI Z21.13/CSA 4.9
Gas-Fired Low Pressure Steam and Hot Water
Boilers