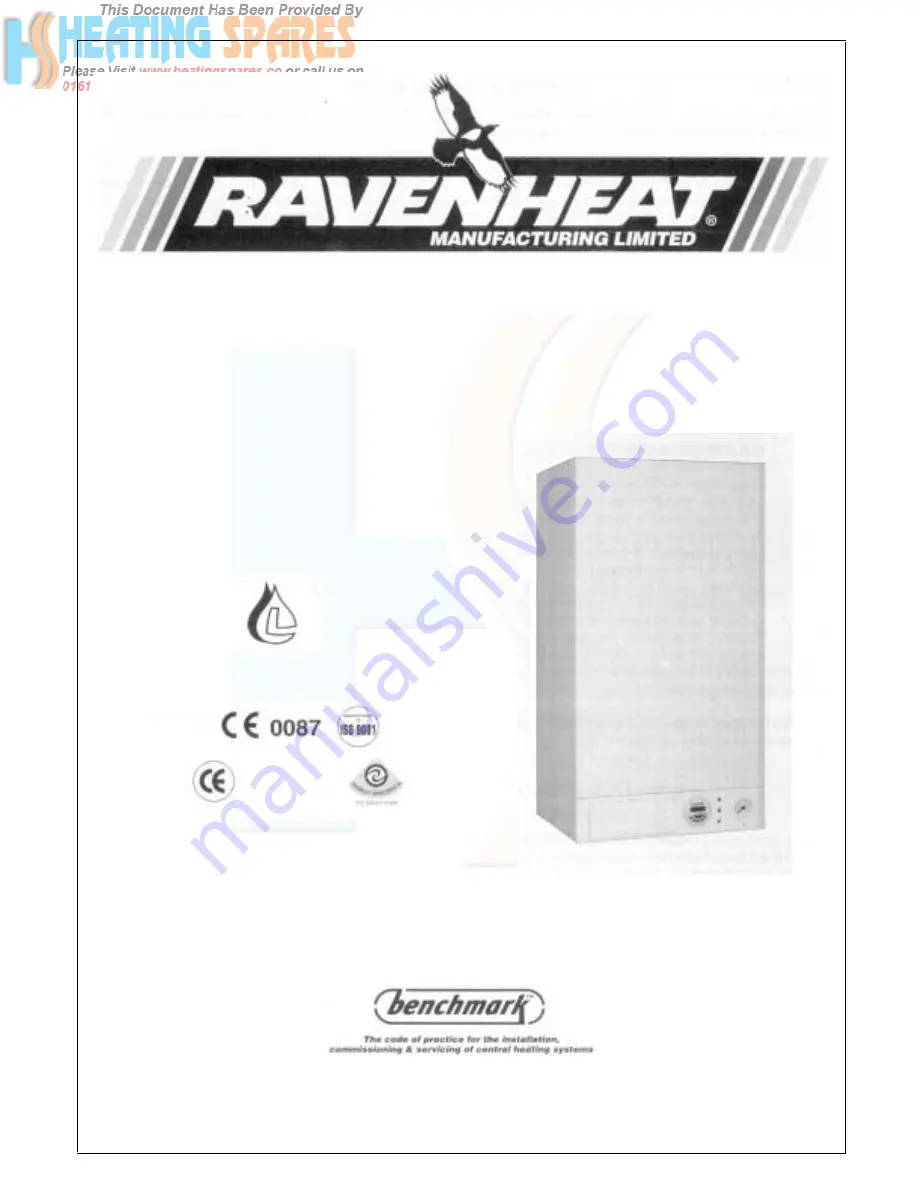
Supplied By www.heating spares.co Tel. 0161 620 6677
CONDENSING
FANNED FLUE BOILER
CSI SYSTEM
WITHOUT TIMER
NATURAL GAS (G20) (I
2H
) G.C.N
o
47 581 01 - CSI
LPG (G30-G31) (I
3+
) G.C.N
o
47 581 03 - CSI
Tested, certified and
service listed
Listed by The United Kingdom Water
Fitting Byelaws Scheme
WITH TIMER
NATURAL GAS (G 20) (I
2H
) G.C. N
O
47 581 02 - CSI
LPG (G 30 - G 31) (I
3+
) G.C.N
O
47 581 04 - CSI
INSTALLATION AND SERVICING INSTRUCTIONS
TO BE LEFT WITH USER
Technical and illustrative data are not binding and can be modified without prior notice.
The descriptions and illustrations in the present booklet are for guideline purposes only.
RAVENHEAT MANUFACTURING LTD., CHARTISTS WAY, MORLEY, LEEDS, LS27 9ET. -TELEPHONE (0113) 252 7007
Summary of Contents for Flue Boiler
Page 16: ...Supplied By www heating spares co Tel 0161 620 6677 ...
Page 26: ...Supplied By www heating spares co Tel 0161 620 6677 2 6 ...
Page 41: ...Supplied By www heating spares co Tel 0161 620 6677 Fig 90 Fig 91 Fig 93 41 ...
Page 45: ...Supplied By www heating spares co Tel 0161 620 6677 ...
Page 49: ...Supplied By www heating spares co Tel 0161 620 6677 ...