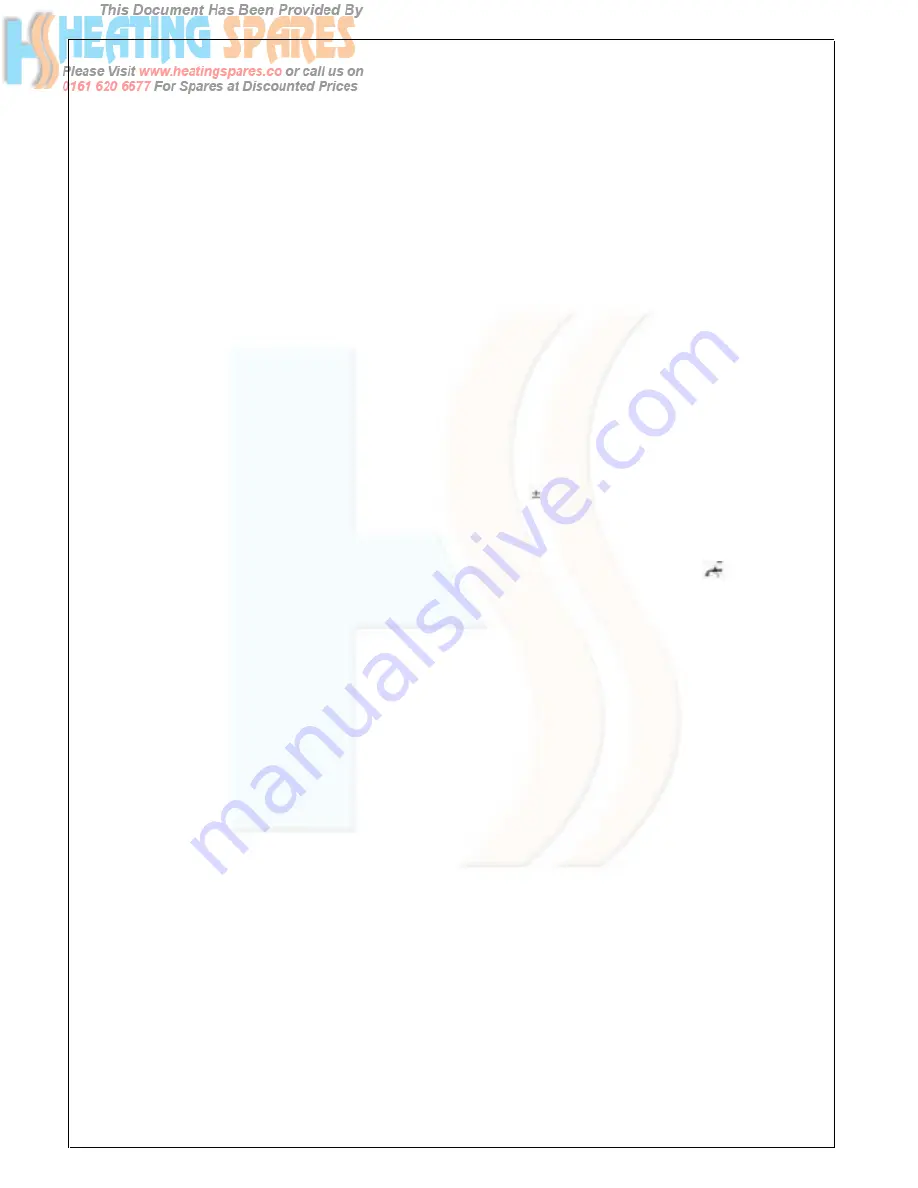
Supplied By www.heating spares.co Tel. 0161 620 6677
SECTION
6 COMMISSIONING
6.1
6.2
6.2.1
6.3
6.4
6.5
6.7
Each boiler has been through a rigorous
operational procedure at our factory and
should not require any further adjustment.
If in the unlikely event of the appliance not
operating correctly, please turn to the Fault
Finding and Logic Sequence charts.
GAS SUPPLY INSTALLATION
Inspect the entire installation including the
gas meter, test for soundness and purge,
all as described in BS 6891.
ELECTRICAL INSTALLATION
Preliminary electrical systems checks to
ensure electrical safety shall be carried out
by a competent person (earth continuity,
polarity, resistance to earth). Those checks
are outlined in the <<lnstructions for British
Gas Multimeter>> Booklet. If a fault has
occurred on the appliance the fault finding
procedure should be followed as specified
under the servicing section of this document.
INITIAL FILLING OF THE SYSTEM
Open central heating flow and return
valves.
Unscrew the cap on automatic air release
valve one full turn (leave open permanently).
- Close all air release taps on the central
heating system.
- Gradually open stopcock at the filling
point connection to the central heating
system until water is heard to flow.
- Starting with the lowest radiator open
each air release tap in turn. Close it only
when clear water, free of bubbles, flows
out. In the same way release air from
any high points in the pipework.
- Continue filling the syStem until 1.5 bar
registers on gauge. Then turn off the fil-
ling points stopcock.
- Inspect the system for water soundness
and remedy any leaks discovered.
SETTlNG THE SYSTEM DESIGN
PRESSURE
The design pressure must be a min. 1 bar
and max. 1.5 bar. These figures are read off
the pressure gauge.
- The actual reading should ideally be 1
bar + the height in metres to the highest
point of the system above the base of
the appliance (up to a max of 1,5 bar).
N.B.: The safety valve is set to lift a 3
bars (30 mt/42.5 psig).
- To lower the system pressure to the
required value remove drain point (Fig.
93) or drain on the heating circuit.
LIGHTING THE BOILER (Fig. 50)
Before lighting the main burner make sure
that the heating circuit flow and return val-
ves are open.
- If external controls are installed (e.g.
timeclock and thermostat) make sure
that they call for heat.
- Turn on main switch 1 (Fig. 50).
- Turn control thermostat 4 up to its maxi-
mum setting.
-
Now the main burner should turn on.
With leak detection fluid test for gas sound-
ness of all gas components and joints.
- See paragraph 6.14 for regulating the
heating circuit thermostat.
Check gas mains pressure (Fig. 52). Fit
a gas pressure gauge on pressure inlet
77 (Fig. 51) on the gas valve, after
releasing the seal screw.
Check the gas mains pressure with boil-
er operating.
Check with the Local Gas supplier if the
pressure differs significantly from 20
mbar (natural gas), 37 mbar (G 31) and
29 mbar (G 30).
6.9
CHECK THE GAS PRESSURE AT THE
BURNER
Now check if the maximum gas pressure at
the burner is equal to 10.5 + 0.5 mbar (4.2
0.2 in wg.) for CSI 85 CSI 85T.
- LPG check gas pressure inlet (37 mbar
propane - 29 mbar butane).
To do this proceed as follows:
- Turn off main switch 1 (Fig. 50)
-Set main switch 1 on
- S e t c o n t r o l t h e r m o s t a t 5 a t i t s
maximum setting.
-Fit a pressure gauge, using a hose, to
pressure test point 81, (Fig. 51), after
first loosening its close-off screw.
-Open one or more hot water taps so
that at least 10 -12 litre of water flows
per minute.
- The pressure indicated on the pressure
gauge is the maximum operating gas
pressure.
- Check that the minimum pressure
corresponds to 2 mbar (0.8 in wg.) for
G 20 as is set at the factory.
-
LPG 7.3 mbar for G 31 and 7.0 mbar for
G 30. This is set and sealed at the
factory and cannot be adjusted.
Detach one of the wires going to
modulator 104 (Fig. 51) and make the
boiler operate just as was done for
checking the maximum pressure.
Observe the pilot flame which will light a
second before main burner. It should be
about 20 mm long (Fig. 528) and envelop
the spark electrode tip.
6.10
ADJUSTING MINIMUM AND MAXIMUM
PRESSURE (Fig. 51) SIT-HONEYWELL
GAS VALVE
- Remove cap covering modulator to gas
valve.
- Detach one of the cables connected to
the modulator 114.
27
Summary of Contents for Flue Boiler
Page 16: ...Supplied By www heating spares co Tel 0161 620 6677 ...
Page 26: ...Supplied By www heating spares co Tel 0161 620 6677 2 6 ...
Page 41: ...Supplied By www heating spares co Tel 0161 620 6677 Fig 90 Fig 91 Fig 93 41 ...
Page 45: ...Supplied By www heating spares co Tel 0161 620 6677 ...
Page 49: ...Supplied By www heating spares co Tel 0161 620 6677 ...