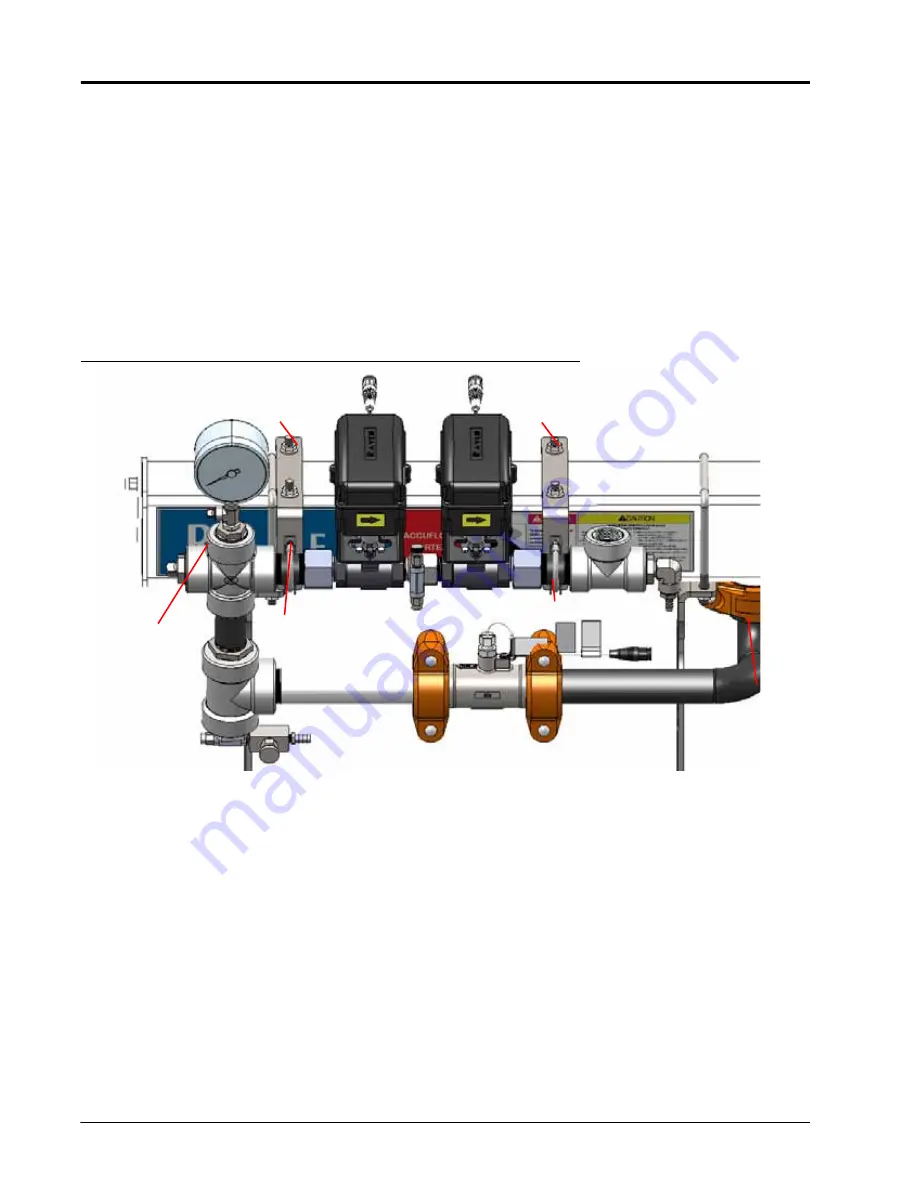
CHAPTER 3
26
AccuFlow™ Vortex and AccuFlow™ HP+ Installation and Operation Manual
15. Install the tee, bleed valve, and check valve into the relief valve adapter.
16. Install the on/off valve onto the 1” close nipple.
17. Install pipe adapter into the other end of the on/off valve.
18. Thread the 1” x 3” long pipe nipple into a pipe adapter.
19. Thread the other end of the pipe nipple into a 1-1/4” tee.
20.Install 1-1/4” x 1/2” reducer into the other end of the 1-1/4” tee.
21. Install an elbow into the 1-1/4 x 1/2” reducer.
22.Install the hose barb fitting into elbow.
ATTACHING THE GAUGE TREE TO THE COOLER
FIGURE 12. Attaching the Gauge Tree to the Cooler
1. Place the cooler mounting bracket on top of the cooler.
2. Use the provided large u-bolts to secure the mounting bracket to the cooler.
3. Place the clamping u-bolts over the horizontal pipe nipples on the assembly.
4. Feed the ends of the clamping u-bolts into the side of the mounting brackets.
5. Install the nuts on the end of the clamping u-bolts.
6. Slide the coupling gasket over the end of the gauge tree that attaches to the flowmeter.
7. Connect the end of the gauge tree to the end of the flowmeter.
8. Use the provided coupling clamp, 1/2” bolts, and 1/2” nuts to secure the gauge tree to the outlet manifold.
9. Tighten the 1/2” nuts to 80 to 100 ft-lbs.
Clamping U-Bolts
Cooler
Mounting
Bracket
Gauge Tree
Cooler
Cooler
Mounting
Bracket
Clamping U-Bolts
Summary of Contents for AccuFlow HP+
Page 20: ...CHAPTER 2 16 AccuFlow Vortex and AccuFlow HP Installation and Operation Manual ...
Page 46: ...CHAPTER 3 42 AccuFlow Vortex and AccuFlow HP Installation and Operation Manual ...
Page 54: ...CHAPTER 4 50 AccuFlow Vortex and AccuFlow HP Installation and Operation Manual ...
Page 64: ...CHAPTER 5 60 AccuFlow Vortex and AccuFlow HP Installation and Operation Manual ...
Page 74: ...CHAPTER 6 70 AccuFlow Vortex and AccuFlow HP Installation and Operation Manual ...
Page 94: ...CHAPTER 8 90 AccuFlow Vortex and AccuFlow HP Installation and Operation Manual ...