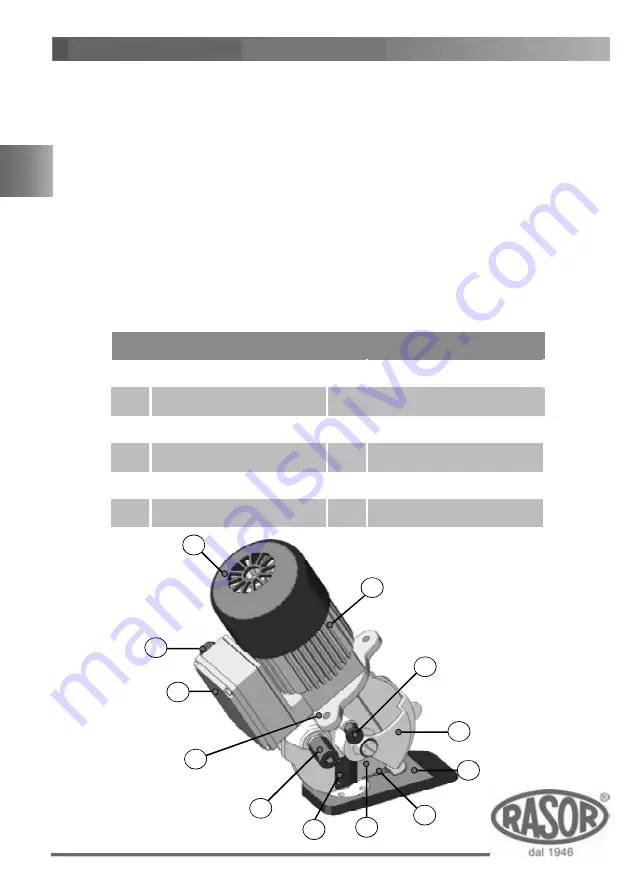
EN
4. PRODUCT DESCRIPTION
The fixture described in this manual is a cutting unit model GRT10 which can be assembled
on automatic machines (e.g. spreaders, computerized cutting) by means of proper holes
located in the motor support.
GRT10 can operate continuously and it can cut at various heights by means of multiple
installation.
By cutting with the blade and the counterblade always in contact and thanks to the steel
upper quality of the blade supplied, GRT10 guarantees the clean separation without frayings
of the two borders of the cut material. The three-phase motor with extremely compact
dimensions and extreme reliability with 100 mm diameter blades, guarantees cuts with
thickness up to 3.5 cm. A sharpener assembled on the cutting unit head allows whetting
the blade at any moment without disassembling it. After carrying out this operation, it is
possible to start cutting again. A high power motor, perfectly balanced, with a high number
of revolutions and totally free of maintenance, reduces the vibrations to the minimum, thus
making the cutting unit complies with European Directive No. 2002/44/EC concerning the
risks deriving from mechanical vibrations.The mechanical parts are made of high resistance steel,
bronze and aluminium and require lubrication after several working hours.
1
2
3
4
10
6
7
8
9
5
11
12
1
Connector block
7
Aluminium base
2
Motor cover
8
Poligonal blade
3
Cable gland
9
Spring locking the thread
4
Motor frame
10
Greaser
5
Sharpening button
11
Hard metal counterblade
6
Movable front protection
12
Motor flange with assembly
holes
Device components
22
Enfocus Software - Customer Support