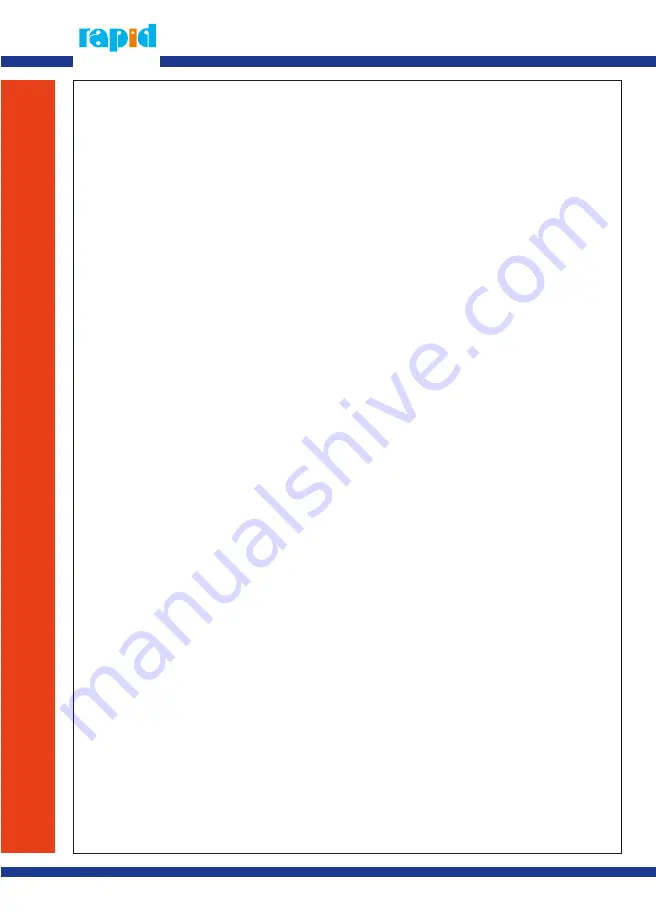
7. Operation
7.1
Pressure relieve
7.1.1
Skin injection hazard: The equipment stays pressurized until pressure is
manually relieved. To reduce the risk of serious injury from pressurized fluid, fluid
from the valve or splashing fluid, follow this procedure whenever you:
7.1.1.1 Are instructed to relive pressure
7.1.1.2 Stop dispensing
7.1.1.3 Check, clean or service any system equipment.
7.1.1.4 Install or clean dispensing devices.
7.1.2 Pressure relieve procedure
7.1.2.1 Close the pump air regulator and the bleed-type master air valve.
7.1.2.2 Hold a metal part of the dispensing valve firmly to a grounded metal wast
container and trigger the valve to relieve the fluid pressure.
7.1.2.3 Open the air line valve and grease valve.
7.1.2.4 Close the control valve.
7.1.2.3 When occurs:
1) Problems on control valve, flexible hose, rigid tube or manual tip, autotip
2) Pressure relieved very slowly until relieved throughly. Please clear obstruction
of grease system.
7.2
Procedure
7.2.1
Note: When the pump is primed and with sufficient air supplied, the pump starts
when the dispensing valve is opened and shuts off when it is closed.
7.2.2
Warning: The maximum working pressure of each component in the system may
not be the same. To reduce the risk over pressurizing any component in the
system, be sure you know the maximum working pressure of each component.
Never exceed the maximum working pressure of the lowest rated component in
the system. Over pressurizing any component can result in rupture, fire,
explosion, property damage and serious injury. The maximum pressure in the
system is equal to air input pressure times pump ratio. Regulate air to the pump
so that air line or fluid line component or accessory is not over pressurized.
7.2.3
Caution: Never allow the pump to run dry of the material being pumped. A dry
pump will quickly accelerate to a high speed, possibly damaging itself. If your
pump accelerates quickly or is running too fast, stop it immediately and check
the material supply. If the supply container is empty and air has been pumped
into the lines, prime the pump an lines with material, or flush it and leave it filled
with a comatible solvent. Be sure to eliminate all air from the material lines.
7.2.4 Startup
7.2.4.1 If there are multiple pumps on the air line, close the air regulators and bleed-type
master air valves to all but one pump.
7.2.4.2 Open the master air valve from the compressor.
7.2.4.3 Open the dispensing valve into a grounded metal waste container, making firm
metal-to-metal contact between the container and valve. Open the bleed-type
master air valve and open the pump air regulator slowly, just until the pump is
running. When the pump is primed and all air has been pushed out of the lines,
close the dispense valve.
7.2.4.4 If you have moren than one pump, repeat this procedure for each pump.
8
+49 (6158) 92980-0