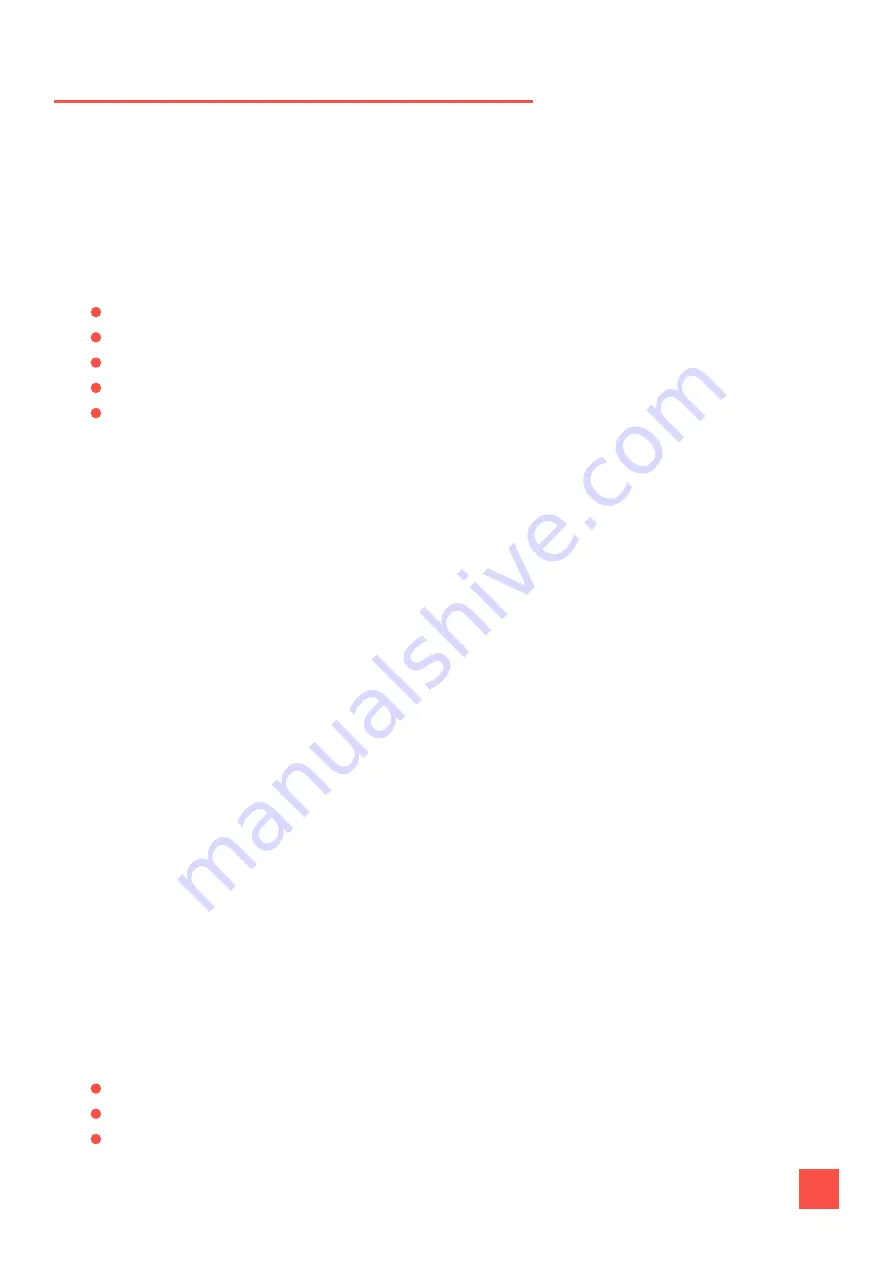
20
Scanning
Requirements for the scanned object
The scanner analyses structured light reflected from the surface of the object,
therefore, scanning should be carried out in premises without direct sunlight, as well as
free of dust and vibration. For the same reason scanning of the following objects is not
possible or is too difficult:
too dark and black objects
transparent objects
mirrors
flecking and glossy objects
fur
To work with such objects it is recommended to process them with special aerosol
products prior scanning, which leave a very thin coat of white powder on the object
after drying. HELLING Developer solution U89, Sherwin D-100.
There are also some difficulties when you are scanning objects with sharp edges,
deep grooves or holes, thin wall objects. Objects that contain large contrast areas (for
example, black lettering on white paper) can also cause problems. Geometrical
distortion may appear in places with strong contrast.
Scanning principle and methods
If you're shooting a single fragment (scan) - you get a three-dimensional model of
the object surface. To create a full object model you need to obtain surfaces of the
object, that together entirety replicate the form of the object, i.e. scan the object from
different angles.
Obtained fragments are combined in the special software by the surface geometry,
hence there is another requirement - the object must be rigid and do not change its
shape during the entire scanning procedure. Otherwise, the geometry of the same area
of the object surface of different scans may be different, and it will be impossible to
unite the pieces into a coherent whole.
In RangeVision 3D scanner there are 3 scan options available, which are different, in
the first place, by the fragment alignment method:
Scanning without markers
Scanning with markers (marks)
Scanning on the turn table (optional, not included in the standard kit)