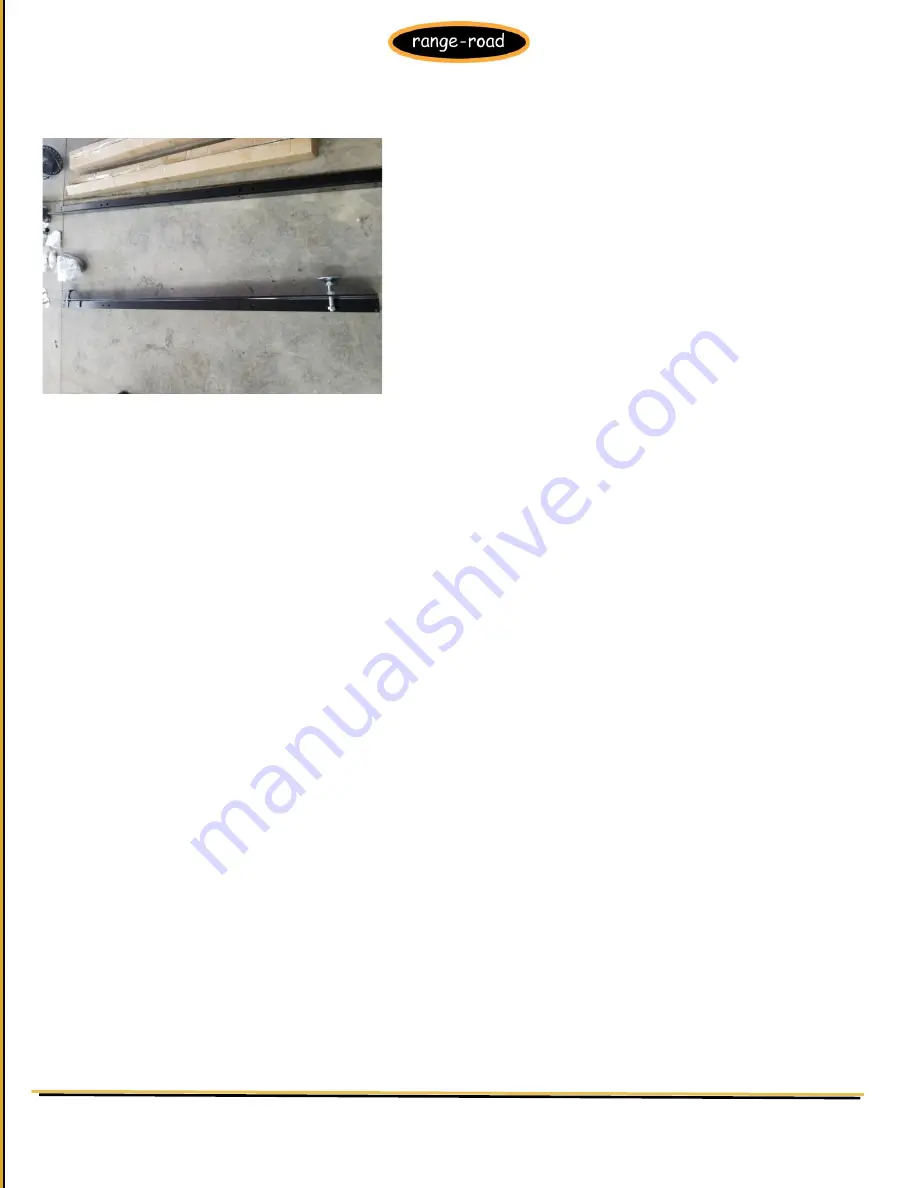
Range Road Enterprises Ltd
Box 944
Eckville AB T0M 0X0
www.range-road.ca
3) Place 2 guide rails on the floor and install 2 or 3 levelling feet in the large round holes on the bottom of each rail
4) Place the 2 rails on their levelling feet parallel to each other,
the measurement from center to center will be roughly:
-
RR5022 & RR5026 845mm (33 3/8
”)
-
RR5029 902mm
(35 ½”)
-
RR5032
1008mm (39 11/16”)
-
RR5036A 1099mm (43 ¼”)
Alternatively: assemble track without setting width, then:
1) You can assemble the sawmill head assembly, them measure the distance between the left and
right rollers on the sawmill head, that will give you the width that you need for setting the track
width. OR
2) You can assemble the sawmill head assembly, and loosely assemble the track, then set your
assembled head onto the loose track, the track will automatically move out to the proper width,
then run the sawmill head slowly down and up the track to set the width along the entire length of
the track.
Any of the above procedures will be suitable for setting the track width.
For any Sawmill to cut square and straight all pieces have to be squared to each other
and level. Use the adjusting feet to level one rail and then make sure the second rail is
level with the first one.
Summary of Contents for RR5029
Page 33: ...Range Road Enterprises Ltd Box 944 Eckville AB T0M 0X0 www range road ca Parts List...
Page 34: ...Range Road Enterprises Ltd Box 944 Eckville AB T0M 0X0 www range road ca...
Page 35: ...Range Road Enterprises Ltd Box 944 Eckville AB T0M 0X0 www range road ca...
Page 36: ...Range Road Enterprises Ltd Box 944 Eckville AB T0M 0X0 www range road ca...
Page 37: ...Range Road Enterprises Ltd Box 944 Eckville AB T0M 0X0 www range road ca...