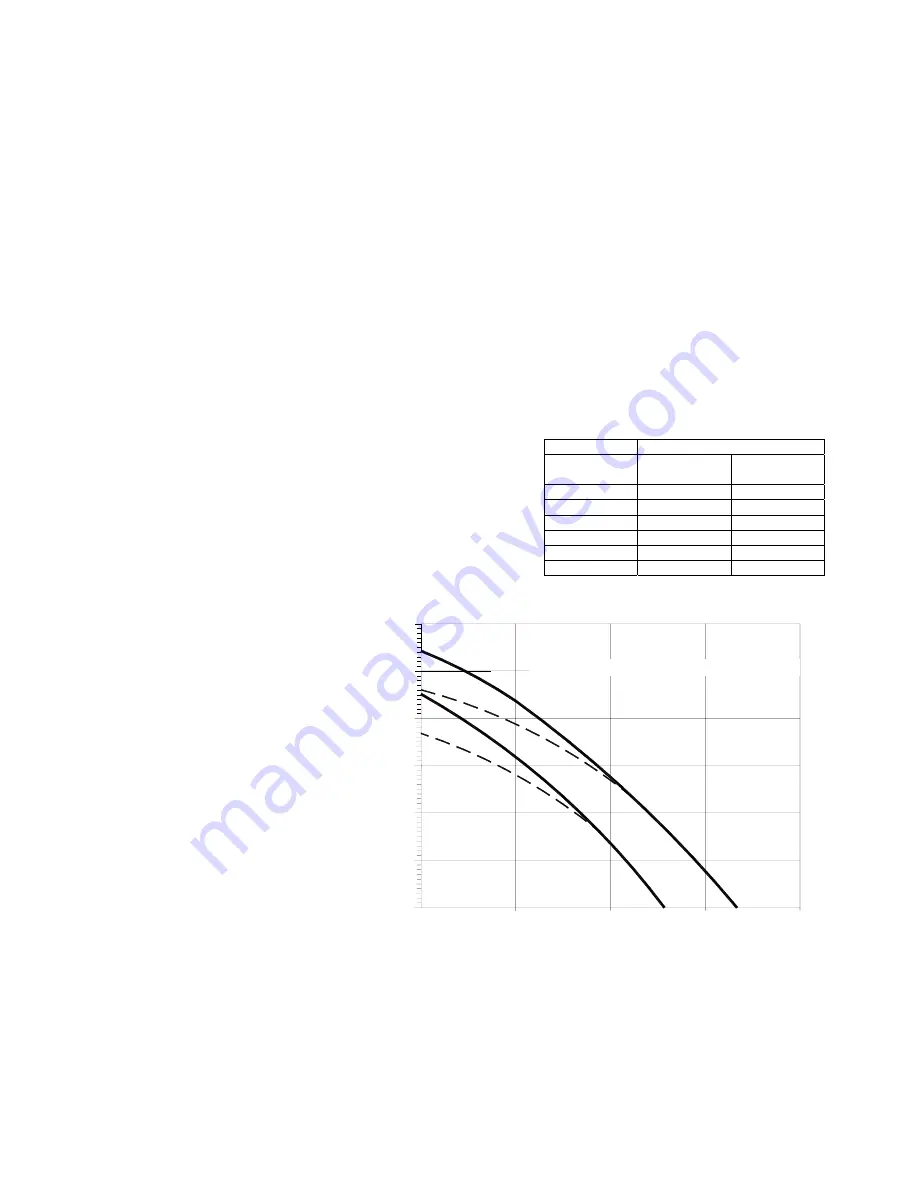
Installation Manual
COMBI - TA05A005.C0604
9
0
H
ead: m.c
.w.
Flow rete: lt/h
0
500
1000
1500
1
2
II
III
2000
3
4
6
5
GAS CONNECTIONS
The gas supply must be connected up by a corgi registered fitter.
The following standards must be complied with: UNICIG 7131/72 and UNICIG 7129/92 (of 21/04/93)
Before installing the boiler, make sure of the following:
the pipeline must be of an adequate section and length to carry the flow required and must be fitted with all safety devices and
measures prescribed by current norms;
before turning on the boiler make sure the type of gas which it is designed to run on is available;
the gas supply pressure must lie within the values shown on the boiler data plate (positioned on the inner side of front casing);
it is recommended that the gas supply pipeline should be checked for residual obstructions before installing the boiler;
where the internal gas supply pipe meets the boiler, the gas isolation cock supplied with the boiler must be fitted;
check thoroughly that the gas inlets and outlets are properly sealed.
conversion to allow the boiler to run on L.P.G. to natural gas or vice versa must be carried out by a qualified corgi registered fitter.
ANTI-FREEZE SYSTEM
The boiler is equipped with an anti-freeze system which comes into operation when the temperature falls to 5° C (heating sensor)
protecting the boiler down to an outside temperature of -2° C.
N.B: The system only comes into operation if the boiler is in the “ON” position (with MAIN SWITCH turned to SUMMER or
WINTER position) and the gas supply turned on.
FOR THE INSTALLER
For boilers installed outdoors, where the temperature may drop below -2°
degrees Centigrade, the system should be filled with antifreeze liquid by an
authorised technician and a set of electrical heating elements should be
fitted.
ADVICE FOR THE SERVICE TECHNICIAN
If the boiler is out of service because it is
frozen, check that no parts have been
locked in position by ice before putting it
into operation.
It is advisable to empty the boiler and the
system if it will not be used for a long
period.
Recommended percentage of glycol for
temperatures down to - 8°C is 20%.
The antifreeze liquid used must be of a
good make and in a solution which has
already been diluted to avoid the risk of
uncontrolled dilution.
Antifreeze Temperature
Ethylene glycol
(%) volume
freezing point
(°C)
boiling point
(°C)
10 -
4 101
20 -10 102
30 -
17 104
40 -
27 106
50 -
40 109
60 -
47 114
CIRCULATING PUMP SPECIFICATIONS