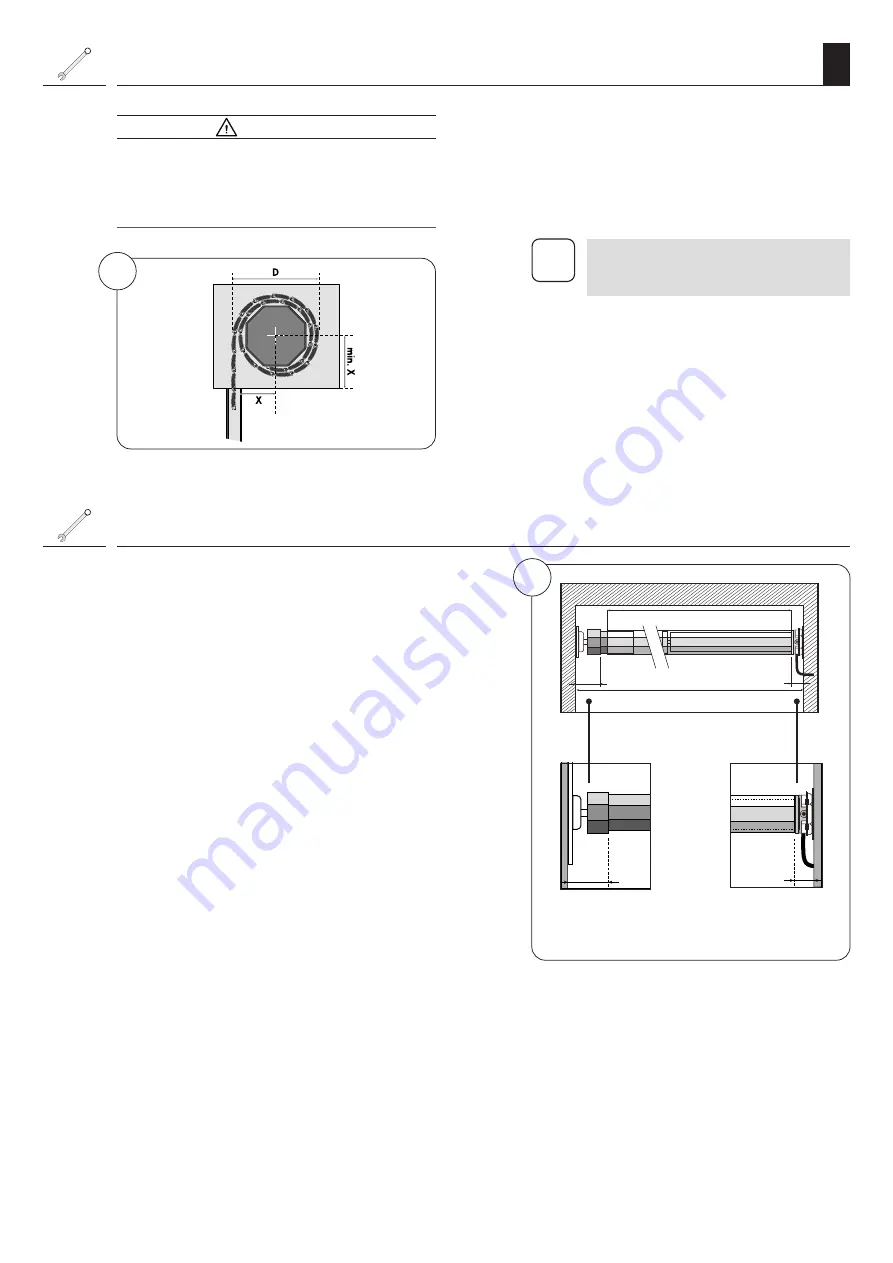
11
EN
B
C
A
L
L = A - (B + C)
4
C
B
3
= (D/2)
7.2 Mounting the bearings
ATTENTION!
A roller shutter wound at an angle can block the
drive and cause damage.
◆
Always ensure that the bearings are mounted as
horizontal as possible.
7.3 Determining the length of the winding shaft (5)
1.
Measure the wall gap of the drive
(13)
and counter
bearing
(1)
as shown.
2.
Measure the roller shutter box and calculate the
required shaft length
[ L ]
.
3.
Length of the winding shaft:
L = A - (B + C).
Recommendation
Shorten
L
by approx.
5 mm
more than calculated
by the equation to ensure a sufficiently large space
of 2 to 3 mm in the overall length when the roller
capsule
(4)
is inserted.
4.
Shorten the winding shaft
(5)
to the required size.
Cut the shaft to size with a hacksaw at a right-angle.
Remove the burrs from the shaft internally and ex-
ternally with a file.
1.
First determine the position of the drive
(13)
and
counter bearing
(1)
in the roller shutter box.
2.
Wind the roller shutter casing fully onto the winding
shaft and measure the diameter
[ D ]
. See figure
[ 3 ]
for determining the position of the centre of the
bearing to the guide rail.
i
When installed, the wound roller shutter
must run vertically in the guide rail on the
window.
3.
Fasten the bearing in accordance with the bearing
type and on-site conditions.
4.
Mount the drive bearing
(13)
so that the set button
(11)
on the drive head will be easily accessible at
a later stage and the motor cable
(15)
can be laid
without kinking.
B
= Counter bearing / roller capsule
C
= Drive bearing / motor
Summary of Contents for RolloTube CLIS
Page 27: ...27 EN ...