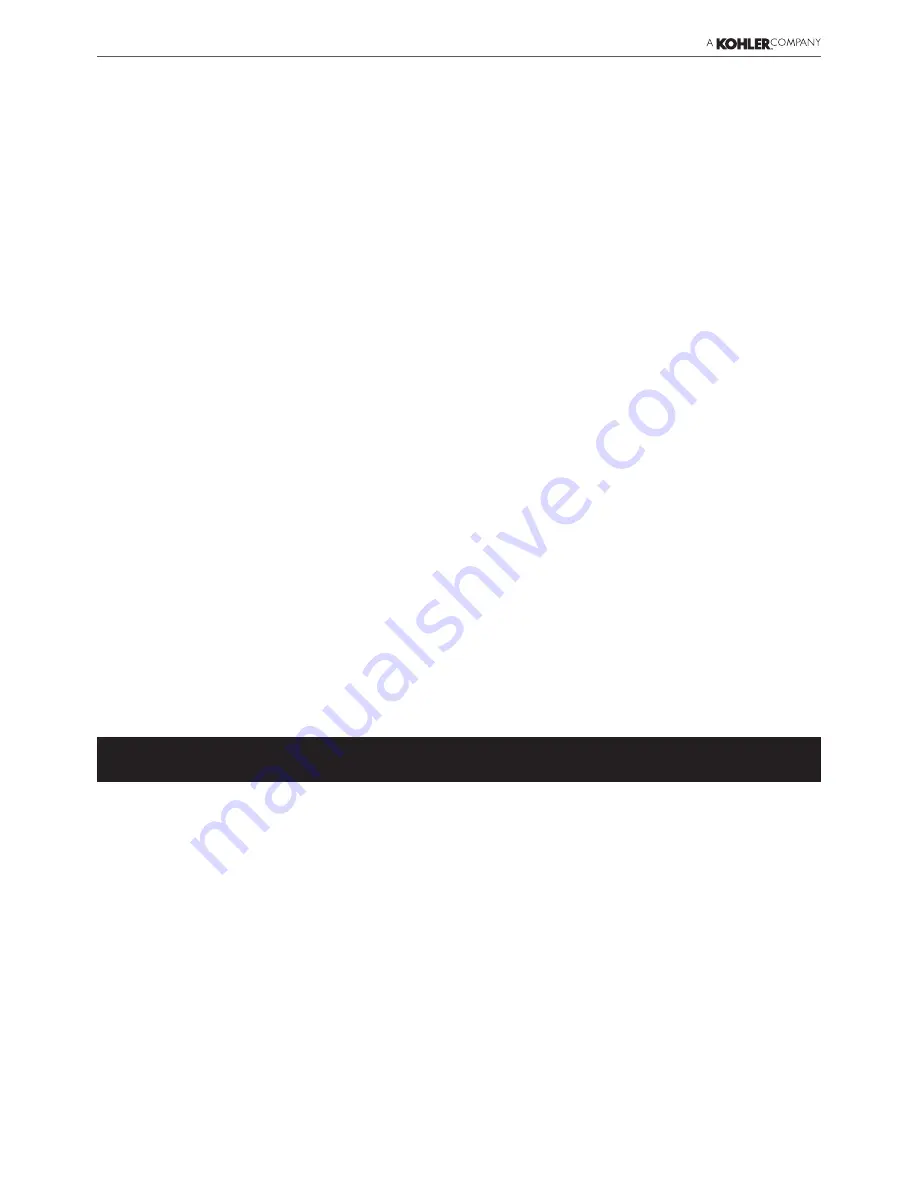
21
1300905-W2-A
Commissioning Checks
(Temperatures should always be recorded with a thermometer with proven accuracy).
1. Check inlet pipework temperatures for correct function of checkvalves i.e. that hot water
does not cross flow into the cold supply and vice versa.
2. Check that the supply pressures are within the range of operating pressures for the
valve.
3. All connections and the mixer body are water tight.
4. Exercise the thermostat.
(a) ensure that the hot and cold water are available at the valve inlets, and the outlet is
open.
(b) move the temperature control rapidly from cold to hot and hot back to cold several
times, pausing at each extreme.
5. Adjust the temperature of the mixed water in accordance with the instructions
(refer to Maximum Temperature Setting).
6. Operate the outlet flow control and check:
(a) Flow rate is sufficient for the purpose
(b) Temperature(s) obtainable are acceptable.
For models with knob fitted for adjustable temperature control, adjustment of blend temperature
from preset maximum to cold is achieved by clockwise rotation of the knob.
For models with locked temperature control, no user adjustment is intended.
Control of flow is via separate outlet valve(s), refer
Flow Control
.
It is advisable to establish a performance check at this time, which should be noted for future
reference as part of a Planned Maintenance Programme. The procedure should be chosen to
imitate both typical and difficult operating conditions, such as any supply pressure fluctuations
that may be likely. An ideal method is to locate another outlet on the common cold water
supply close to the mixing valve (operating this outlet should cause a drop in supply pressure),
and note the subsequent effect on blend temperature (should be no more than 2
o
C change).
Operation
The product is suitable for a number of bathing applications. Ultimately, the user or attendant
must ensure that the delivery of warm water is at a stable, safe temperature. This is particularly
important in healthcare procedures such as supervised bathing of patients unable to respond
immediately to unsafe temperatures.
If temperatures are found to be unstable or unsafe the product must be isolated and not used
until product maintenance checks have been carried out in accordance with the instructions
given in this manual.
Summary of Contents for 320
Page 1: ...1 1300905 W2 A 320...
Page 3: ...3 1300905 W2 A X 1 q X 1 q X 1 q X 1 q 320 IC X 3 q X 2 q X 1 q X 1 q X 2 q...
Page 4: ...4 1300905 W2 A 320 IF X 1 q X 1 q X 1 q X 1 q X 2 q X 1 q X 1 q X 2 q...
Page 5: ...5 1300905 W2 A 320 F X 1 q X 1 q X 1 q X 3 q X 1 q...
Page 6: ...6 1300905 W2 A 320 M X 1 q X 1 q X 1 q X 3 q X 1 q...
Page 12: ...12 1300905 W2 A a b 6 0 mm 2 1 3 0 mm 6 0 mm 3 0 mm 6 0 mm...
Page 13: ...13 1300905 W2 A 3 320 IC 320 IF Install the connections...
Page 14: ...14 1300905 W2 A 320 M 320 F 4 1 min...
Page 15: ...15 1300905 W2 A 5 3 0 mm 6 320 IC 320 IF Install the pipework a...
Page 16: ...16 1300905 W2 A 320 M b c 320 F...
Page 29: ...29 1300905 W2 A...