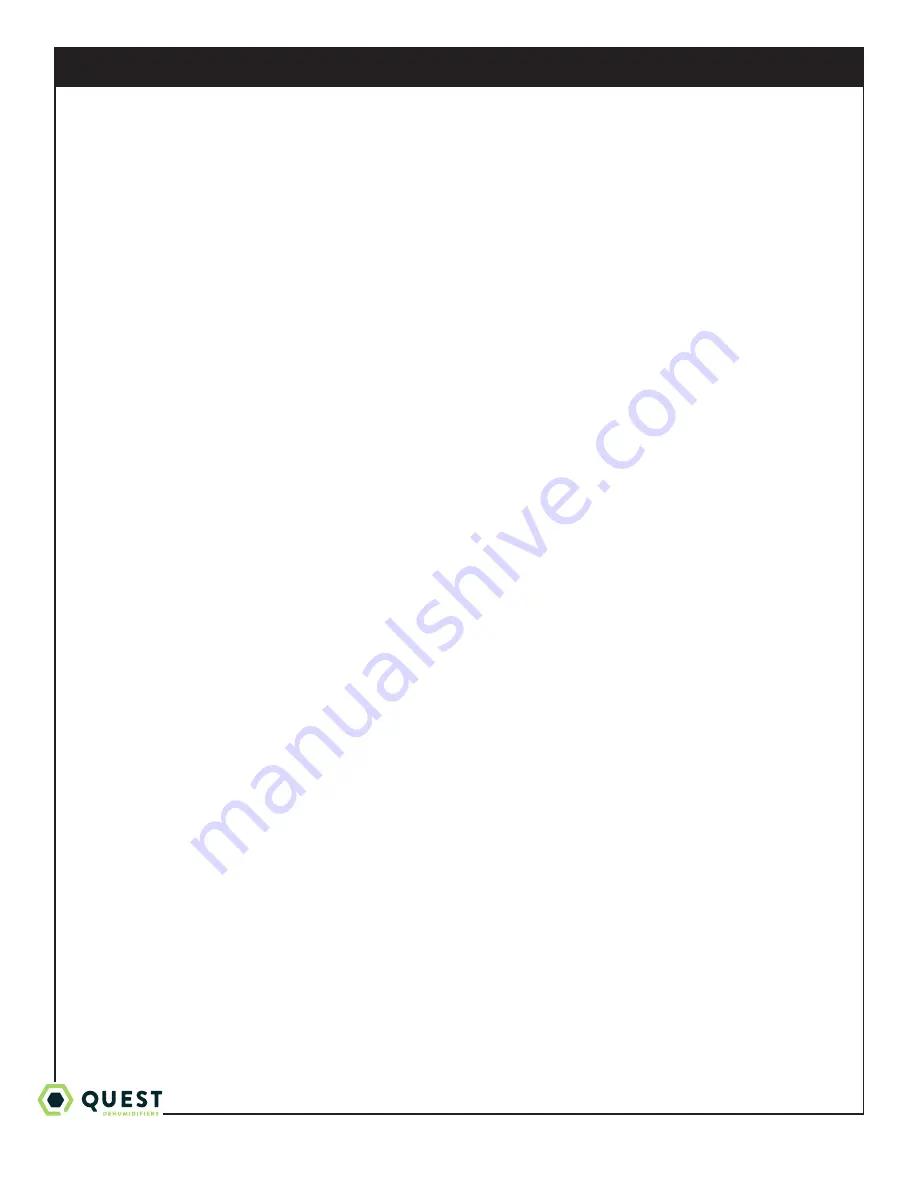
1-877-420-1330
Quest 215 Dual
Installation, Operation and Maintenance Instructions
14
www.QuestHydro.com
4. Compressor terminals C and S: No continuity indicates an open start winding. The compressor must be replaced. Normal start
winding resistance is 3 to 7 ohms.
5. Compressor terminals C and R: No continuity indicates an open run winding. The compressor must be replaced. Normal run
winding resistance is .5 to 2 ohms.
6. Compressor terminal C and overload terminal 1: No continuity indicates a defective overload lead.
7. Overload terminals 1 and 3: If there is no continuity, the overload may be tripped. Wait 10 minutes and try again. If there is still
no continuity, it is defective and must be replaced.
8. Compressor terminal C and compressor case: Continuity indicates a grounded motor. The compressor must be replaced.
9. Disconnect the wires from the run capacitor. Set the ohmmeter to the Rx1 scale. The capacitor is shorted and must be
replaced if continuity exists across its terminals. If there is no needle movement with the meter set on the Rx100000 scale,
the capacitor is open and must be replaced.
10. Reconnect the wires to the compressor and capacitor. Plug in and turn on the unit. If the compressor fails to start, replace the
run capacitor.
11. If the unit still does not start, adding a hard-start kit (relay & capacitor) will provide greater starting torque. If this doesn't work,
the compressor has an internal mechanical defect and must be replaced.
8.6B Replacing a Burned Out Compressor
The refrigerant and oil mixture in a compressor is chemically very stable under normal operating conditions. However, when
an electrical short occurs in the compressor motor, the resulting high temperature arc causes a portion of the refrigerant oil
mixture to break down into carbonaceous sludge, a very corrosive acid, and water. These contaminants must be carefully removed
otherwise even small residues will attack replacement compressor motors and cause failures.
The following procedure is effective only if the system is monitored after replacing the compressor to insure that the clean up was
complete.
1. This procedure assumes that the previously listed compressor motor circuit tests revealed a shorted or open winding.
2. Remove and properly dispose of the system charge.
DO NOT vent the refrigerant or allow it to contact your eyes or skin.
3. Remove the burned out compressor. Use rubber gloves if there is any possibility of contacting the oil or sludge.
4. To facilitate subsequent steps, determine the type of burn out that occurred. If the discharge line shows no evidence of sludge
and the suction line is also clean or perhaps has some light carbon deposits, the burn out occurred while the compressor
was not rotating. Contaminants are therefore largely confined to the compressor housing. A single installation of liquid and
suction line filter/driers will probably clean up the system.
If sludge is evident in the discharge line, it will likely be found in the suction line. This indicates the compressor burned out will
running. Sludge and acid have been pumped throughout the system. Several changes of the liquid and suction filter/driers will
probably be necessary to cleanse the system.
5. Correct the system fault that caused the burn out. Consult the factory for advice.
6. Install the replacement compressor with a new capacitor and an oversized liquid line filter.
In a running burn out, install an oversized suction line filter/drier between the accumulator and compressor. Thoroughly flush
the accumulator with refrigerant to remove all trapped sludge and to prevent the oil hole from becoming plugged. A standing
burn out does not require a suction line filter/drier.
7. Evacuate the system with a good vacuum pump and accurate vacuum gauge. Leave the pump on the system for at least an
hour.
8. Operate the system for a short period of time, monitoring the suction pressure to determine that the suction filter is not
becoming plugged. Replace the suction filter/drier if pressure drop occurs. If a severe running burn out has occurred, several
filter/driers may have to be replaced to remove all of the acid and moisture.
NOTE: NEVER use the compressor to evacuate the system or any part of it.