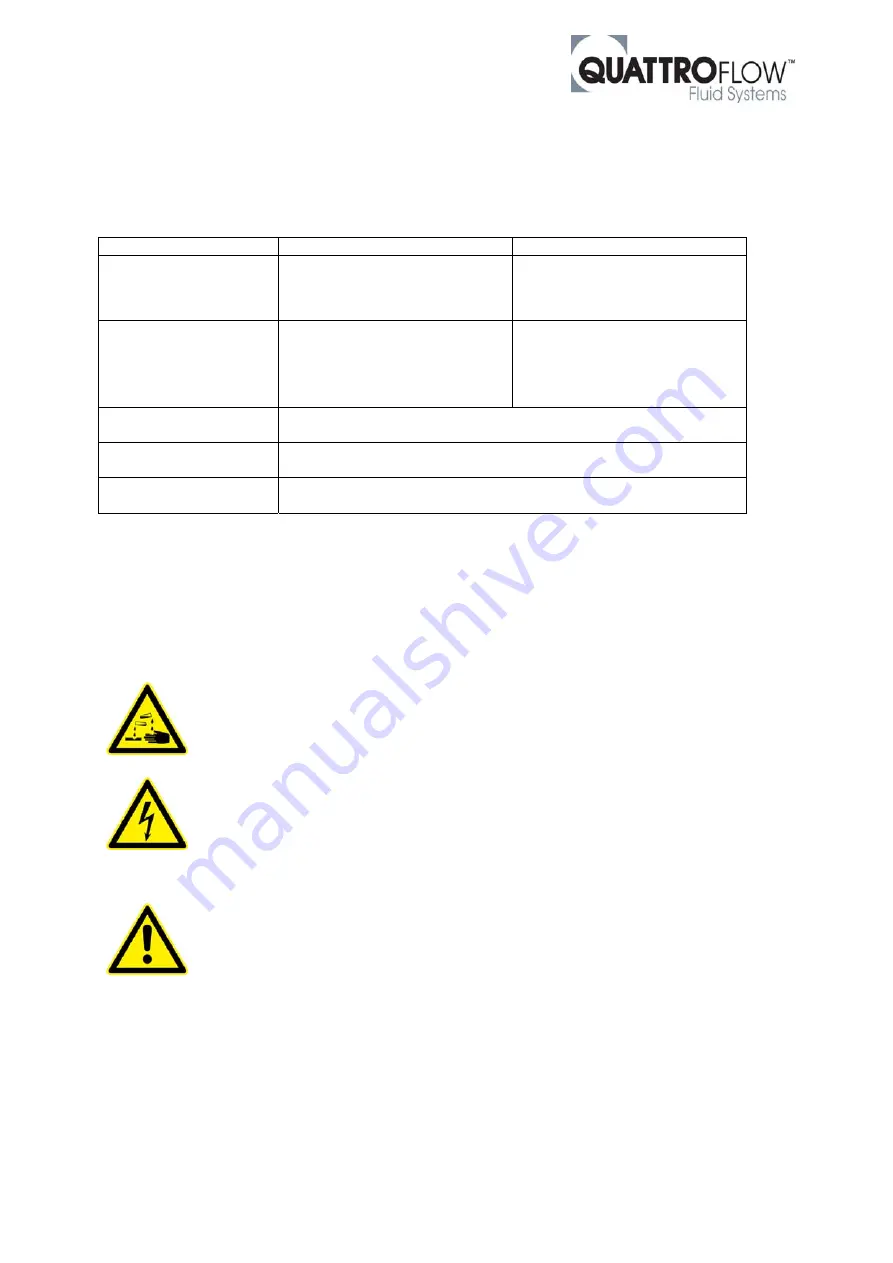
QF5050SU; edition 2016-05; page 11 of 18
4. Maintenance/Servicing of the QF 5050SU
Due to the robust construction the Quattroflow pump are widely maintenance-free. The ball bearings
do not need any extra lubrication.
We recommend the following maintenance intervals for the different pump parts:
Component Maintenance
interval
Action
Shaft-bearing-cap unit
1000 h operating hours,
at least once a year
Replacement of the complete
unit (kit order no.
PSKITWLC44)
Tension roller /
Drive belt
Once a year
Wear control (in case of
replacement: order no.
Q531053020 resp. Q6158.419);
Pay attention tot he belt tension
(chapter 4.2, image 6)
Motor
Pay attention to the maintenance information of the manual of the
motor
Coupling
Pay attention to the maintenance information of the manual of the
coupling
Gear
Pay attention to the maintenance information of the manual of the
gear
In case of a broken diaphragm the complete pump chamber should be replaced. In this case the ball
bearings of the drive shaft should be verified. For corrosion reasons or a clearly audible operating
noise the parts of the bearing service kit should be also replaced. (PSKITWLC44).
Tension roller (Q531053020) and drive belt (Q6158.419) with wear indications has to be changed
also. In general it is recommended to replace the elastomer parts whenever the pump chamber is
opened.
Please follow the general guidelines and safety advices when
handling with chemicals
.
Disconnect mains supply before opening the pump housing!
Basically, operations at the pump must be performed during standstill only. The motor
has to disconnect from the power supply, e.g. by pulling out the power plug or using a
repair switch, and has to secure against unintentional switch-on. This can be realized by
a lockable emergency switch. To prevent an accidental re-starting a danger sign should
be installed..
After purging the pump with air there might be a small residual
amount of fluid inside the pump chamber.
Flush the pump chamber thoroughly and check the rinse fluid.
The dismounting and mounting of the pump should be done on a
rigid table or work bench. Please note: the pump is heavy.
All further warning and safety instruction of chapter 3 has to be
respected.