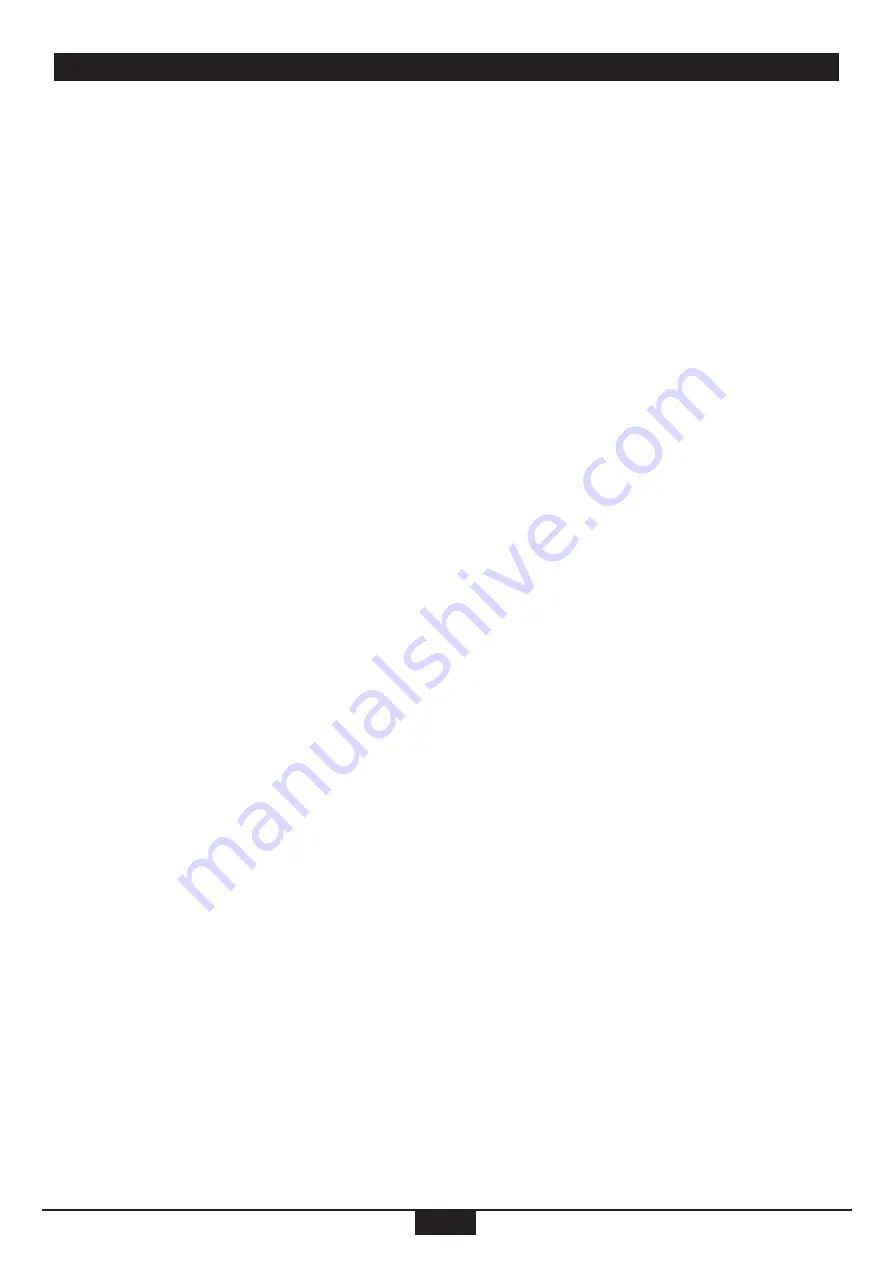
35
MAINTENANCE AND CARE
Date _______________________
Vehicle Owner’s Name __________________________________ Vehicle Identification # ____________________________________
o
Serial # of tiedown
o
Occupant Restraint ___________________________________________
1. The following items should be inspected and serviced by an experienced and trained technician during the scheduled
maintenance of the Q’Straint® 4-Point Wheelchair Securement System.
o
Clean all debris from floor anchorages.
o
Clean all retractors.
o
Verify that all manual release systems are functioning properly.
o
Verify that all electrical release systems are functioning properly.
o
Verify that all retractors are working properly.
o
Verify that electrical retractors are properly connected to vehicle’s electrical system and working.
o
Verify that fail-safe system for the electrical retractors are properly connected and working.
o
Verify that occupant securement system (shoulder and lap belts) are working properly.
o
Verify that all seatbelt systems are not worn or frayed. Replace as needed.
o
Verify that occupant securement system is not damaged or corroded. Replace if needed.
o
Verify that floor anchorages are not damaged or corroded. Replace if needed.
o
Verify that all mounting bolts are tight.
o
Inspect electrical retractors’ wiring for fraying. Replace any that have frayed.
o
Inspect all webbing for fraying. Replace any that have frayed.
o
Inspect entire system to make sure everything is working properly and replace anything that is needed.
2. Any deficiencies shall be noted below and rectified before the Q’Straint® 4-Point Wheelchair Securement System is released
to the consumer for use.
3. If the repairing technician has any issues not covered by this document or is not clear on what corrective action needs to be
taken, they MUST consult the nearest Q’Straint® office listed on the back page of this manual.
Deficiencies Noted: ________________________________________________________________________________________
_________________________________________________________________________________________________________________
________________________________________________________________________________________________________
Action Taken: _____________________________________________________________________________________________
_________________________________________________________________________________________________________
_________________________________________________________________________________________________________
Dealership: ________________________________________ Technician: ___________________________________________